
Sign In
Taking 3D Printing to the Moon and Beyond
28-05-2021
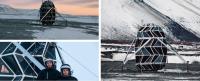
Since the historic 1969 moon landing, experts have looked at ways to prolong and improve on moon explorations, with the next one tentatively planned for 2024. The concept of humans living on the moon continues to intrigue those bold enough to find new solutions for us to reach – and live among – the stars.
It’s this vision that brought together two Danish architects, Sebastian Aristotelis and Karl- Johan Sørensenth of SAGA Space Architects. Both have a fascination with space exploration and technology, and it is this love that allowed them to collaborate on an ambitious project that would change the way scientists look at lunar habitation.
Their innovative idea was to create a solar-powered living habitat to help non-astronauts survive the harsh conditions of the moon, and further allow them to thrive by adding an element of ‘cosiness’ (a Danish word known as hygge) to the internal living space.
Karl-Johan Sørensenth and Sebastian Aristotelis
With this in mind, what made this project truly unique was that the habitat would have a liveable function to help counteract monotony, claustrophobia and psychological stress which is commonly reported from astronauts. In fact, previous research has shown that lack of stimuli, isolation, and confinement will become major challenges for the long-term voyages of the future.
As the pair put it: “If we are trying to settle on other planets, we must be very careful how we design the homes. In space, your habitat is your entire world; there is no nature or change of scenery.”
To help test this concept, the pair would work with scientists, engineers and even polar experts to build a test habitat for a planned three-month simulated Moon mission within the Arctic, Northern Greenland, which is ideal to replicate similar cold conditions.
But how to create an adaptable space that can easily be reworked yet still be durable enough to withstand the extreme weather elements? For this, the team leaned on the concept of origami. For the design phase, they developed a unique origami structure that would make up the outer shell of the habitat and allow for easy compartmentalization during transportation and when being setup. They tested compliant 3D printed joints that would work best with the expandable habitat concept. While origami is easy with paper, a thicker, rigid material that can be foldable is something else entirely.
Within the unfolding pod concept, there is limited space and they had to make sure to add space for batteries, water and a living algae farm. There was no way for them to add more supplies without compromising the personal space of the astronauts. The question became: How can they maintain spare parts and repairs if anything were to go wrong? This was when, as a long time 3D printing enthusiast, Karl-Johan knew that this would play an important role in their success.
The structure of the habitat explained
Due to the extreme nature of the mission, the team had thorough requirements for the 3D printer they would end up selecting. They required a 3D printer that needed to be reliable for multiple outputs, compact to fit within the limited space, and versatile in the materials it can print with, all while performing quietly.
After a series of high-production performance tests with a number of large printer companies from around the world, they ultimately selected the award-winning Craftbot 3D printer as the best option for their mission. The Craftbot system outperformed all of the other printers due to their incredibly high print quality, speed, reliability, and repeatability. Furthermore, it helped that Craftbot 3D printers were production-ready right out of the box.
Often referred to as pioneers and industry leaders themselves, Craftbot was thrilled and honored to help with this unique project. Immediately, Craftbot shipped eight Craftbot Plus and three Craftbot3 printers to support with printing the habitat model parts for use in the planned 3-month field test.
Craftbot printers in use during the preparation for the mission
With the final design in place and a group of Craftbot printers, they constructed a static mock-up of the habitat out of MDF and 3D printed ABS joints for the field test. In total, they printed a total of 113 joint parts using the Craftbot printers, all of which were perfect. After a year from conception, the design was completed for what became known as The LUNARK. The prototype included a series of in-built digital software systems, including a weather simulator and an algae reactor, to nurture and monitor inhabitant’s nutri tion source.
The design and the 3D printed prototype of the foldable habitat
Printed with PLA and flexible filaments on the dual-headed Craftbot 3 printer
By Fall 2020, Aristotelis and Sorensen were ready to embark on the planned three-month trial to test their prototype. Isolated in one of the harshest climates, they endured -30°C temperatures, hurricane winds, and even hungry polar bears to successfully complete the test.
The habitat in Greenland during the mission
During the mission, the Craftbot 3D printer within the habitat was essential in printing spare parts, tools and even bendable wall pieces needed for the maintenance of the habitat.
The interior of the habitat with the Craftbot 3D printer in it during the mission
Having completed their most ambitious project, the unique LUNARK story and success of the mission has led to multiple award wins, global media coverage, planned documentary movies, and even plans for a future exhibition of the habitat.
During this age of 3D innovation and collaboration, Craftbot believes in the importance of supporting future scientists as they develop new ways to tackle issues and excel space travel to a new dimension.
For more information on Taking 3D Printing to the Moon and Beyond talk to Evo3D
Enquire Now
More Case Studies / Blogs
List your company on FindTheNeedle.