
Sign In
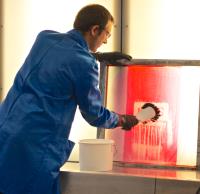
Clean water and good sanitation is taken for granted by millions of people in the ‘developed’ world. We simply turn on a tap for clean drinking water and allow it to wash into a sewer for treatment in some unseen facility. We also expect to walk alongside unpolluted rivers and waterways that are full of fish and wildlife.
This has certainly not always been the case and during periods of industrialisation our environment and waterways have suffered from the effects of pollution. Waste water is now a hot topic but legislation and policies on this subject are also some of the most difficult to understand. The purpose of this article is to offer a practical guide on some of the issues related to screen making chemicals and how they can impact on waste water.
What Regulations Apply?
Waste water regulations are probably the most diverse set of ‘environmental’ standards, as different rules apply at EU, Country, Regional and Local Authority levels, they also differ by Water Company and even individual building. From our own experience we’ve established that the closer you are to the waste water treatment plant the stricter these limits can be. It is also likely that your business has different ‘consent limits’ for waste water compared to your neighbours, depending on the nature of their work.
The most important thing is to establish exactly what regulations apply to your business and your Water Company can advise you on this. If you are discharging effluent into a sewer you will require a ‘trade effluent consent’ and you will be given strict ‘consent limits’ for a range of parameters. Your Water Company may require you to conduct periodical monitoring of your waste water or they may choose to conduct their own ‘spot checks’.
Needless to say, non-compliance is a very serious issue and penalties can range from improvement notices, fines, or prevention from discharge into the drains which would necessitate all water being collected for disposal as ‘chemical waste’ at huge cost and inconvenience to the business.
Making Sense of the Terminology
The consent limit stipulates what and how much ‘trade effluent’ you are allowed to discharge into the drains. This is made up of many key properties of waste water that the Water Company treating the water will be concerned about i.e. maximum daily volumes and discharge rate, pH, COD (Chemical Oxygen Demand), Solids, Temperature etc. It will also stipulate the types of chemicals that are allowed down the drain, for example any substance likely to produce flammable or harmful vapours (such as petroleum spirits and some aromatic hydrocarbons) are unlikely to be permitted to enter a public sewer.
Additionally, the consent limit typically applies to the specific source of ‘industrial effluent’ which in the case of screen printers may be a screen cleaning machine or the booth used to develop stencils. Therefore, other waste water from sources such as toilets, kitchens and wash rooms are excluded and it is not possible to ‘dilute’ the trade effluent with these other sources, even though they will most likely end up in the same sewer.
Typical example of consent limits values could be:-
COD: <2,000 mg/Litre
pH: 5 to 10.
Water temperature: <43°C.
Solids: < 1,000mg/Litre (i.e. 1 gram/Litre)
In our experience COD (Chemical Oxygen Demand) is the most misunderstood parameter and the one that causes most problems with effluent from the screen making process. It is a measure of how much oxygen is required to break down the ‘waste’ materials in the water at the treatment plant. Many sewage treatment facilities use a cocktail of bio-organisms to ‘feed’ on the waste, but if the COD in the water is too high they will run out of oxygen and die. Different treatment plants have different requirements and one of the issues the Water Company needs to deal with is optimising the incoming COD levels to ensure the bio-organisms are ‘fed’ at the right level. In Scandinavian regions, for example, many treatment plants are optimised for high COD levels and other factors such as ‘nitrification’ of the water are highly critical. In other regions low COD values are preferred.
Unfortunately, screen making materials such as emulsions and fillers have a relatively high COD of around 1,500,000 mg/Litre. So each litre of emulsion that goes down the drain needs 750 litres of clean water to reduce the COD to 2,000mg/Litre, which is a common industrial effluent limit! Simple measures such as scraping as much out of the coating troughs prior to cleaning will reduce the amount that goes down the drain and lower your COD and solids.
pH is a measure of acidity or alkalinity and is a number on a logarithmic scale from 0 to 14, with 0 being highly acidic and 14 being highly alkaline. Water and ‘neutral’ materials have a pH close to 7. Acids and Alkali’s neutralise each other so it is possible to use different materials with high and low pH and achieve a ‘balanced’ neutral discharge – more of that later.
Solids content in waste water is a simple measure and not normally an issue within our industry.
Drain Safe is Okay, Right? - Wrong!
