
Sign In
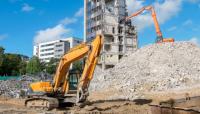
Recycling
Given the ever-increasing awareness of the environmental impact of construction and the desire to preserve the world’s resources, there is an onus on manufacturers to ensure their products can be recycled where possible when they reach the stage where they are no longer usable in their current form, known as end of life.
The use of recycled aggregates
A focus on recycling across a broad spectrum of industries in recent years has naturally led to the question of what concrete manufacturers are currently doing to ensure the re-use of aggregates where possible, and what more they could be doing in the future. There is a pressure upon all businesses to look at increasing sustainability through the introduction of a higher proportion of recycled aggregates.
Currently around 200 million tonnes of aggregates are used across the UK every year as raw construction materials, of those around 57 million tonnes (or 28 per cent) derives from recycled or secondary sources.
The Mineral Products Association reports a ‘public will to reduce the use of primary aggregates in construction’ by replacing them with recycled material made from crushing inert construction and demolition waste.
With such a large amount of aggregates needed within the construction sector each year, it’s simply not viable to continue using solely primary materials to meet that need. The cost of producing concrete from recycled aggregates is often lower than sourcing primary aggregates, a saving which can be passed on to the customer. Reducing the amount of material which must be disposed of by reusing it within the industry is also clearly of benefit. This is why many manufacturers have already begun using recycled materials where appropriate.
Unknown or hazardous materials
There are manufacturers who are using genuine recycled materials which have reached the end of their useful life in their current format – where the make-up of those aggregates is known and where they are tested to determine their strength and used only in places where it is appropriate -but not all are.
Problems arise when the recycled aggregates are comprised of unknown, or potentially harmful, materials. While it is absolutely right that the concrete industry looks at how it can lessen its environmental impact – and keep manufacturing costs down to keep the market competitive – regulations must be in place, and strenuously enforced, to ensure that aggregates of unclear quality or origin and aggregates containing hazardous waste are excluded from use in structural concrete.
Their use within the construction sector, and specifically within interlocking concrete blocks, is not to be encouraged due to the potential for the structural integrity of such blocks to be compromised if any material contained within them does not meet the regulations surrounding concrete and aggregate strength and durability.
Due to their very nature, the origins of recycled aggregates are difficult, if not impossible, to pinpoint. They can consist of a mixture of brick rubble, glass, plastics and other materials, which impacts their ability to consistently meet the requirements of the British Standards focused on aggregates.
While structural concrete manufacturers have tended to shy away from the use of recycled aggregates, some interlocking concrete blocks are now being made in this way – which can drive down costs if manufacturers are reusing waste they already have on site.
While for the customer, the use of recycled aggregates could represent a cost-saving which is understandably tempting, unless they are aware of the reasons why recycled materials are not suitable in such blocks – and therefore able to question their manufacturer of choice – it could result in them using substandard quality materials unwittingly. Ultimately, while there may be savings to be had initially, the shorter lifespan of many of these substandard blocks could mean being forced to purchase replacements which would be costly in the long-term. Blocks which only contain aggregates being used for the first time are often given a durability lifespan in excess of 100 years – but it is simply not possible to guarantee the longevity of a block which contains unknown elements.
In the worst cases, interlocking blocks including materials of dubious origins have crumbled on or shortly after delivery to the customer’s site, rendering them totally unusable and in need of immediate replacement. This is not only a cost and customer service concern: it also presents a clear safety issue and presents a substantial risk to the company’s reputation. However, these problems could be avoided if specific regulations were put in place specifically surrounding the use of recycled aggregates within structural concrete including interlocking blocks.
“The relative proportions of the three main constituents within recycled aggregates (unbound stone, crushed concrete and crushed brick) can vary widely and it is generally assumed that, as a result, the performance of concrete containing recycled aggregates can vary significantly.”
The quoted research concludes it has been possible in many cases to use recycled aggregates which don’t meet the general concrete-standard regulations. Furthermore, the use of recycled crushed concrete and crushed brick led to ‘lower concrete performance than equivalent concrete mixes prepared with natural aggregates at the same water/cement ratio’.
Regulations – BS EN 12620
The use of aggregates within concrete is covered by the BS EN 12620:2013 regulations which govern elements including physical, geometrical and chemical requirements, as well as durability7. These European guidelines, adopted and published in the UK by the British Standards Institute, specify details such as the minimum oven dried particle density, particle shape, angularity, resistance to wear and fragmentation and classification of the constituents of coarse aggregates.
These guidelines should be followed by all manufacturers producing concrete for use in roads, pavements and precast concrete products. While they are not legally enforceable, British Standard regulations ‘often become intrinsic to the working practices of different industries. Often this is because compliance with a standard is required within contractual terms, or because meeting the standard is essential to providing customer reassurance about quality and credibility.’ Thus, many manufacturers choose to meet the standards and comply with best practice, although there are a proportion who are less conscientious and choose not to.
The standards do not necessarily exclude the use of recycled aggregates within structural blocks, as there is no distinction made between natural, manufactured and recycled material (or a mixture), but all products including those using recycled material should comply with testing standards to ensure they are strong and durable enough for use within construction.
British standards
BS 8500:
The Europe-wide 12620 regulations are supplemented by the British BS 8500 standards which are split into two parts, the first of which looks at the specifications of concrete including exposure classes for durability and intended working life. The second part covers basic requirements relating to delivery, conformity testing, production control and transport for concrete producers.
BES 6001:
Since 2008, manufacturers have been able to aim for the Building Research Establishment’s responsible sourcing benchmark (BES 6001) – it’s now estimated 92 per cent of concrete is certified, giving companies the opportunity to reassure customers of the quality of their products. The standards look at sourcing and traceability but have no set guidelines about recycled aggregates, other than to state it is important to ensure they conform with all requirements even if the materials have similar properties to primary aggregates, and that an appropriate mix is used.
The guidelines do state there should be no set requirement to use more recycled aggregates due to the possibility materials would have to be transported over longer distances if no local recycled aggregates were available, which would clearly be contrary to any environmental benefits the policy would be intended to produce such as a reduction in carbon footprint.
Hazardous waste
The Environment Agency:
Any waste being sent for recycling or disposal must be classified to ensure its composition is fully disclosed; various other pieces of information must also be included within the required description of the waste – for example the location where the waste was produced, a chemical and physical analysis, and – crucially – whether the material is hazardous9 under the criteria defined by the Environment Agency.
Whenever such materials are transported or sold, they must be done so with a waste transfer note. However, if the waste is being reused to make a new product then the manufacturer can undertake a Court of Appeal OSS end of waste test which would mean the material was no longer defined as waste, because it has been turned into a new product which can be sold on – as would be the case if recycled aggregates were used within interlocking concrete blocks10. This means a waste transfer note would no longer be needed and the new product could be sold or moved without the requirement for the exact composition of the product to be disclosed, even if it contained materials which were previously defined as hazardous when they were classified as waste.
There is a cost benefit to the manufacturer of encapsulating waste materials into new products – rather than paying to have their waste disposed of correctly they are able to sell blocks containing this waste to customers, which means the company is now effectively being paid to dispose of waste. While this is a dangerous and dubious practice, crucially it’s not illegal which is why new enforceable guidelines need to be put in place.
At Elite Precast we only use high quality concrete that does not contain any recycled materials and all our interlocking blocks are Class A1 Fire Resistant. For more information about any of our products or services please call us on 01952 588 885 or email sales@eliteprecast.co.uk.
For more information on The dangers of using recycled aggregates in concrete talk to Elite Precast Concrete Ltd
Enquire Now
List your company on FindTheNeedle.