
Sign In
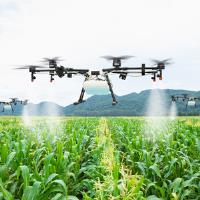
Industry commentators point to the 2020s as being the decade for Industry 4.0 to really take hold. In multiple sectors of the economy, large strides in technology are changing the way businesses operate and how we live: moving towards an Internet of Things approach where Machine-to-Machine communication facilitates complex and reactive pipelines.
This “fourth Industrial revolution” is taking its hold in the agricultural sector too: with one tool driving this change and providing a generational leap in farming efficiency for those with the foresight to buy in: the industrial unmanned aerial vehicle (UAV)… or more commonly known as the drone.
The majority of drones in the industrial sector take the form of nimble quadcopters or hexacopters where either four or six powerful rotors power a UAV that uses six-axis stabilisation for precise programable motion. Initially geared towards the realm of the recreational “drone enthusiast”, the fall in the cost of drone technology now makes it viable for use in industry to improve automation and data collection.
One of the most popular applications for drones in farming is surveying land and collecting and interpreting data. This is where high resolution (up to 4K) cameras come in to play. Usually installed on a pivoted support system called a “gimbal”, camera drones can be used to scan large swaths of farmland and with mobile networking, this information can be sent in real-time to a technician’s computer for analysis.
Farmers can use drones to identify crop health and map growth patterns. They can also be used for surveillance to track wildlife (with the added benefit of a noisy quadcopter having the ability to scare away any rabbits!).
For livestock farmers, camera drones can be used to easily get a top-down view of dozens of acres of land at a time, allowing for farmers to achieve detailed tracking of herds.
Fitting drones with infrared cameras allows farmers to see their livestock through dense overgrowth or woodlands, and the ability for drones to sync in real-time to a central database means farmers are able to use GPS ID fitted collars to track specific animals, allowing for seamless unmanned management of livestock.
Another important use case scenario for drones in agriculture is to facilitate heavy lifting. Researchers at the Georgia Institute of Technology have developed a way for centrally controlled “swarms” of drones to use co-operative flight to lift payloads of up to 5kg. Once streamlined, these academics hope to roll these drone swarms out to industry, where farms can benefit from the reduction in heavy-lifting labour.
Whilst companies like DJI are pioneering the way forward for standard, off-the-shelf drones, with products like the DJI Mavic 2, for large industrial applications, system designers may enjoy the flexibility of designing a drone themselves. If your business is looking to construct your very own specialist drone equipment, its very important for durability, longevitity and safety that you get the power components right for both your drone and your base charging station.
Power
A small electric drone needs between 2-200W per KG to fly. The power consumption requirement increases with any added weight – for example if you’re looking to create a spraying drone, more powerful propellors would be needed to offset the added mass of a water tank.
Specialist equipment like flashlights, infrared cameras or thermometers may also increase the power consumption, so a beefier, higher power output component may be needed for the power architecture of the drone.
For simple, low power requirement drones, power components like the small Cincon ECLB40W-110 is perfect for on-board power management. Rated for use in railway application, Cincon boast great shock and vibrance resistance, increasing the component’s longevity fitted to a drone. Delivering up to a 40W power output, this power supply is perfect for drones that need to pack some oomph, for example surveillance drones, and its micro form factor makes it perfect for keeping the size and weight of the drone’s electrical components down.
For larger, beefier drones that’ll need a high power input, the Cincon CQB150W-110S is a high power output power supply that may fit your desired system. With the EN50155 approval for rail and rolling stock testing, this sturdy power supply can handle the shocks and knocks of a drone falling out of the air without breaking a sweat. With an output of up to 150W, this is perfect for a system designer looking to create a drone behemoth, and its form factor as a shielded quarter brick keeps the component shielded from the elements whilst making it easy to fit with a DC battery with ease.
As for charging base stations, we’re looking at power components that’ll be able to provide high power outputs and can withstand the elements to stay outdoors. That’s where DELTA’s panel-mounted low profile supply shines. Delivering up to 150W of output power and coming with conformal coating as standard, this is a great PSU choice for base stations. Meeting the shock and vibration requirements of IEC 60068-2-27 and IEC 60068-2-6 respectively, and with a wide operating temperature range of -30°C to +70°C, this power supply can withstand the worst farmers can throw at it.
ARTESYN also offers a great PSU with good environmental endurance with their high power LCC series. With outputs of up to 650W, the LCC is great as a central power supply for a multitude of charging pads, and the IP64 ingress protection allows the component to face the elements with ease. These power supplies are conduction cooled, increasing longevitity by reducing moving parts, and support for the PMBus digital control protocol allows for system engineers to create routines and remotely manage the power output of the charging system: improving efficiency.
For more information on The rush to power these revolutionary agricultural drones talk to Components Bureau
Enquire Now
More News
List your company on FindTheNeedle.