
Sign In
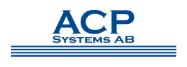
Simon Jones, Global Screen Business Manager, highlights the importance of using screen printing chemistry that is safe for both users and the environment.
Screen printers are under increasing pressure to both protect the health and safety of their employees and reduce their impact on the environment as new legislations continue to be passed. While many companies take a responsible approach to each of these issues, many perceive them to be secondary concerns when margins are tight and money is scarce. In reality, when it comes to choosing screen cleaning technology and solutions, safety and efficiency often go hand in hand.
Companies also have a legal responsibility to dispose of the chemicals properly and where potentially harmful chemicals are used, this can be problematic and expensive requiring the use of verified outside contractors.
Greener chemistry
Navigating the maze of legislation can be complex and time consuming, which makes the use of safer chemicals all the more appealing. The latest screen cleaning solvents have been developed to be safer for both users and the environment and often require no hazard labelling.
Unlike many cheaper options, high quality cleaning solvents have low flammability to reduce the risk of fire and no harmful chemicals to minimise the chance of dangerous accidents. Furthermore, low evaporation and low odour make the products far more pleasant to use.
The latest generation of safer screen cleaning chemicals are also better for the environment, as they can be disposed of more easily and cheaply, with minimal risk of environmental damage.
Cleaner results
With even the most persuasive safety and environmental benefits, screen cleaning products still need to be up to the job. While customers are increasingly concerned about the green credentials of their suppliers, they ultimately want to work with a company that they can rely on to deliver consistently good results. For a screen printer to provide this high quality service, often to tight deadlines, the cleaning chemicals chosen must be effective, reliable and affordable.
Cheaper chemicals may be chosen to keep costs down however, these products are rarely able to provide effective cleaning. For instance, they typically evaporate quickly; at a rate 20 times faster than water and 100 times faster than a low volatility product. This makes it impossible for them to remain on the screen and in contact with inks and residues for long enough to deliver satisfactory results. More chemicals are then needed to get the screens clean and more wipes required, escalating costs, creating unnecessary waste and more hazards for the users.
Re-useable solvents
High quality, safer chemicals can also provide opportunities for re-use in re-circulation. Re-circulation systems are available that allow ink solids to be separated effectively from the solvent screen wash, increasing the working life of the solution and keeping waste down. Modular stainless steel re-circulation units can be used alongside manual or automatic screen cleaning units to allow users to get more from their solvents and save a considerable amount of money.
In summary
While increasingly tight margins make it tempting for screen printers to choose the cheapest possible products available, these are rarely the most cost effective or reliable choice in the long term, and screen printing chemicals are no exception. Cheaper solvents are not typically developed with user safety, the environment or consistently effective cleaning in mind.
By choosing safer, high quality solvents these issues can be eliminated leaving screen printers to focus on providing a quality service to their customers. Rather than making printing applications more expensive, working with safer, more environmentally friendly chemicals can actually be a sound commercial decision as well as an ethical one.
For more information on Safer Screen Cleaning Makes Good Business Sense talk to CPS - Chemical Products and Services
Enquire Now
List your company on FindTheNeedle.