
Sign In
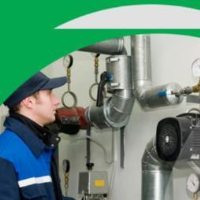
What makes EMS different?All building or facilities managers want to control their electrical, plumbing and maintenance costs! Yet at the same time they need to prevent building or facility dilapidation, comply with regulations and ensure that Health and Safety issues are paramount for occupants, employees, services personnel and visitors. A quandary Yes, impossible to solve NO!From time to time funding will be restricted or budget reduced, particularly when there is an economic recession or the organisation is short of funds. Under these circumstances the manager is reacting to breakdowns or very serious dilapidation. In the short term there are few risks but this can change rapidly. Look at what has happened within the rail industry and the billions of pounds it will cost to correct the situation. Over a 5 to 10-year period you can expect to pay a substantial premium via shutdowns, increased dilapidation, reduced capital value and potential legal actionThe perceived method of tackling these issues are via planned maintenance, effectively taking a conservative view of the facility and what needs to be done and when. The results tend to be unnecessary expenditure, undertaking additional work such as replacing equipment earlier than necessary. By tacking a more predictive approach the objectives change so that equipment is only updated when necessary or when likely to fail or its performance starts to deteriorate. The results are longer equipment life; only replace them when it is necessary to do so. The chart illustrates the impact of the above: within the first year we would expect to achieve a 3% to 5% saving over budgeted levels. By year three this would be expected to increase to approximately 10%, after inflation has been taken into account. There after cost would increase by under the level of inflation.
For more information on Facilities Engineering talk to Environmental Maintenance Services Ltd
Enquire Now
List your company on FindTheNeedle.