
Sign In
Ultimate Guide To Pallet Racking
23-09-2021
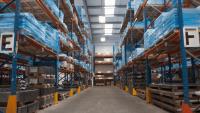
Choosing and installing the right form of pallet racking is crucial. Selecting an unsuitable rack or getting it mounted incorrectly will adversely affect the profitability of your warehouse so it’s something that must be considered carefully. Here we direct you through 10 easy-to-follow steps to ensure that you get your pallet racking right from start to finish in our ultimate guide to pallet racking below.
Consider Your Pallets
The first thing you need to think about is your pallets. The items you store will decide the size of the pallets you’re going to use, and eventually the size of the racking you’re going to need. You should also know how many pallets you need to store your entire stock. Based on the type of stock you hold, you will need to determine if regular pallets or composite pallets are better suited.
The Warehouse Layout
The shape, size and height of your storage warehouse, as well as the location of the entry points, exit points and windows, will also need to be considered when choosing the type of racking to be used.
Workspace management specialists like Avanta UK will be able to carry out an in-depth study of the capabilities of your warehouse and provide you with ways to enhance the layout, functionality and operations of your warehouse to give you the most effective working atmosphere.
Choosing Your Racking & Storage Systems
Depending on the industry in which you work, you may need to determine which type of racking to use. Some of these include the following:
Wide Aisle Racking
Usually, the most common type of rack, wide aisle is simple to mount, flexible and relatively inexpensive. Through adjustable beams, this rack can handle changing warehouse configurations and business models and provides convenient access to forklift traffic.
Narrow Aisle Racking
This form of racking is suitable for retail, food & beverage, manufacturing and construction warehouses. These are usually built where floor space is restricted – by optimising the height at which the goods are stacked and stored.
Double Deep Racking
This rack does as it says on the tin; it provides twice the depth for storage, thereby reducing the number of aisles available. Double-depth requires a special lift fork with either an extension or a side fork configuration.
Drive-In Pallet Racking
Also known as the Pallet Shuttle, this is one of the most space-efficient racking models available on the market. Drive-in racking will increase the capacity by up to 80% over traditional rack by allowing pallets to be placed on guide rails in the centre of the rack on which forklift trucks will drive through.
Pallet Live Racking
Live racking systems operate on a first-in, first-out basis
and deliver an incredibly efficient degree of storage capacity.
In the case of live pallet racking, pallets are loaded onto rollers
which are placed at a set gradient to allow stock rotation and control.
Shuttle Racking
This is a deep lane storage and retrieval system, which has rechargeable batteries and is useful for managing whole pallets, processing in batch quantities and replenishing order pick-up tunnel systems. This method of racking is best used in cold stores and can work as the first in, the first out or the last out of the network.
You can take a look at our full selection of pallet racking by heading over to our Product Range.
Choosing The Most Suitable Lifting Trucks For Your Racking
Depending on the nature of your service, you may need to think about which vehicle is better suited to operate in accordance with your racking system(s). There are three types of widely used warehouse vehicles:
Counterbalance Forklift Truck
Typically used for unloading goods in and out of the warehouse. They are available in either battery, gas or diesel-powered to suit your exact needs.
Reach Truck
This vehicle is most widely used for loading and pick-up from standard rack types, e.g. Wide Aisle, Double Deep Racking.
Narrow Aisle Turret Truck
There’s a hint in the description. This machine is designed to work alongside a narrow aisle rack. Trucks that are very Narrow aisles are also an option.
Safety Considerations
To avoid accidents, you must show the appropriate safety and danger signs around your warehouse, particularly when it comes to loading and picking. For starters, emergency exits must be properly signed and free from obstructions.
Barrier rails should also be considered to reduce the effects of forklift collisions, walkway security barriers to protect passers-by and pallet rack protectors from preventing damage to the rack.
It is also critical that you clearly identify different areas such as walkways and loading bays with colour-coded line-markings.
If you would prefer for us to come out and install the racking systems or carry out a relocation – head over to Our Services page for more information on how we can assist you.
Which Aisle Orientations Is Best?
First, it is essential to remember that the exterior dimensions of your warehouse should be similar to 2:1. This will mean that you have the full versatility of the internal layout, that you have more room for building expansion, and that you have more options when it comes to aisle orientation.
The most popular (and reliable) forms of rack orientation are:
Fishbone
This principle consists of the central aisle being vertical to the length of the rack parallel to the length of the rack.
Hair Comb
The central aisle is parallel to the length of the racks, vertical to the length of the racks.
Whatever orientation you pick, be sure that the rack does not block any fire escapes. The use of professional workspace design consultants such as Dexion Anglia LTD would ensure that the design, arrangement and movement of products are introduced with health and safety remain at the forefront of your warehousing operations.
For more information on Ultimate Guide To Pallet Racking talk to Dexion Anglia Ltd
Enquire Now
List your company on FindTheNeedle.