
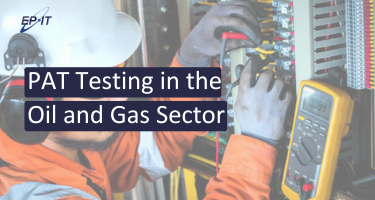
In the oil and gas industry, safety and compliance are more than priorities—they are integral to operations. The environments are inherently high-risk, with flammable materials, heavy machinery, and complex systems creating conditions where even minor electrical faults can lead to catastrophic consequences. Portable Appliance Testing (PAT) plays a vital role in mitigating these risks, ensuring the safety of personnel, protecting valuable assets, and maintaining operational efficiency.
PAT testing is not merely a regulatory obligation; it is an essential practice that fosters a culture of vigilance and responsibility among employees. By embedding PAT testing into everyday operations, organisations signal their commitment to safety, encouraging staff to be more aware of the risks associated with electrical equipment. When employees see regular inspections being carried out, they are more likely to report potential hazards, handle equipment responsibly, and recognise their role in maintaining a safe workplace. This proactive approach helps prevent accidents and promotes a culture where safety becomes second nature.
The legal implications of neglecting PAT testing can be severe. Under the Electricity at Work Regulations 1989, employers are required to ensure that electrical systems and equipment are maintained in a condition that prevents danger. Failure to comply can result in substantial fines, reputational damage, or even prosecution in the event of a serious incident. Moreover, many insurers require evidence of regular PAT testing as part of their policies for high-risk industries. Without this documentation, businesses risk invalidating their insurance, leaving them exposed to significant financial liabilities in the event of an accident.
The operational impact of neglecting PAT testing can be equally damaging. In high-pressure industries like oil and gas, downtime caused by equipment failure is not just inconvenient; it’s costly. Unplanned outages can delay projects, disrupt supply chains, and erode client trust. PAT testing helps to identify potential issues before they lead to breakdowns, ensuring that equipment operates reliably and efficiently. By addressing faults early, organisations can avoid expensive repairs and replacements, while extending the lifespan of their high-value assets.
In addition to operational benefits, regular PAT testing supports long-term sustainability goals. Repairing faulty equipment identified through testing reduces waste and maximises the use of existing resources. In a sector increasingly focused on sustainable practices, this aligns with broader efforts to minimise environmental impact while maintaining stringent safety standards.
For organisations committed to best practices, training plays a critical role in the effective implementation of PAT testing. EPIT’s City & Guilds In-Service Inspection and Testing of Electrical Equipment Course equips individuals with the skills needed to manage and conduct thorough inspections of portable electrical appliances. Delegates not only gain theoretical knowledge but also hands-on experience, ensuring they are confident in identifying and addressing potential hazards. The course includes a copy of the IET Code of Practice, a key resource for maintaining compliance, and offers pathways to advanced qualifications in electrical safety.
By prioritising PAT testing, businesses in the oil and gas sector can protect their teams, meet legal requirements, and ensure the reliability of their operations. More than that, they can foster a safety-first mindset, building an environment where risks are managed effectively, and employees are empowered to take responsibility for their role in maintaining a safe workplace.
Investing in PAT testing is not just a regulatory necessity; it’s a strategic choice that safeguards your business and your people. To find out how EPIT’s course can help you enhance your safety protocols, and explore the 2025 course dates.
For more information on The Importance of PAT Testing in the Oil and Gas Sector talk to EPIT Group