
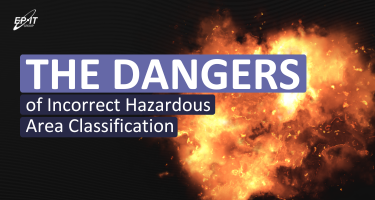
In industries where explosive atmospheres may occur, accurately classifying hazardous areas is vital for ensuring safety and compliance. Hazardous areas are locations where flammable gases, vapours, dust, or fibres may be present, creating a potential for fire or explosion. Misclassifying these areas can have catastrophic consequences, leading to severe accidents and substantial losses. Here are some examples of what can go wrong if hazardous areas are not correctly classified:
Explosions
Chemical plants: improper classification can lead to incorrect equipment being installed in areas with flammable gases or vapours. This increases the risk of sparks or heat sources igniting these substances, causing catastrophic explosions.
Fuel storage facilities: incorrect classification of areas where fuel vapours are present could result in the wrong equipment being installed, leading to the ignition of these vapours and subsequent explosions.
Fires
Food processing plants: misclassified dust hazardous areas can result in the ignition of combustible dusts such as flour or sugar, leading to significant fires.
Textile factories: fibres and dust in textiles can become highly flammable. Without proper classification, unsuitable equipment increases the risk of fire.
Toxic Releases
Chemical plants: incorrect classification can lead to improper handling and storage of toxic chemicals, posing severe health risks and environmental hazards.
Pharmaceutical plants: misclassified hazardous areas handling chemicals can lead to accidental releases, endangering workers and causing contamination.
Equipment Damage
Malfunctions: using inappropriate equipment in hazardous areas can cause failures, such as non-intrinsically safe devices short-circuiting in explosive gas environments.
Corrosion and degradation: equipment not designed for hazardous conditions may corrode or degrade faster, leading to leaks and breakdowns.
Personal Injury
Worker injuries: incorrectly classified areas increase the risk of exposure to explosions, fires, toxic releases, and electrocution, leading to severe injuries or fatalities.
Environmental Damage
Pollution: incorrect classification can lead to mishandling hazardous materials, causing spills and contaminating soil and water sources.
Wildfires: misclassified areas with combustible dust, such as agricultural or wood processing facilities, can lead to wildfires if dust clouds ignite.
Real-World Accidents and Consequences
Incorrect hazardous area classification can lead to several serious accidents, primarily fires and explosions. Here are some examples of accidents that can occur:
Ignition of flammable vapours: if an area with flammable vapours is incorrectly classified as non-hazardous or a lower hazard zone, unsuitable equipment may be used. This can lead to sparks or heat that ignite the vapours, causing a fire or explosion.
Explosion in confined spaces: misclassifying an area where flammable gases can accumulate (like inside process equipment) may result in using equipment that can generate sparks, leading to an explosion.
Dust explosions: incorrectly assessing areas with combustible dusts can lead to the use of equipment that may ignite dust clouds, causing devastating explosions.
Catastrophic releases: underestimating the risk of major releases (like vessel or line ruptures) can lead to inadequate safety measures and potentially catastrophic consequences.
Fires from secondary releases: failing to account for potential secondary releases (e.g., spills from dropped containers) can result in fires if ignition sources are present in areas incorrectly deemed safe.
Explosions during maintenance: if areas are not properly classified, maintenance work involving hot work or unsuitable tools and equipment could ignite flammable atmospheres.
Laboratory fires or explosions: in laboratory settings, incorrect classification may lead to using standard equipment near volatile solvents or during distillation processes, potentially causing fires or explosions.
These specific examples as reported in HazardEx, Health and Safety Executive, and other industry publications demonstrate that incorrect hazardous area classification can lead to serious accidents, including chemical releases, explosions, fires, and electrical incidents, resulting in injuries, fatalities, and significant damage to facilities. Proper classification and implementation of appropriate safety measures are crucial to prevent such incidents in industries dealing with hazardous materials or potentially explosive atmospheres.
Chemical releases and injuries: at the Honeywell International Fluorine Products facility in Geismar, Louisiana, a release of highly toxic hydrofluoric acid (HF) occurred, seriously injuring a worker. This incident highlights the dangers of improper handling or containment of hazardous chemicals in incorrectly classified areas.
Burns and fatalities: at a Tata Chemicals Europe Limited plant in Northwich, Cheshire, a worker died from complications after his foot slipped into a trough containing liquid calcium hydroxide, causing chemical and thermal burns. This incident demonstrates the risks of inadequate safety measures in areas with hazardous chemicals.
Explosions: an explosion at a liquid nitriding facility in Chattanooga, Tennessee resulted in one fatality. This incident underscores the importance of proper classification and safety measures in areas with potentially explosive atmospheres.
Electrical arc blasts: at a Stanley Black + Decker facility in Willard, Ohio, a maintenance electrician suffered severe burns during an electrical arc blast. This incident illustrates the dangers of using inappropriate electrical equipment in potentially hazardous areas.
Fires and explosions on vessels: an explosion on a bulk carrier off the coast of Morocco killed seven people. While not directly related to land-based facilities, this incident highlights the importance of proper hazardous area classification in maritime settings as well.
Preventive Measures
To prevent such accidents, it's crucial to conduct thorough and accurate hazardous area classifications, implement appropriate safety measures, and regularly review and update these classifications as part of an overall risk assessment process. Here are some key steps:
Conduct thorough assessments: ensure all areas are properly evaluated for potential hazards.
Use suitable equipment: install equipment that meets the necessary safety standards for classified hazardous areas.
Regularly update classifications: reassess hazardous area classifications periodically and whenever there are changes in processes or materials.
Train personnel: educate workers on the risks associated with hazardous areas and the importance of proper equipment and procedures.
Implement safety measures: establish robust safety protocols and emergency response plans tailored to the specific risks of each classified area.
Correct hazardous area classification is essential to ensure worker safety, equipment integrity, and environmental protection. Speak with experts at EPIT Group if you need help achieving the highest standards of safety and compliance in your hazardous environments
For more information on The Dangers of Incorrect Hazardous Area Classification talk to EPIT Group