
Sign In
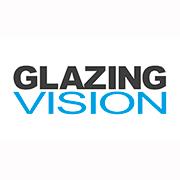
Glass, when installed overhead in rooflights and skylights must be ‘safety glass’, which is often referred to as Toughened or Tempered Glass.
Toughened glass is 4-5 times stronger than standard annealed glass of the same thickness; it’s a key safety feature in the specification of domestic rooflights and skylights as it is designed to crumble into granular type fragments when broken, rather than shatter into jagged shards like annealed glass. This significantly helps to reduce the risk of injury.
How is toughened glass made?
Toughened glass is produced by passing annealed glass through a furnace, heating it to above 600°C before being rapidly cooled. A balance of high compressive stresses at the surface and tensile stresses in the centre of the glass increase its strength. When the glass breaks it is the release of these stresses that causes it to break into small pieces – usually accompanied by a large bang as the energy is released.
Toughened (tempered) glass is a preferred option for rooflights but there can be disadvantages. Firstly, glass needs to be cut to the required size and shape before it’s treated.
Secondly, toughened glass has been known to spontaneously fracture for no apparent reason with the most likely culprit being Nickel Sulphide (NiS) inclusions within the glass.
NiS is a chemical contaminant that can manifest itself during the toughening process; as it gradually changes state over time it can cause the glass to fracture. This can happen at any time, from a few weeks to many years or not at all.
One of the most effective ways of combatting this it to subject the glass to Heat Soak Testing.
Heat Soak Testing
Heat soak testing is carried out during the manufacture of the glass and will filter out around 95% of problem units. This involves heating tempered glass up to 290 degrees Celsius and holding it at that temperature over a controlled period of time. This process accelerates any NiS inclusions reverting back to their Beta state, which could result in glass failure.
Whilst more expensive, this method of testing identifies any issues with toughened glass before it’s used in manufacture. This is of particular importance when specifying larger structural rooflights or those used for walk on applications, where heat soak testing is a requirement of Building Regulation.
Laminated Glass
Annealed laminated glass can also be specified for some rooflight applications, to conform to BS5516 Part 2 – pane sizes above 3m2 and between 5mts and 13mts from floor level should be laminated.
Laminated glass is produced by combining two or more sheets of float glass with one or more interlayers. Glass integrity is maintained from a ‘laminated’ interlayer, commonly PolyVinylButyl (PVB), which is processed with heat and pressure under factory conditions.
Should any damage occur, the interlayer holds any fragments together preventing them from falling, reducing injury risk even further.
Combinations
Toughened Laminated or HST Toughened Laminated are also common glass specifications, particularly when the glass has to perform a structural function, as in a glass floor or structural glass fins.
For more information on The importance of using toughened glass for domestic rooflights and skylights talk to Glazing Vision Ltd
Enquire Now
List your company on FindTheNeedle.