
Sign In
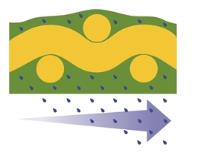
The importance of drying:
All CPS Ultra Coat emulsions (especially the Diazo sensitised ones) require complete and thorough drying before exposure to give the strongest stencil. If the screens are not dried properly the stencils will be soft, easily damaged and will quickly break down during printing.
It may seem simple, but the way the screen is dried can have a huge effect on the final result. There are three main factors of equal importance to consider; (i) temperature (ii) humidity and (iii) air movement.
Temperature- There is a temptation to use high temperatures to dry the stencil as quickly as possible, however Diazo sensitisers are temperature sensitive and the higher the temperature the quicker they will decompose/react. The first symptom of high temperature drying is a slow, difficult washout and a loss of resolution. In severe cases, the stencil will be completely insoluble and won’t wash out at all. Therefore we recommend a maximum drying temperature of 35°C.
#ScreenPrintingTopTip: As temperature is so important, it is good practice to check monthly that the temperature in the dryer is actually the same as indicated on the control panel. If your frames are too hot to touch when they come out of the dryer, the temperature is much too high!
Humidity- In some ways humidity is even more important than temperature, as it controls the amount of water that can be absorbed by the air in the dryer. Each summer some printers working in a warm, humid environment suffer screen breakdown during printing which is directly caused by poor screen drying. Consequently screens have to be remade, presses are down and there is high cost to production.
The reason for the breakdown is because the Diazo sensitiser reacts with the water in the screen rather than the polymer, resulting in only a partial hardening of the emulsion and therefore a soft, weak stencil.
Always aim for a Relative Humidity of less than 50% for drying, as the lower the humidity, the more water the air will hold and the quicker the screen will dry. A digital hygrometer (shown above) will tell you exactly what the ambient relative humidity (RH) is.
#ScreenPrintingTopTip: When drying screens in a humid environment such as a hot, humid climate, or a sealed drying chamber where many screens are drying at the same time, installing an inexpensive de-humidifier can dramatically improve the drying. Costing less than $300 these units can dramatically speed up production and prevent costly breakdown on the press.
Air movement - Having a constant movement of warm, dry air over the stencil will give the most efficient drying as it blows away the wet air directly next to the emulsion. However, if that air is contaminated with lots of particles of dust then you will end up with a dry, but useless screen! A gentle movement of filtered air is the best compromise.
For best results use warm, dry, filtered air to evaporate the water from the stencil
Recommendations:
Drying cabinets- Purpose built drying cabinets are the best tools for drying screens as they create the perfect environment for drying screens efficiently and consistently.
A good drying cabinet will have the following features: (i) be light-safe, (ii) have thermostatically controlled temperature, accurate to + 1°C, (iii) have gentle air movement, (iv) filtered air, (v) exhaust the wet air and draw in dry air and (vi) allow the screens to be dried horizontally with the squeegee side uppermost. Picture courtesy of Natgraph.
CPS Ultra Coat emulsion screens should always be dried horizontally with the squeegee side uppermost to allow the emulsion to settle on the print side of the screen. If the screen is dried vertically, there is a chance that the emulsion could run before it has started to dry which can cause visible 'curtaining' of the emulsion, or a higher stencil thickness (EOM) towards the bottom of the frame.
How to check if it is dry- To tell when the screen is ready, it should feel dry to the touch with a non-sticky surface. However a more accurate way is to use a moisture meter that is accurate below 5%. Please note that some dual cure emulsions still have a slight surface tack even when dry e.g. CPS Ultra Coat 535, CPS Ultra Coat Viking and CPS Ultra Coat Triton.
Other elements to consider- One other aspect of the drying process that is often overlooked is the effect that temperature has on dimensional accuracy. For example a 1m x 1m Aluminium frame dried at 40°C will be 440 microns larger in each dimension than it was at 20°C room temperature! This highlights the need to allow screens to always return back to room temperature before they are exposed. Always expose the screens at the same temperature at which they will be printed.
Storage of unexposed screens- All screens must be stored in ‘safe’ conditions before they are used. The temperature should be 20°C or lower and the humidity kept low. The screens are sensitive to UV light, so must be stored in a dark or yellow safelight area. Most screens will start to fog (expose) in less than 20 seconds if exposed to daylight and projection speed emulsions such as CPS Ultra Coat CTS L or CPS Ultra Coat Neptune will fog in less than 1 second.
You can use the following text as a safelight check. If you can read this yellow text in your screen making area then your safelights are not safe.
Unexposed screens have a shelf life of up to three weeks when stored at 20°C/50% RH which will be dramatically reduced if stored hotter or at a high RH.
Summary:
Insufficient screen drying is one of the top three most common reasons for stencil failure, next to mesh preparation and under-exposure, but it is probably the least recognised. Drying a screen properly is quite straightforward and will save you significant money in the long term by reducing the number of on-press breakdowns.
For more information on Drying CPS Ultra Coat emulsion stencils talk to CPS - Chemical Products and Services
Enquire Now
More related to Drying CPS Ultra Coat emulsion stencils
List your company on FindTheNeedle.