‘Drain Safe’, actually means the product does not knowingly contain any chemicals that are banned from entering the waste water system, it doesn’t guarantee compliance and therefore should not be assumed is okay. For example, releasing too much hot water into the drains would be non compliant, even through the water itself is 100% ‘drain safe’! Don’t panic, there are simple measures to minimise any possibility of a non compliance, especially if you understand how the processes of screen cleaning and screen making affects the waste water and you select the correct cleaning chemicals.
Screen Making
All emulsions, capillary films and fillers coated onto the screen will eventually end up in the waste water, either as unexposed emulsion washed out after exposure, or during the decoating process after printing. They also have high COD values. A single screen with 1m2 coating of emulsion on a 120/cm mesh would have a COD of up to 150,000mg/Litre and would require around 75 Litres of water during washout and decoating to get the waste water COD to below 2,000mg/Litre.
Screen Cleaning and Ink Removal
The waste water from this process may be neutral, acidic or alkali, dependant on the ink type. The ink and screen wash used will contribute to the COD, with both individually having a COD of approximately 1,500,000 mg/Litre. The ink will also contribute to the solids content of the waste water. The most important step you can take is to scrape as much of the ink from the screen before cleaning, particularly if using plastisol inks. This will reduce the COD, the amount of solvent needed to clean the screen (also reducing the COD), and the solids content of the waste water.
Using a water dilutable cleaning solvent such as an Aquawash, offers a significantly lower COD level than a general purpose screen wash. An Aquawash diluted at 1:1 with water will have a typical COD value of 750,000mg/Litre, diluting at 2:1 with water will reduce this to 500,000mg/Litre. Processes where the cleaning solvent is recirculated in automatic cleaning machines and manual cleaning booths can also significantly reduce COD levels in waste water.
Stencil Removal
The waste water from this process will always be acidic. This is due to the nature of the raw materials in the stencil remover used to breakdown the emulsion. The pH of stencil remover once diluted (at the correct ratio) or in a ready to use format will typically have a pH of 2. However, as the chemicals used in the stencil remover are inorganic, they will not contribute to the COD of the waste water. If pH is an issue, the waste water from the stencil removal stage can be ‘neutralised’ by holding back the water in a tank and adding waste water from the haze removal stage prior to discharging to the sewer.
Haze Removal
The waste water from this process will always be alkali due to the caustic chemicals used in these types of cleaning products. Using lower caustic haze removers, and those that can be left on the mesh overnight to dry, can minimise the pH of the waste water from this process. If you want to reduce the COD, apply the minimum amount of haze remover and if possible use a coating trough to apply the haze remover to the mesh. The pH of this process can be neutralised by holding back the waste water in a tank along with water from washing out and decoating screens prior to discharging to the sewer.
Equipment Solutions and Waste Water Treatment
“Prevention is better than cure” and treating your own waste water on-site should be seen as a last resort if all other steps have been taken to meet consent levels. Many print facilities have been forced to install waste water treatment for different stages of the process due to high volumes or very demanding local regulations.
Always take expert advise and be clear on what you are trying to achieve and why. Again, your local Water Company can probably offer good and impartial advice.
Various approaches can be used to treat waste water in-house, prior to discharge. These include settlement tanks, chemical treatment (pH adjustment, flocculation and coagulation), filtration and carbon absorption of organic materials. Many printers fall into the trap of purchasing complex equipment which will ‘over-treat’ their waste water, i.e. remove solids through flocculation/coagulation and filtration and adjust the pH level when all that is required is pH adjustment to ensure compliance.
Review your processes
Even through you may have never had a problem with your Water Company in the past, regulations are becoming tougher and more efforts are being made to enforce them. Take an honest look and appraisal of your cleaning operation. If you have concerns or “think it looks wrong” then it probably is. Better to take steps now than wait for a knock on the door telling you that you need to clean up your act!
Understanding and knowledge is key to this and a few small changes to the products you use or the processes you follow can make a significant difference. Who knows, you might even save yourself some time and money in the process.
To help with the review we have produced our own table as a guide, a copy of which can be downloaded by clicking here. It details generic screen making and screen cleaning products and what properties they have with respect to waste water. Products used should be compared to the ‘generic’ classification in the table, in many cases, it may be possible to select an alternative one with lower impact on waste water.
For more information on Waste Water – Practical Advice for Screen Making Chemicals talk to CPS - Chemical Products and Services
Enquire Now
List your company on FindTheNeedle.