
Sign In
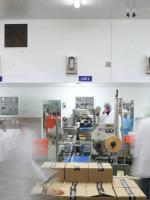
Automation is set to play an increasingly larger role in safeguarding the future of the UK’s food manufacturing industry, according to end-of-line machinery specialist, Endoline Automation.
While most UK food manufacturers understood the efficiencies gained from automation, adoption was at a far slower pace than other countries. However, Covid-19 has emphasised the need to update manual manufacturing practices that will prevent many from recovering quickly once social distancing measures are lifted.
According to a recent post by the International Federation of Robots (IFR) in comparison to several countries across the world, the UK was the only country, over a 10-year period, to report a 9% decrease in productivity per person.
While coronavirus undoubtedly put a strain on global productivity, UK manufacturers faced significant issues because of workers being unable to work in production lines where they normally stand less than 50 cm apart on 12-hour shifts.
There is an established link between automation and increased productivity, so now is the time for UK manufacturers to look at long term growth and invest in automation to support labour intensive activities.
So, why have UK food manufacturers always been so reluctant to take the automation plunge?
Here, Andrew Yates, Sales Director for Endoline Automation, discusses the reasons why the UK lagged behind its global counterparts, how automated end-of-line packaging systems today meets manufacturer demands, and how machinery can be integrated into processing and packing lines quickly to ramp up output.
Demonstrating flexibility
For some food manufacturers, a wariness to change well established manual processes, and an aversion to the risks that new technologies can bring, have created major roadblocks, preventing them from reaping the many benefits automated systems can yield.
Within food manufacturing, the variability of materials has played a major factor, particularly as many believe that uniformity plays a vital role in ensuring automation runs efficiently. To meet retail demand, manufacturers are producing an abundance of brand varieties in all shapes and sizes which can cause greater complexities, due to the variation in size, shape, quality, and weight of the product.
“Retailers are constantly vying for consumer attention, creating greater choices which are continually changing. Historically, this hasn’t always lent itself well to automation and manufacturers need assurances that the investment they make in end-of-line packaging automation is future-proof.”
Fully automated end-of-line systems today can manage an unprecedented range of case styles and sizes and have been re-engineered to handle a wide variety of case materials to suit retail specifications, from poorly scored, lightweight cases, to heavy, twin wall cases. Random systems, with integrated bar code reading technology can seal random sized cases at high speed – and be reconfigured remotely to manage new sizes and orientations as and when required.
Health & Safety
Getting health and safety right has never been more paramount. Food manufactures need to adhere to stringent measures and are being set greater guidance on the use of machinery through the Food Standard Agency’s regulatory model, facing stiffer sentences if they are non-compliant.
Tougher governance around health and safety shouldn’t be a deterrent to automation, however it is vital that manufacturers do not take a CE certified machine at face value.
“There are a number of other factors which need to be considered. Manufacturers need to understand the area the machine will be located in and assess the environment for any safety concerns such as access.”
End-of-line equipment in particular presented significant hazards. Not only do they operate automatically and, in some cases, at very high speed, but the openings, to allow the cases to be transported through the system, are often large enough to be a potential for unauthorised access.
Over the years quality, end-of-line systems have been ergonomically designed offering safer operator access and the integration of Safety Light curtains not only safeguards the machine, but eliminates the need for additional safety guarding so reducing the overall footprint. Systems can also be constructed from IP65 washdown rated stainless steel.
Eliminating unnecessary downtime
Food manufacturing sites that are highly automated operate with fewer workers, resulting in a larger opportunity for uninterrupted processing. Manufacturers are currently seeking to mitigate the risk of sending people home in virus-susceptible areas within their facilities, and automation is a big part of this solution.
The risk of downtime, as a result of machinery failure, servicing or reprogramming has always been a bottleneck in the adoption of automation.
However, automation specialists have been driving the intelligence of end-of-line systems forward for some time, and there is now a greater emphasis on linking these systems together and integrating them into a customers’ own specific data network. Consequently, food manufacturers can capture, process, and analyse big data from the factory floor remotely, and improve productivity, avoid downtime through predictive maintenance, upload new case recipes, and optimise energy use.
“Our systems built today feature an integrated, Industry 4.0 compatible HMI interface enabling engineers to easily re-programme the machine to allow for new configurations of case sizes remotely via a computer, tablet or even a mobile.”
In addition, these SMART systems can be also used to monitor the machinery and send alerts on any preventive maintenance issues and spares shortages. “End-of-line systems are very self-sufficient.”
Beyond Covid-19
Automation has always been an enabler to streamline and enhance efficiency and, as a result of the pressure created by the crisis on manual process, manufacturers should now be able to clearly identify which areas would benefit from automation.
Covid-19 has undoubtedly heightened the need for the UK to integrate automation into their packing lines. By taking the steps to automate, manufacturers will be prepared for any future crisis or shutdown, while ensuring that their output levels and efficiencies remain high.
This will also make the UK more competitive on the global production field.
For more information on Packaging automation set to aid food manufacture growth in the wake of Covid-19 talk to Endoline Machinery Ltd
Enquire Now
List your company on FindTheNeedle.