
Sign In
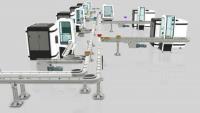
About 20 years ago, optical labs as we know them today were revolutionized. Optical labs started to look at automation of optical job tray handling and advancing machine capabilities. Today, optical labs again must adapt to new market requirements. As eCommerce has become the leading business model for optical companies, speed, efficiency, and information are requested more than ever to increase the efficiency of lab processes.
In the early 2000s, small sections of conveyor systems were added to optical labs to move optical job trays from one process to another. An article in Optometric Management from January 8, 2003, describes the situation very well. The report suggested that if a lab sold three pairs of glasses daily, five days per week, they needed a finishing lab. Images of optical labs from the past didn’t reveal too many conveyors in optical labs.
The benefits and efficiency improvements were enough to expand conveyors and optical job tray handling solutions throughout the entire lab. Over the years, as machines progressed, conveyors became an integral part of the overall lab flow and functionality. Solutions evolved to save space with elevators and spirals, tray stacking and de-stacking were created, software was added to intelligent route trays to the correct process or machine, and, eventually, conveyors were a part of the lab as the equipment processing the lenses. The days of manual carrying stacks of trays or placing stacks on carts were in the past, and the focus with people was on making eyeglasses.
Meet the modern optical lab
Fast forward to today and think about the future. There is still much to consider when planning for optical tray handling and other automation efficiencies. Manufacturers in optical and many other industries face labor shortages and competitive pressure to lower the costs of products. Some optical companies are also changing their delivery models from ship to the store to ship to the end customer. Speed, efficiency, and information are requested more today than ever before. Optical labs want to collect data (OEE – Overall Equipment Efficiency) for their equipment to fine-tune their processes and complete more production. Great strides have been made with robotics and software to help advance labs into the future.
Robotics and software revolutionized optical labs
Robots could be helpful for loading and unloading machines, picking and placing lens blanks and frames, sorting, and buffering job trays, and, in the optical job tray and performing other manual tasks. Is it possible for a robot to complete the assembly process (lens to frames)? Automatically de-boxing lenses are near a viable solution. Automating the storage and retrieval of lens blanks and frames is available, eliminating the manual handling and potential for errors – including contact lenses. The next generation of modular plug-n-play conveyors is available for fast setup, changes, and adding machines. eCommerce solutions are available to sort, consolidate and package orders for shipments.
Technological advancements and the people who think ahead to what would make eyeglass manufacturing better have driven solutions and growth in automation since back then. Machine suppliers advance, automation suppliers advance, and companies advance. All it takes is for lab people to keep asking for more solutions and suppliers to keep innovating to make those required solutions.
Contact us to learn more about optical lab automation. Also, please visit our website and follow us on LinkedIn for more regular updates on industrial automation and robotics. Also, read our other blogs about the optical industry here.
For more information on Increasing the level of automation in optical labs talk to FlexLink Systems Ltd
Enquire Now
List your company on FindTheNeedle.