
Sign In
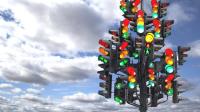
Boost throughput, go green and embrace the future. These are words to live by within the automotive industry. These words are also highly relevant when it comes to production. A smart production means high efficiency, energy savings as well as new technology that prolongs service intervals. This blog article will give you insight into how smart production can benefit the automotive industry.
A production that handles heavy loads without compromising on speed
A smart production in the automotive industry means a lot of things and includes a number of different production line solutions. What is important in the automotive industry is that the production line can handle heavy loads without compromising on speed and efficiency. The industry earns a quite small amount of money per car, which means they need to produce many cars in order to be profitable. There are high delivery requirements with tight margins, so for the industry to deliver what they promised they need well-functioning production flow solutions that operate without production stops.
Reduced operational costs and better utilization of the factory floor
Achieving a smart production in the automotive industry has many benefits for the production owner. By eliminating bottlenecks, you create a balanced production flow that leads to increased sellable throughput, improved quality assurance as well as increased yield and product safety. Also, it reduces changeover time, which increases line flexibility and available production capacity. A smart production can also contribute to reduced operational costs. It minimizes non-value adding operations and lowers the power consumption per produced unit. In addition, it reduces work-in-progress (WIP) and helps to better utilize the factory floor.
Energy efficient solutions that apply predictive maintenance
As mentioned above, there are several ways to achieve a smart production. Depending on industry, production, and prerequisites, there are multiple ways of combining and adapting smart production solutions so they meet your specific needs. Examples of how to achieve a smart production in the automotive industry are:
Space-efficient solutions that lead to more capacity per factory m². This can be achieved by, for example, using module-based production lines or vertical transport solutions.
Energy-efficient solutions. Energy can be saved in multiple ways, where one example is to use a start-stop function on the production line. This means the conveyors stop automatically when the production flow stops. In turn, they start running again as soon as the production flow comes back on.
Connected, electromechanical solutions that reveal how the production equipment is doing by gathering production data. This makes it easier for the manufacturer to anticipate future production events and prolong service intervals.
Production solutions that apply predictive instead of preventive maintenance. Preventive maintenance is scheduled maintenance that is performed regardless of the status of the machine and could thus lead to unnecessary maintenance. Predictive maintenance, on the other hand, is based on the actual condition of the equipment rather than time or age factors. Both preventive and predictive maintenance is achieved by analyzing data from the production and the machines.
Twin track pallet system for smart production
An example of a smart production solution for the automotive industry is FlexLink’s Twin Track pallet system. The conveyor platform for heavy loads offers increased production efficiency and trouble-free operations. It has a smart line architecture based on a simulated, monitored and digitalized system design with unique predictive maintenance. As a bonus, you get a digital twin of the line for future process changes, expansion or introduction of new products. The twin track conveyor for heavy loads is fully digitalized and prepared for the Internet of Things (IoT) and traceability requirements. The standardized modules with pre-defined control logics shorten design and installation time, reducing time-to-market. In addition, all stops, locating stations and transfers are all electrical. This allows for a reduction of 50% of the system’s energy consumption.
Continuous optimization through the systems’ entire lifecycles
FlexLink delivers smart and innovative production solutions for all businesses in the manufacturing industry. As System Architects, FlexLink supports you with line design and continuous optimization through our systems’ entire lifecycles. We start by applying a feasibility study and acquire data from existing lines to create a simulation and iteration analysis. With the results of the study and our extensive experience, we can define the optimal solution for your needs.
I hope you enjoyed reading my article about smart production solutions in the automotive industry. Feel free to contact me with questions or visit our website social media channels or our blog for more information about FlexLink and our offer.
For more information on How to achieve a smart production in the automotive industry talk to FlexLink Systems Ltd
Enquire Now
List your company on FindTheNeedle.