
Sign In
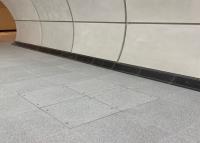
The legislative and regulatory landscape which specifiers, contractors and manufacturers must operate within with regard to fire safety is currently shifting at a pace not seen for decades. Here Chris George, Business Development Manager at Howe Green, explores the latest advancements and what they mean for the entire industry with regard to the testing and certification of building components.
The housing secretary recently appointed Paul Morrell, an industry veteran and former chief construction advisor to the government, and Anneliese Day, a leading legal expert within the construction sector, to lead an independent review into the current testing requirements for construction products.
This review may lead to significant legislative updates regarding the testing regime in England and Wales. It is just the latest development in a long line of industry advancements, including the Grenfell inquiry, Hackitt Report and the formation of the National Construction Products Regulator. Each of these activities share the same commitment to creating a more robust testing regime that will improve the level of safety and accountability throughout the entire construction sector.
However, if the industry is to drive and achieve this cultural step change with regard to how fire integrity products are tested, certified, specified, installed and maintained, there must be a new-found sense of collaboration and transparency fostered between manufacturers, specifiers and contractors to ensure the most suitable and compliant products are consistently specified.
Whilst much of the industry commentary on the issue of fire safety initially centred around combustible cladding and insulation, these latest regulatory advancements have broadened the scope to focus on all types of building materials and components, including access solutions that house electrical and mechanical systems.
Due to the very nature of these products, ensuring rigorous specification processes is vital to achieving both successful specification and continued adherence with all relevant regulations.
Access solutions, such as floor access covers, are essential to providing discreet and concealed access to necessary areas of maintenance, particularly for high trafficked commercial applications including healthcare and transport. As these types of underfloor services also often join multiple building areas together, they play a pivotal role in limiting the potential transfer of fire, which can easily spread between gaps in the building structure.
When specifying and installing floor access solutions for commercial projects, professionals must first ensure the product is compliant with BS476 – Part 22 and the requirements outlined within Approved Document B of the Building Regulations 2010 of England and Wales. The installation of floor access solutions that do not meet the standard set out in legislation can result in potentially unlimited fines. It is the shared responsibility of the manufacturer, specifier, architect and contractor to ensure the most suitable and compliant product is installed.
Efficient communication and availability of relevant information and documentation is essential to achieving successful specification with regard to fire integrity products. This ‘golden thread’ of building information must be available from the initial design stages, right through to maintenance, to ensure every project remains safe for the individuals who inhabit it.
To go above and beyond current compliance and ensure a structure is fit for purpose, and for the future, specifiers must work with manufacturers who can demonstrate compliance with current regulations and prove their building components offer the very highest standards in fire integrity and performance.
The current testing regime has created significant inconsistency regarding the testing and certification of building components. For example, some manufacturers may only conduct their own product assessments, while others may undertake continuous rigorous product testing and certification to evidence their products are consistently suitable for installation.
To take a proactive approach and achieve the aims of the government’s advancements before they come into force, professionals should specify building products that have been tested and certified by an accredited third party. This not only fulfils duty of care in terms of best practice, but also proves the access solution goes above and beyond current requirements to offer the highest standards in quality, performance and safety.
The certification of a product by an accredited third party, rather than being tested by the manufacturer themselves, provides third party reassurance that it will not fail in the event of a fire. This is due to the product being supported by comprehensive test documentation that physically proves its suitability and performance, not only for the outlined duration but throughout every stage of the manufacturing process.
This enables all professionals involved through every stage of the construction process to demonstrate a comprehensive trail of due diligence, allowing key information to be consistently communicated and referred to. This has the additional benefit of fostering a close level of collaboration between all parties to streamline each stage of the design, specification and installation stages.
Howe Green’s 1050 Series and 7500 Series Floor Access Covers are tested for up to two hours for fire integrity and insulation. The access covers are available in single, duct or multi-part configurations to provide professionals with the highest standards in compliance and performance.
For further information on Howe Green’s complete range of floor access solutions call 01920 463230.
For more information on A NEW FUTURE FOR FIRE TESTING AND CERTIFICATION talk to Howe Green Ltd
Enquire Now
More News
List your company on FindTheNeedle.