
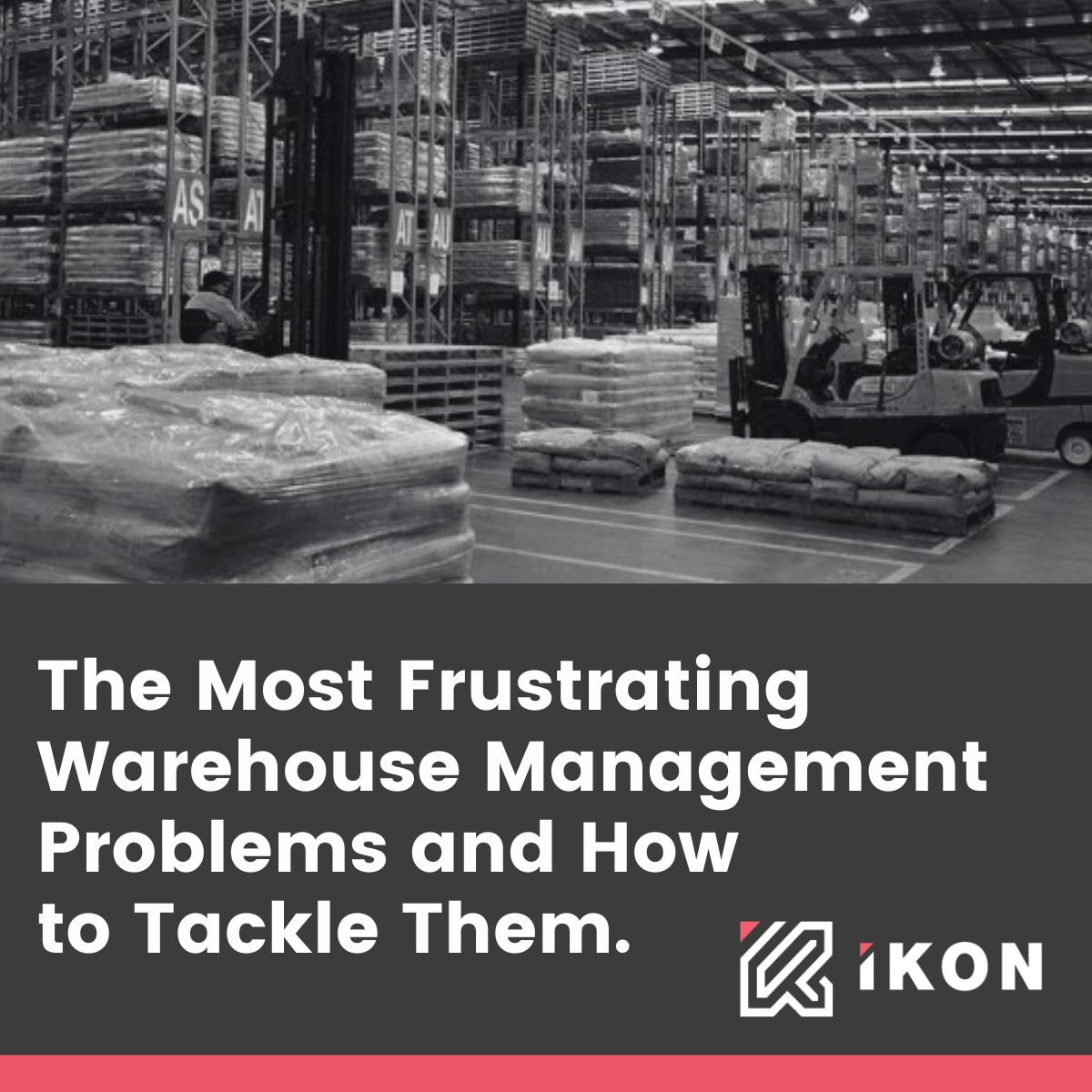
Warehouse management involves organising, managing, and maintaining all the processes that occur in a warehouse so that they run as smoothly and efficiently as possible. Even though some of these processes are automated and seem error-free, every warehouse operation is prone to mistakes and challenges. According to a report by McKinsey & Company in 2019, about £300 billion is spent each year worldwide on overall warehousing costs. And that amount doesn’t include the additional costs of correcting errors and mistakes.
