
Sign In
Neodymium Magnets: How to Prevent Corrosion
29-03-2018
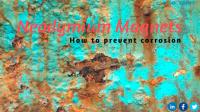
Why do neodymium magnets corrode?
Iron displays the most dramatic ferromagnetic properties of all elements, which is why it is found in the most powerful magnets. Therefore, meaning that every permanent magnet contains a form of iron. However, iron is highly reactive to water and hence makes magnets with high iron content, like neodymium, very vulnerable to corrosion and possible demagnetisation in the long run.
The strongest permanent magnets available are neodymium magnets, but because of their high iron content (64-68%) they are highly prone to corrosion in moist environments. Modern manufacturing techniques have seen traces of other rare earth elements such as dysprosium added to the NdFeb alloy to improve resistance to corrosion as well as other magnetic properties. Due to their vulnerability to corrosion, neodymium magnets are almost always coated before being used in any application.
Neodymium Coatings
Neodymium magnets are so prone to corrosion, that even the moisture in the atmosphere can cause them to corrode over time. The typical coating for a neodymium magnet is a layer of nickel followed by a layer of copper and then nickel again. However, there are a variety of different coatings available. Below are some of the most common coatings and their characteristics.
1. Nickel (Ni-Cu-Ni)
The most commonly used coating
Nickel has a good price/performance ratio
Thickness: approx. 12 micro metres
Colour: shiny metallic
2. Gold-coating (Ni-Cu-Ni-Au)
Razor-thin coating over normal nickel coat
Thickness of gold-coating without nickel: 0.05 micro metre
Thickness of whole coating: approx. 12 micro metres
Colour: shiny metallic
Gold-coating rubs off easily with frequent use, therefore it is suitable for decorative purposes only.
3. Chrome (Ni-Cu-Ni-Cr)
Better resistance against rubbing and pressure, thus its commonly used for sphere magnets
Thickness: approx. 15 micro metres
Colour: dull, grey-metallic
4. Copper (Ni-Cu)
Slightly weaker rubbing and impact resistance than nickel
Also, a slightly weaker corrosion resistance than nickel
Thickness: approx. 10 micro metres
Colour: shiny brown-red-gold. However, the colour may change over time due to rust
Like the gold-coated magnets, the copper-coloured surface rubs off with frequent use. Therefore, they are for decorative purposes only.
5. Epoxy resin (Ni-Cu-Ni-Epoxy)
Not shock-resistant, so it crumbles quickly
Almost 100% non-corrosive, if coating is intact
Thickness: approx. 10 micrometres
Colour: black
Even the smallest damages to the coating will cause damage to the magnet in the long term when exposed to moisture.
What about samarium cobalt magnets?
Samarium cobalt magnets have a significantly higher level of resistance to corrosion even without a protective coating. However, most SmCo magnets are still coated, but this is largely for visual or application-specific reasons. With their higher levels of resistance, SmCo magnets are widely used in offshore applications when they are constantly exposed to extremely harsh environments.
A lower magnetic performance but improved corrosion resistance?
Alnico and Ferrite magnets both resist corrosion naturally, but they don’t have anywhere near the same level of magnetic performance as samarium cobalt and neodymium magnets.
Some grades of alnico magnets do contain traces of iron and therefore will display some light surface corrosion over time if exposed to water. However, alnico performs exceptionally well in the presence of other lubricants, like:
Oil
Alcohol
Solvents
Goudsmit UK
With our years of experience and expertise, at Goudsmit UK we can offer the best solution for your application. Not to forget that we can carry out the manufacture, coating, magnetisation, inspection and shipping of your products to ISO 9001, AS 9100 and TS 16949 quality standards.
Contact us today at info@goudsmit.co.uk of if you’d rather speak to a member of our team, call us on (0) 2890 271 001.
For more information on our magnetic products visit our magnetic grades webpage or our brochure.
Follow us on LinkedIn, Twitter and Facebook for regular updates.
For more information on Neodymium Magnets: How to Prevent Corrosion talk to Goudsmit Magnetics (UK) Ltd
Enquire Now
List your company on FindTheNeedle.