
Sign In
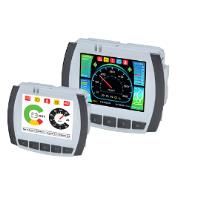
Yes, Curtis CANdo.... part 2
Engineers working with different CAN devices are often frustrated that some fail to communicate with others due to conflicting CAN “languages” and entirely different 29-bit CAN protocols such as SAE J1939, often forcing designers to approach manufacturers for modifications; this can be expensive and time consuming and result in the creation of non-standard parts with higher pricing, negatively impacting on new vehicle profitability.
In CANdo part 2, we learn how one flexible solution helped overcome this exact situation.....
Control conflicting languages with a CAN interpreter
Part 1 explained how Curtis AC motor controllers act as CAN language interpreters for different devices on the bus when employed as the electric traction or hydraulic pump motor controller, so costly modifications are not necessary.
By using the controllers standard inbuilt (VCL) software to configure the CAN data, the vehicle designer can either rely on the proven VCL functions Curtis has predefined, or quickly and easily write proprietary functions and algorithms. Choosing the latter will differentiate the control system from the competition (and in consequence, the functions of the vehicle), with the goal of creating a marketplace advantage.
Application example illustrates advantage of VCL
One vehicle developer was in the process of designing a special electric forklift truck for handling long loads. The design required a remote seating position within a rotating cab that would provide the operator with a clear view of un/loading operations, and also face the direction of travel to offer a safe, clear field of vision. Mechanical linkages or hydraulic hoses would be very problematic in such a configuration, hence the need for electronic fly-bywire CAN control of all vehicle functions.
The vehicle developer was very specific that the steering had to simulate the feel of a hydrostatic steering system. This limited the devices for the man-machine interface meaning the developer had to choose a device that only ran a custom version of 29-bit CAN. Hydraulic control and vehicle direction inputs were handled by a dual-axis joystick running a ‘proper’ SAE J1939 CAN protocol.
A Curtis enGage VII colour LCD instrument was chosen to provide battery status and steered wheel position indication, together with comprehensive on-vehicle diagnostics and real-time monitoring of all critical vehicle information and vehicle speed. This product, together with the Curtis Model 1222 EPS AC steering motor controller and two Curtis Model 1236 AC motor controllers (one driving the truck’s electric traction motor, the other the hydraulic pump) ran 11-bit CANopen.
The final selection of control devices meant that three different protocol types had to be matched. The vehicle developer thought that a separate (and expensive) CAN system master module would be required to pull the three protocols into line, and asked for Curtis UK’s customer support engineers for help.
Within an hour of arriving on-site, the Curtis engineer had set the Model 1236 AC traction motor controller as the system CAN Master. The individual ‘mailboxes’ in the Model 1236’s software were configured to handle the 11-bit CANopen, 29- bit J1939 and 29-bit OEM-specific protocols. This configuration, easily implemented in the standard AC motor controller, allowed multiprotocol data to flow seamlessly across the network while maintaining the minimal two-wire twisted-pair CAN cabling.
The mailbox data format that adjusts the system to individual needs is fully flexible and may be configured for the transmission of 8-, 16- or 32-bit data by adding the +UseHB (Use High Byte) function. In this way, 16- bit data words sent across the CANbus as two 8-bit bytes are automatically combined back into a 16-bit word by the mailbox. Importantly, the use of the Curtis Model 1236 AC traction controller as the CAN Master completely eliminated the need to add an additional ‘vehicle manager’ device. This functionality was effectively embedded in the traction motor controller’s VCL software, an approach that ultimately provided the vehicle developer with a considerable reduction in system cost and complexity.
In part 3, read about the other interesting functions that characterise the Curtis AC motor controllers.
For more information on How to convert different CAN protocols to a common langauge talk to Curtis Instruments (UK) Ltd
Enquire Now
List your company on FindTheNeedle.