
Sign In
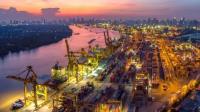
Supply Chain Bottlenecks are delays, interruptions, complications, and unexpected accidents. The list of what causes supply chain bottlenecks is long and ranges from labor shortages and capacity constraints to component shortages. While small, these inefficiencies negatively impact business productivity in terms of quality, production costs, and time. Delayed deliveries, exploding budgets due to higher prices caused by delays, and errors in repetitive manual tasks. So, what is the situation now, and how can automation help eliminate weaknesses and improve operations?
The current situation: a difficult balance between recovery and crisis
Globally, supply chains have endured significant disruption for a while now, and it seems that the problem will not change anytime soon. The post-pandemic recovery has generated a high demand for raw materials, intermediate inputs, and services from supply chains. This has caused a spike in the demand of available supply, leading to rising and volatile prices and delivery delays. Hence, bottlenecks are an essential driver of inflationary pressures worldwide, raising the prices of tradable goods. Most affected by bottlenecks are raw materials, whose prices have significantly increased as shortages emerged, and firms scrambled to secure supplies.
The manufacturing industry has also been badly hit, experiencing a price increase, especially for components such as computer chips and semiconductors. This has caused several instances of downtime. The situation has been made worse by the rise in shipping costs for trade between Asia and North America, which has caused longer delivery times. The current crisis highlights the importance of an efficient response to bottlenecks that may occur in manufacturing workflows.
New technologies for improved processes
Are we in the early signs of a supply chain turnaround? Maybe – at least, we are seeing the first fundamental developments. After some challenging years, we can finally see improvements in shipping and transportation. One of the most effective ways to offset problems caused by supply chain management issues is purpose-built solutions and technologies, such as AI systems. These new technologies can help to improve visibility, allowing manufacturers to detect supply chain bottlenecks, such as shipping time issues. Hence, companies can intervene and address challenges, leading, i.e., to improved shipping times. As companies are entirely focused on supply chain operations, we are about to see an increasing resiliency in supply chains (Source: Forbes).
Environmental consciousness: increased regulations
The global movement towards a carbon neutral, or at least more s responsible approach to our resources, and the environment is not going away anytime soon. Companies are increasingly pressured to make their supply chain transparent and sustainable, especially considering the new CDSR regulations that will come into effect in January 2025. Due to the EU’s CSRD (Corporate Sustainability Directive), large companies will need to disclose their environmental and social challenges starting in January 2025 (Source: Echochain). So, what does this mean for your supply chain? For companies, the value chain has a huge environmental impact that can make up to 80% of a product’s ecological footprint. This is, for example, defined by what kind of materials suppliers use or how they produce goods. With the upcoming new regulations, companies must report environmental data from suppliers they directly conduct business with.
Labor shortages
A recent study by Gartner revealed that 78 percent of manufacturers plan to invest in automation to tackle the impact of labor shortages (Source: Gartner). With many warehouse workers changing jobs, pandemic-related illnesses, and an aging workforce, manufacturers face common challenges, leading to delays and other problems. The answer lies in automation and robotics. Automation promises to help provide the most effective solution to these pressing challenges. The manufacturing processes can be regulated and manipulated through automation to maintain quality. Therefore, automated production flows enhance processes’ efficiency by minimizing non-value-adding operations and bottlenecks. Investing in automated production equipment creates a valuable resource for large production volumes and increases overall productivity. This, in turn, reduces costs and increases profitability.
Working with cobots and industrial robots can automate repetitive and error-prone tasks. Therefore, a high level of automation can prevent problems due to issues with human labor. This helps to produce companies to keep up with shipping demands, reduce costs, increase employee safety and hence, increase efficiency. Automation will, therefore, ultimately help to mitigate supply chain risks and protect your business.
Going Local: a trend towards insourcing of production
Due to the global situation, more and more companies are deciding to align their production locally. This change has both advantages and disadvantages. Local sourcing describes the process of sourcing goods, materials, services, or products from local manufacturers. Global sourcing, on the other hand, is the process of acquiring primary and secondary products from all parts of the world. Large corporations often leverage the benefits of global sourcing, for example, to increase cost-effectiveness, diversify their supply chain and reduce time to market. However, local sourcing is becoming a targeted strategy for more companies. Especially today, a significant proponent of local sourcing is sustainability. By reducing shipping and storage, companies not only decrease costs but also make an essential contribution to reducing carbon emissions.
Furthermore, local sourcing increases flexibility as suppliers are usually more reactive to meet demands. Another important factor is quality control. Ordering from local suppliers has the advantage that the product quality can be controlled much better (Source: producementtactics.com).
Automation as solution
Accelerated by the pandemic, manufacturers of all sizes increasingly turned to automation as an effective way to increase the efficiency of their supply chain. Automating steps of your production can increase the scale of production efficiency, decreasing product and labor costs. Automation can help to increase supply chain management. Furthermore, it improves environmental and regulatory compliance by tracking real-time data, automating processes, streamlining operations, and increasing speed and efficiency. So, how can we fully transform and automate your processes? Reach out for more information.
If you have any questions or want to know more about industrial automation and robotics, don’t hesitate to contact us. Also, visit our website and LinkedIn to learn more about FlexLink.
For more information on How to overcome the supply chain challenges: reasons, consequences, and priorities talk to FlexLink Systems Ltd
Enquire Now
List your company on FindTheNeedle.