
Sign In
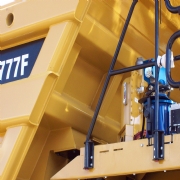
Interlube Systems have developed a unique automatic lubrication system which is already showing huge savings in work time and running costs. The Interlube System provides continuous lubrication to all moving parts whilst the plant is still in operation . Constant controlled lubrication means that the plant is being lubricated whilst in operation on site, this gives adequate and even lubrication all the time, something that cannot be maintained if the machine has to be "parked up" for servicing.The long term benefits includes radical reduction in worn and damaged parts caused by erratic and irregular lubrication, and plant downtime for replacement of lubrication is dispensed with.
The revolutionary Interlube Electric Keg Pump System, which has a fully automated monitoring facility, is now being installed at many Open Cast Coal Mines throughout Europe. Customers are discovering that, amongst other things, there is no reservoir re-fill requirement, only a grease keg which needs changing periodically. This innovative system also monitors the correct and continuous operating facility, indicating to the operator if a vital grease point is not been served. this is done by checking the actual flow of grease and not the unreliable check on pressure. The Interlube Keg system will not airlock, unlike conventional systems, so any grease distribution blockage can be quickly and easily identified. In the very unlikely event of a problem occurring with the integral pump or the electronic controller then the system can be hand lubricated through an integral built in greasing nipple with a standard side lever grease gun. The Interlube Keg system operates with NLGI2 greases and can be connected to a hose reel facility so that smaller operating units can also be lubricated in tandem.
In many cases large plant often needs to be "tracked" back to the workshop for grease reservoirs to be refilled, an operation that could be necessary every 3 working days! Using the Interlube System the grease keg only needs replacing every 7 to 10 days, and the changeover can be done at the working site location without interruption to the plant lubrication facility.
One satisfied customer has had 14 units installed on site. The figures show that large savings have been experienced. The operator in question previously had to allow one hour to move the machine to and from the site face to the workshop, and half an hour to refill the grease storage unit. With the new Interlube electric Keg System this down time and inconvenience has been eliminated.
Interlube have a dedicated and experience design and sales team and can tailor the Interlube Electric Keg System to your specific requirements. For further information on this product or to discuss any lubrication problem please ring sales on +44 (0)1752676000 info@interlubesystems.com
For more information on Interlube`s Automatic Lubrication System saves both time and money talk to Groeneveld UK Ltd
Enquire Now
List your company on FindTheNeedle.