
Sign In
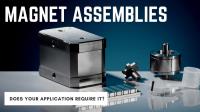
Magnet assemblies
Our blogs are specifically crafted to help you better understand the complex and sometimes puzzling world of magnets. In recent posts, we discussed material grade selection, magnetic applications and understanding the different materials available. This post explains how magnet assemblies work and why they prove to be a common solution for many magnetic applications.
What are the benefits of magnet assemblies?
A magnet assembly incorporates magnet and non-magnet materials, usually magnetising them together to create a stronger magnetic circuit. The non-magnet materials typically incorporate mounting mechanisms for holding applications, while also protecting the magnet material from damage during use. In addition to this, magnet assemblies offer 3 main benefits:
1. Increased mechanical strength
When deciding on a magnetic assembly, it’s important to take into consideration that the magnet alloys have an inherently brittle composition. Depending on the application, magnets are often exposed to continuous mechanical stresses and thus may suffer volume loss. Therefore, causing part of the magnet to chip away from the main body, causing a weakening of the magnetic field. To prevent this, magnets are often combined or integrated with non-magnetic components, such as plastic, ferrous metals or non-ferrous metals. This creates a protective housing that prevents volume loss. Some common examples of magnetic assemblies include:
Pot magnets
Rail magnets
Channel magnets
2. Increased magnetic strength
Not only do magnet assemblies increase mechanical strength, they can also contribute to increased magnetic strength. When compared to a raw magnet, magnetic assemblies frequently have a higher magnetic force. Simply because the flux conducting elements found in the assembly are an essential part of the magnetic circuit. These elements, through magnetic induction, enhance the assembly’s field on the region of interest. However, this technique works best when using the magnetic assembly in direct contact with a work-piece where even the smallest gaps can dramatically impact the magnetic field. These gaps can be an actual air-gap or any coating or debris which causes a disruption in the assembly of the work-piece.
3. Mounting and special design features
Magnetic assemblies can be integrated by a variety of methods, however most tend to be mechanical. The most common type is press-fitting, using a mechanical fastener. Mechanical fastener mounting will also make use of an incorporated tapped or through hole in the assembly.
Assembly methods
Magnet assembly manufacturing methods are as diverse as the materials and magnetic alloys used in them. Hence why we offer a range of assembly techniques to suit various applications, including:
Mechanical Assembly
Insert Moulding
Over Moulding
Gluing
Heat Staking
Ultrasonic Welding
Brazing
Does your application require a magnet assembly?
Customers often ask whether a magnetic assembly is a cost-effective solution for their application. Depending if it results in increased magnetic performance and part longevity, a magnetic assembly may be a cost-effective option. Our team of experienced engineers can assist you in determining if a magnetic assembly is a viable option. For more information contact us today at info@goudsmit.co.uk, or if you’d like to speak to a member of our team call us on +44 (0) 2890 271 001.
If you would like more information on our magnetic products visit our brochure or our magnetic grades webpage.
Follow us on LinkedIn, Twitter and Facebook for regular updates.
For more information on Magnet Assemblies: Does Your Application Require It? talk to Goudsmit Magnetics (UK) Ltd
Enquire Now
List your company on FindTheNeedle.