
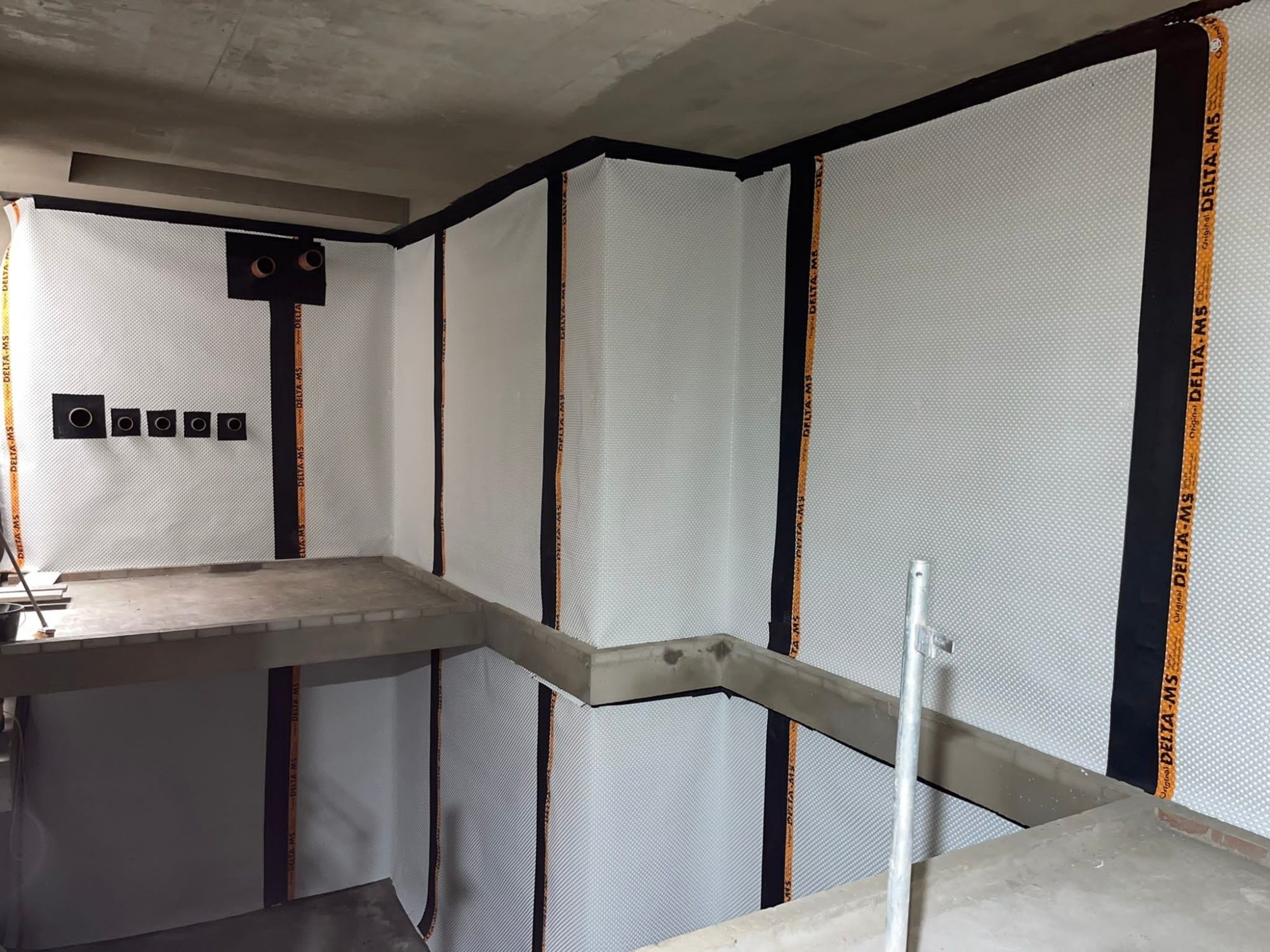
Overview
Delta Registered Installers, Onyx Basement Services were appointed to assist on an exciting new development, in London. The project scope was to offer waterproofing design and installation to a large-scale below ground project consisting of a 3-storey deep basement to a residential building, once complete will comprise of fifty-nine residential units, along with a communal gym and cinema room.
One of the challenges faced when designing a suitable waterproofing system for a multiple residential building is compartmentalization of separate units in a single basement space. This can cause challenges from a waterproofing design perspective in maintaining continuity of the system.
Using a fire retardant, Type C, membrane system enables the waterproofing designer to keep the waterproofing system continuous between adjoining basement properties whilst dealing with the issue of spread of flame from one property to another.
When designing the most appropriate waterproofing system to any given situation, various design factors will need addressing such as (but not limited to), final use of the building, the grade of waterproofing requirement (British Standard 8102), Approved Documents, structural considerations based on the form of construction, ground conditions, and in some cases, satisfying the requirements of building warranty providers.
The project required a robust and a meticulously detailed specification.
Methodology
When designing a robust waterproofing solution, attention to detail is critical. As with all new build projects, waterproofing designs should incorporate BS 8102:2022. Protection of below ground structures against water ingress. Code of practice.
Two forms of waterproofing, often referred to as ‘combination waterproofing’ can offer optimal structural protection against water ingress. Combination systems can offer solution to convoluted/difficult shapes to waterproof. A combination favoured by Delta Registered Installers is A liquid/cementitious (Type A) system which can be lapped behind a Type C (cavity drained system), to provide continuity of the waterproofing design.
For this project, a Type A and Type C, fire retardant system was recommended.
Prior to the installation of the fire retardant, Type C System, Koster NB1 waterproofing slurry was applied to the structure. Used with an additive (Koster SB Bonding Emulsion) Onyx were able to increase the elasticity and flexibility of NB1 along with reducing any water absorption of the slurry.
To reduce the risk of free lime leaching out from the new concrete (during the curing process), Koster Polysil TG 500 was applied to the entire face of the concrete lining wall.
An area of potential weakness (where moisture could penetrate the structure) in a below ground structures is the wall/floor junction. Fillets were created using Koster Repair Mortar Plus (a unique expanding waterproof material) to keep these important junctions protected and watertight. The coved fillets were further waterproofed using two coats of Koster NB1 to create a robust waterproofing solution.
After ensuring the structure was watertight, Delta MS 500 Fire Retardant cavity drained membrane was installed to the walls.
Cavity Drained Systems manage water penetration, Delta drainage channel, a water collection conduit designed to control water ingress was bedded into a preformed recess/gully at the floor/wall junction with incorporated inspection and maintenance points to comply with BS8102:2022.
Prior to the installation of Delta MS20 membrane, the basement slab was thoroughly flood tested.
The project required bespoke sump pump units to remove large volumes of ground water, foul water, and grey waste. Locations of the sump pump units were suggested during the design phase.
For more information on WATERPROOFING DESIGN AND INSTALLATION talk to Delta Membrane Systems Ltd - Basement waterproofing