
Sign In
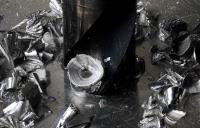
When carried out using the right equipment and with the right training, gundrilling delivers reliable results each time. This is the reason the technique – which you may also know as deep hole drilling – is so widely used in manufacturing. Hundreds of aerospace, automotive and medical components, among others, use gun drilling to produce precision holes of almost any length.
Gundrilling is a precise science that can be tightly controlled to deliver results within very tight parameters, but there are still several factors to take into consideration. A precise result is achieved by controlling four variables, which we will look at below:
1) Fluid Volume/Flow Rate
How much coolant do you need to achieve your result? Although total volume and flow rate are technically two factors, it makes sense to deal with them together. For each revolution of your drill, you will need enough coolant to completely fill the drill hole. To determine this you need to know:
The speed of your drill bit in rpm
The diameter of the gun drill
The depth of the drill hole
Volume (V) and flow rate in gallons per minute (GPM) can be calculated using two simple equations:
V= (0.785x diameter2 x depth) / 231
GPM = V x RPM of drill
Doing these in order will give you a rough figure for your flow rate, e.g. 0.5 GPM. However, in practice your flow rate will always be less due to losses from friction. It is therefore important to control the pressure of your drill.
2) Pressure
Gundrilling CNC operations are high-pressure systems. Maintaining stable pressure in psi is important to retain the correct flow rate. However, blockages can occur, resulting in a build-up of pressure, which can jeopardise the safety of the machine and operators. It’s therefore important to have efficient pump sensors that can moderate the flow of coolant and avoid pressure build up. Clearing a blockage always requires more coolant volume to flush away the obstruction, but this can risk increasing pressure still further at a critical point. The answer is to have a surplus of coolant volume available on top of that which was calculated by your base equations.
3) Feed Rate
Drill feed rate affects how easily the drill cuts into the material, and how efficiently it removes swarf from the cutting zone. Your feed rate will also affect the size of the chips themselves. Higher feed rates often create a proportionately higher work hardening rate. This creates smaller chips that are easier to disperse.
For more information on How To Achieve A Perfect Result With Gundrilling talk to Hone-All Precision Ltd
Enquire Now
More News
List your company on FindTheNeedle.