
Sign In
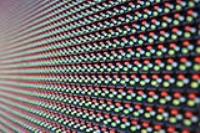
Posted on August 5, 2015 by Ross
The market for Light Emitting Diodes (LEDs) has exploded in recent years. Designers and engineers from a broad range of sectors are scrambling to use these components in new and innovative technologies.
However, as the demand for LED based products increases, there is a growing concern that some developers are ignoring the principles of thermal management when it comes designing products with lots densely packed LEDs.
Keeping LEDs cool is essential to maximising efficiency and reducing failure rates in electronic products.
Swelling demand for LED technology
LED displays have several advantages over traditional ‘lighting’ systems. These advantages have prompted a surge in demand for LED-based products over the last decade or so.
LED displays are brighter than traditional filament bulbs. This makes them more useful for outdoor displays shop signs and billboards which need to illuminate the night.
They also use less energy than normal bulbs. A growing concern about energy conservation among end-users can account for at least part of the rising demand for LED technology.
In order to corner this market, designers in technicians in a broad range of industries will not only need to be creative, but they will also need to make sure they make the best use of the available technology. Making products as practical and efficient as possible is the name of the game for designers using LED displays. And to do it right they will need to have an understanding of thermal management.
Basics of LED thermal management
At least 70% of the energy going into an LED will be wasted as heat instead of light. If a design incorporates lots of LEDs in a tight area then that heat needs to disperse quickly in order to keep the circuit board and the product within a safe operating temperature. It may also be necessary to use a different material in your Printed Circuit Board (PCB).
Circuits which fail to manage temperature effectively run a serious risk of failure. Most LEDs are supposed to have a 50,000-hour lifetime so premature failure can be seriously damaging to your reputation.
What’s more, if your LEDs are ‘running hot’ then they are probably dragging down the efficiency rating for your product as a whole. If you are not careful then your product could be operating at a sub-optimum capacity and it could also receive criticism as being environmentally damaging – a criticism which can carries a harsh penalty in this environmentally conscious age.
Hot LEDs could also be having a knock-on effect on other components in your circuit, thus multiplying the problems associated with inefficient design and circuit layout.
When is thermal management of LEDs Important?
For many low-power LEDs (less than 1W), thermal management can be ignored. Any excess heat in these products will be conducted away through a standard polymer PCB.
Thermal management becomes more important when you have many high-brightness LEDs squeezed tightly in one unit. These pre-packaged LED ‘panels’ need a thermally conductive sub-mount to transfer any excess heat away from components where it might cause damage.
Special thermal PCBs for LED-based electronic products
If your design includes lots of high-power LEDs packed densely into a small surface area, then it might be necessary to use a different type of PCB. For these designs it is usually recommended to avoid using polymer board. Instead designers are advised to use a ‘Metal-in-Board’ PCB.
These boards come with a base plate of aluminium which conducts heat away from danger areas. They also have a top layer of copper which runs underneath an arrangement of LEDs.
For more information on Why The Thermal Management Of LEDs Is Important talk to Hi5 Electronics Ltd
Enquire Now
List your company on FindTheNeedle.