
Sign In
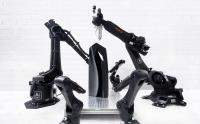
UK-based 3D printing solutions provider EVO 3D has launched a new range of robotic pellet 3D printer packages to deliver improved benefits to its customers.
The firm is working with industrial robot manufacturer KUKA, AI and robotic 3D printing developer Ai Build, and Canada-based OEM Dyze Design, to offer four packages that feature various robot, extruder, and software combinations for pellet additive manufacturing.
EVO 3D’s AM service offering
Exeter-based EVO 3D provides a range of 3D printing solutions, including the resale of 3D printers and accessories and technical support. The company’s customers include the likes of the National Manufacturing Institute of Scotland, University of Cambridge, and London Electric Vehicle Company which have leveraged its services for a variety of applications within the industry, research and other sectors.
EVO 3D announced its launch at the beginning of this year alongside a £250,000 capital investment to expand its operations. Shortly afterward, the firm revealed it had joined Evolution Sales and Marketing to strengthen its offering to the additive manufacturing sector.
Leveraging the benefits of pellet 3D printing
Pellet-based extrusion provides a number of advantages, including enabling very high throughput, reducing material costs and offering access to new kinds of polymers that do not exist in filament format. Pellets can also cost between 65-90 percent less than filament of the same plastic, depending on the volume of purchase.
These benefits are offered through EVO 3D’s new robotic pellet printer range, which will see customers achieve faster print speeds and larger print sizes. Due to the large heat zones in pellet extruders, a material throughput of almost 100 times greater than that of FDM 3D printers can be achieved, making such extruders capable of print speeds of up to 200 times quicker.
The combination of robotic arm 3D printers and pellet-fed extruders is typically used for large-scale prints, such as 3D printed furniture and makes the fabrication of these objects more economically feasible due to the cheaper material costs and faster print times.
Additionally, customers can create their own custom composites and material blends through the combination of different pellets. By easily adding various dyes, additives, and reinforcement fibers to a mix, customers can create custom composite plastics, of which waste can be reused by tossing it in with virgin pellets.
As such, not only does pellet 3D printing offer efficiency and cost benefits, but the technology also delivers environmental advantages. Currently, initiatives such as Print Your City are helping cities to collect plastic waste to 3D print public park benches, while the likes of polymer 3D printing specialist Covestro sell recycled plastic shreds for pellet 3D printing. Going forward, EVO 3D envisions a future where everyone can chop up their own household plastic waste to use as pellets in their own 3D printers.
Enabling large-scale industrial applications
To launch its new pellet 3D printing range, EVO 3D has teamed up with KUKA, Ai Build, and Dyze Design to offer four different packages to its customers. Each package is comprised of a KUKA robot, a pellet extruder from Dyze Design, and Ai Build’s Ai Sync software.
Dyze Design’s high flow rate Pulsar Pellet Extruder can put out 2.5kg per hour of material, enabling the printing of bigger pieces in less time. The extruder features three heating zones to ensure the polymer is at a constant temperature all the way through the end of the extrusion, while a patented anti-oozing system prevents leaks during movement. The Pulsar Pellet Extruder can print any materials currently manufactured on the market including PEEK, Ultem, and PSU.
“Pellet-based extrusion is a true game changer in the 3D printing industry,” said Simon Duchaine, Chief Marketing Officer of Dyze Design. “It enables really high throughput, but most importantly, it reduces your material costs by up to 10 times and gives you access to new kinds of polymers, some that don’t even exist in filament format.”
Ai Sync, meanwhile, is Ai Build’s enterprise software for large-scale, autonomous additive manufacturing. Leveraging advanced algorithms, IoT devices and a cloud infrastructure to automate workflows, the software is designed to make 3D printing easy, smart, and affordable.
The software’s advanced toolpath capabilities allow users to print complex geometries without supports, therefore reducing material waste, printing times, and failed builds by 65 percent. Using the toolpaths, users can design and print the parts they want without constraints or limitations.
Ai Sync also helps users to reduce their dependency on supply chains and offers a greater choice of materials ranging from polymers, metals, and other high-performance materials. With Ai Sync, customers can make use of one additive manufacturing platform to scale, control and monitor the entire 3D printing process.
“We are excited to collaborate with EVO3D and Kuka robotics to provide the software solution for the large format additive manufacturing packages,” Ai Build said. “Our data-driven software makes advanced toolpath generation for complex, multi axis geometries simple and automated. Teaming AiSync with Kuka hardware means we can provide a highly reliable solution for a range of industries and applications.”
The Ai Sync interface. Image via Ai Build.
Finally, the flexibility and versatility of KUKA’s industrial robot make it the ideal component for the execution of automated additive manufacturing methods, owing to its repeatability and accuracy. With a combination of automation tools, extruders and application-specific software increasingly enabling the delivery of more materials within industrial additive manufacturing, from polymers and metals to concrete, demand for ad-hoc, atypical items and a faster, stronger, cheaper approach to manufacturing is continuing, according to KUKA.
The company continued: “It is an exciting time for modern manufacturing, as very small to very large components and parts can be produced in alignment with an ‘on-demand’ economy, with benefits such as reduced cost of prototyping and thus reduced cost of entry being achieved by manufacturers, versus traditional, subtractive methods. Product integrity, larger assemblies consolidation and multiple material combinations can be satisfied, broadening the scope of manufacture.
EVO 3D’s robotic pellet printer range
The first package, called the Small but Mighty, is made up of a Dyze Design Pulsar Pellet Extruder, featuring an extrusion rate of 2kg per hour, and a KUKA LBR iiwa robot with an 820mm reach. The second, The Long Arm, also contains the Pulsar Pellet Extruder but offers a KUKA KR CYBERTECH robot with a 2,013mm reach.
The third package, named The Long Arm Heavy, features an extruder with a 12kg per hour extrusion rate and a KUKA KR IONTEC robot with a 2,500mm reach. Meanwhile, The Long Arm Super Heavy package offers a Extruder with an 84kg per hour extrusion rate and a KUKA KR QUANTEC robot with a 3,904mm reach.
The new robotic pellet printer packages are delivered hand-in-hand with EVO 3D’s service offering, which includes onsite consultation and installation. EVO 3D will also provide full training and ongoing support for the package deals to its customers in a one-stop-shop format, alongside competitive pricing which will be announced through the firm’s website.
For more information on EVO 3D LAUNCHES NEW ROBOTIC PELLET PRINTER PACKAGE RANGE talk to Evo3D
Enquire Now
More Case Studies / Blogs
List your company on FindTheNeedle.