
Sign In
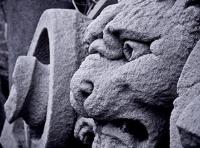
Original equipment manufacturers (OEMs) have been outsourcing their electronics manufacturing and test for decades. So it’s perhaps surprising that a number of myths relating to outsourcing still remain today.
Of course, there is no smoke without fire. I’m sure some of these are the result of bad experiences, which have then been shared time and time again. That's why I thought I would try and tackle some of these head on so that anyone considering outsourcing to an electronics manufacturing services (EMS) provider can base their decision on facts and not fiction.
Here are five common myths relating to outsourcing and my advice to anyone grappling with these or similar questions.
2026: The future of electronics manufacturing services
No one can accurately predict the future.
However, it’s fair to say that some of the technological advancements we are starting to see will transform how electronics manufacturing services (EMS) providers operate. The race is on for both original equipment manufacturers (OEMs) and EMS providers to digest what "big data" really means to them, while trying to increase automation, prepare for Industrie 4.0 and somehow make their factories "smart".
So how far will EMS providers go? Well, with such a broad range of capabilities and a diverse customer base, the answer really should be "far and wide". Unsurprisingly, many are holding back and watching with interest while the Tier 1s make a head start. After all, many of these advancements require significant planning and investment - not something to dive straight into.
While a lot can happen in 10 years, here are my predictions regarding the four major areas that I believe will impact EMS providers supplying industrial products and how they might adapt to them.
The rise of 3D inspection technology within electronics manufacturing
This month we caught up with David Bennett, President of MIRTEC Europe.
Founded back in 2000, with facilities in the US, Europe, China, Japan and Korea, MIRTEC is a global supplier of automated inspection equipment to the electronics manufacturing industry.
In this blog post, David discusses how the market is rapidly shifting from 2D to 3D automated optical inspection (AOI) systems and the benefits this technology has to offer customers. David also provides insight into the latest product developments being worked on at MIRTEC and his own predictions on what we might expect to see in the future.
What is stress screening and how do electronics manufacturers use it?
In a previous post, we discussed soak testing, a form of performance testing that is used in electronics manufacturing to find out how a product "survives" in the wild.
But what happens when the going gets really tough – how can you be sure that a product will be able to withstand more extreme scenarios? That’s where stress screening comes into play.
Unlike soak testing, which places a product under "normal" conditions, stress screening, also known as fatigue testing, imposes more punishing conditions that are designed to test a product to its limits - or beyond. For example, a product might be subject to vibration tests, thermal shock or mechanical shock.
Screen testing proves a product’s reliability, durability and safety by identifying the points at which failure will occur; the weak spots. So how is this process implemented by electronics manufacturers?
Outsourcing your manufacturing? Don't overlook outbound logistics
When it comes to outsourcing their manufacturing operation, most original equipment manufacturers (OEMs) primarily focus on the assembly processes.
During their evaluation, they will thoroughly investigate how well equipped their potential electronics manufacturing services (EMS) provider is to manufacture their product to the highest quality - and to the end customers' expectations.
Also in the spotlight will be the quality of the EMS company’s sourcing and supply chain capabilities, together with the strength of their key supplier relationships. In addition, their equipment, processes and quality procedures all need to be fully investigated.
By contrast, the shipping part of the equation will often be lower down the list of priorities. After all, the selected EMS partner just needs to be capable of getting finished products from A to B, right? But outbound logistics could play a far more integral role in the success of an outsourcing venture. This blog pot should help to illustrate this and hopefully explain how this last piece of the outsourcing jigsaw can have a major impact.
When it comes to outsourcing their manufacturing operation, most original equipment manufacturers (OEMs) primarily focus on the assembly processes.
During their evaluation, they will thoroughly investigate how well equipped their potential electronics manufacturing services (EMS) provider is to manufacture their product to the highest quality - and to the end customers' expectations.
Also in the spotlight will be the quality of the EMS company’s sourcing and supply chain capabilities, together with the strength of their key supplier relationships. In addition, their equipment, processes and quality procedures all need to be fully investigated.
By contrast, the shipping part of the equation will often be lower down the list of priorities. After all, the selected EMS partner just needs to be capable of getting finished products from A to B, right? But outbound logistics could play a far more integral role in the success of an outsourcing venture. This blog pot should help to illustrate this and hopefully explain how this last piece of the outsourcing jigsaw can have a major impact.
Improving efficiency and safety through automated test solutions
This month we caught up with John Blandy, Sales Manager of TestWorks Group Ltd.
TestWorks is an innovative technology company offering a comprehensive range of solutions, products and services in the field of electronic and mechanical design, manufacturing and test.
In this blog post, John discusses how the company is reacting to growing customer demand for custom electronics/PCB test solutions, which offer increased coverage at a reduced price. John also explains how they are developing automated test solutions to help keep operators and products safe when performing hipot/electrical safety testing.
How has the last twelve months been for you and how do you see the future?
Although some less significant parts of our business, such as in-circuit applications, continued a downward trend, our core custom test solutions business finished on target, which was a growth on the previous year of around 20 per cent, made up of new and repeat business.
Conditions are still tough but we see a good demand for custom functional test solutions. Although some larger organisations are retaining and/or growing their test development in-house, the general trend is still to outsource this activity.
For more information on 5 myths about electronics manufacturing outsourcing talk to ESCATEC Mechatronics Ltd
Enquire Now
More Blogs
List your company on FindTheNeedle.