
Continuous vs Batch Feeding Processes
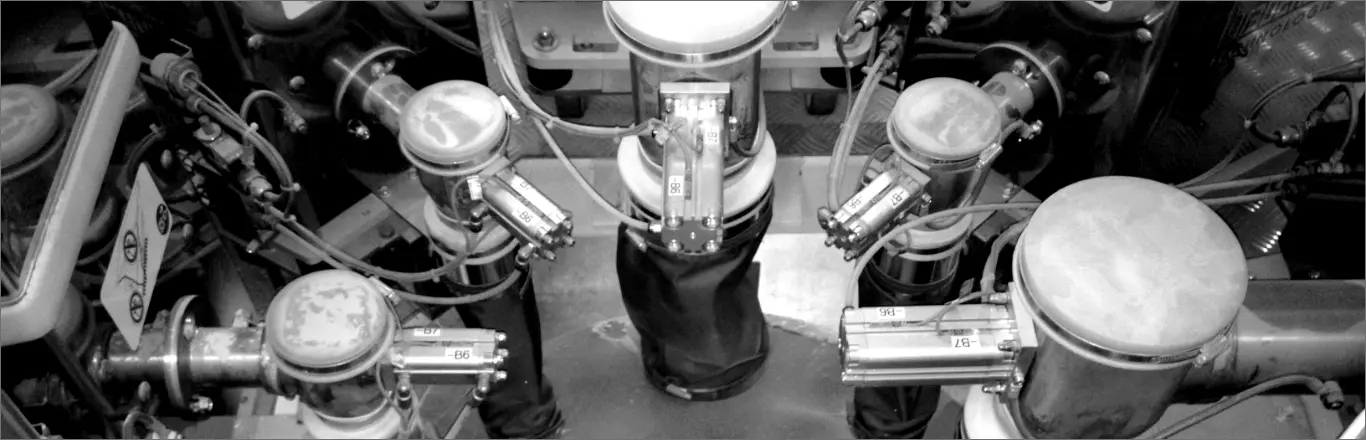
In any production process, customising your feeding and weighing technology to your application is crucial to ensure maximum efficiency. Genesis Process Solutions, with our extensive knowledge of feeding processes, guide customers in selecting the right system for their solids and liquids feeding needs. The decision between continuous and batch feeding processes is based on various factors, meaning you must do thorough research before investing in a new production system.
Why choose a Continuous Process?
Continuous processes are generally more suitable for higher throughputs or mass production with only a few recipe changes. The longer the production process runs, the higher the economic efficiency and the better your ROI. Downtime can be reduced, even with frequent recipe changes, as long as enough weigh-feeders are available to handle the different ingredients. In this case, any weigh-feeders which are not required are excluded from the recipe and the production process can continue.
Continuous processes typically demand a high short-time accuracy and as they need refilling while continuing to run, their control is more complex.
Filling must be precisely controlled as the weight of material fed out at this point in the cycle cannot be checked. Correct hopper venting is another important factor and each weigh-feeder is vented separately to avoid cross contamination of ingredients . For higher throughputs, the weigh-feeders remain relatively small. Weigh-feeders which are not in use, can simply be deselected in the control system, which results in short downtimes with easy ingredient changes and a simplified cleaning process.
High outputs are faster and easier to achieve with a continuous process because the devices are smaller than for larger batches. Since the materials are fed directly into the downstream processing machine, e.g. a mixer, extruder or kneader, and fewer personnel are usually required, this feeding method can provide a high level of process reliability. Precise coordination is required only during the start-up and shut-down phase to avoid product losses.
The relatively small footprint requirements are an advantage, especially the lower height requirements. Commissioning is simple for qualified and well-trained personnel, as the weighing unit and the feeding device are one unit.
Key Advantages of Continuous Feeding:
– Substantial throughput
– High process reliability
– Smaller footprint and low height
– Fewer operating staff required
– Suitable for feeding of micro quantities
Key Disadvantages of Continuous Feeding:
- More planning required
- Start-up and shut-down can be more complex
Why choose a Batch Process?
Batch feeding systems are suitable for limited production quantities with multiple recipe changes. There are two types of batch processes: gain-in-weight and loss-in-weight. Both processes offer different advantages and disadvantages for different applications. Gain-in-weight processes involve sequential feeding into a weighed hopper, while loss-in-weight processes allow for parallel feeding.
All batch processes require meticulous planning, you must consider factors like temperature, humidity, explosion prevention, and working conditions. Volumetric feeding is simpler but less accurate for small batches, while gravimetric feeding ensures accuracy for all ingredients.
Key Advantages of Volumetric Feeding:
– Suitable for large batches
– Different recipes/formulations feasible
– Easy to control
– Uncomplicated planning and installation
Key Disadvantages of Volumetric Feeding:
– Larger footprint
– More reliant on staff operation
Key Advantages of Gravimetric Feeding:
– Simple product changeovers
– High process reliability
– No product losses
– Smaller footprint
– Uncomplicated commissioning
Key Disadvantages of Gravimetric Feeding:
– More effort required for large batches
Industry Trends and Applications
The industry trends in feeding processes are leaning towards continuous systems, especially in industries like pharmaceuticals, tire manufacturing, and powder coating.
The shift is evident in applications such as adhesive feeding in hotmelt processes, battery production, dry cereal mixing, granola bars, baked goods, dough products, and vegan meat substitutes.
Despite the planning challenges, the advantages of automation, improved product quality, and smaller equipment footprint make continuous processes increasingly popular.
In conclusion, the choice between continuous and batch feeding processes depends on your specific production requirements. While batch processes offer simplicity for smaller volumes, the advantages of continuous systems are becoming more apparent, particularly in industries focused on automation, quality, and efficiency. As technology evolves, the shift towards continuous feeding processes is expected to continue.
For more information on Continuous vs Batch Feeding Processes talk to Genesis Process Solutions