Warehouse problems can affect the speed, efficiency, and productivity of either one warehouse operation or the entire chain of processes. In most cases, these errors are only identified after the process has begun or even after it has been completed. And by then, it’s usually too late to prevent the mistake—it may even be too late to reduce the damage done. But with prior knowledge about the potential challenges in your warehouse operations, you can predict them and stop the damage before it starts.
In this blog, we will cover some of the most common problems faced in warehouse management and how to stay clear of them.
DISORGANISED WAREHOUSE LAYOUT
Due to the increasing storage cost, warehouse managers have been forced to find more efficient ways to use their space. However, according to a Logistics Management survey in 2018, manufacturers’ average warehouse capacity utilisation was only 68%, indicating that ineffective use of space was a common challenge for warehouses then and, from our experience, still is today. To tackle this issue, an optimal warehouse layout should be developed, which includes maximising floor and vertical space usage while providing adequate room for employees to move around. Additionally, exploring automation and equipment to reduce labour and costs, improving product accessibility, systematically organising inventory, and ensuring safe inventory storage are all crucial components of a successful warehouse layout.
To start optimising your use of warehouse space:
- To better organise your warehouse layout, consider using technology like a warehouse management system (WMS). With the dimensions and measurements of your warehouse and inventory, some WMSs can even provide a 3D model of the best arrangement. Another option is an automated storage and retrieval system (AS/RS), which uses computer-controlled equipment to automate your putaway and picking processes. This improves efficiency and saves valuable warehouse floor space that would otherwise go to waste.
- You can opt for a more straightforward approach if you’re not prepared to upgrade your technology. Utilise your current inventory and sales management solution to determine which products sell the fastest. Then, ensure that these items are stored in easily accessible locations, allowing for quick retrieval and restocking.
ACCIDENTAL REDUNDANCY
Warehouses often have multiple operations for each item, strung together to create workflows. However, if the workflow is disorganised, the same procedure may accidentally be performed more than once. This can increase labour costs and waste time by having to go back and reverse the mistake. Redundancies are more common in giant warehouses due to the increased inventory and space. Redundancy is frequently noticed in order picking, where products are picked from storage to fulfil an order. In smaller warehouses, order picking is usually done by one person, which leaves little room for error. In larger warehouses, multiple people work together to fill a single order, increasing the chances of mistakes, such as picking too many of the same product. A solution to reduce redundancy is to invest in technology, such as a modern warehouse execution system (WES), to automate redundant processes. For example, barcode technology could scan picked products for orders and notify users of duplicates.
POOR INVENTORY MANAGEMENT
Have you been experiencing any of these issues?
- Expecting to find a product in a specific location, but realising it’s placed elsewhere.
- Accepting an order on the assumption that you have enough stock to fulfil it and only later finding out that you don’t. Now you have to place a backorder, significantly extending your order lead time.
- Denying an order after assuming you don’t have enough stock to fulfil it, but then finding out that you do.
- Trying to put away stock you’ve received but needing help finding where to place it.
Any of these problems can indicate that you need to maintain accurate inventory records and update them consistently. Miscalculations can easily happen when inventory-checking processes are done manually since this leaves room for human error. Sometimes they can also occur when using outdated software.
One way to overcome these warehouse challenges is by switching to a newer solution. This could be a system specific to inventory management or an overall warehouse management software with real-time inventory management features. A typical system first collects your inventory data through a handheld or fixed device such as a barcode scanner. This information is sent to your software solution, which catalogues and tracks your inventory.
LACK OF PREPAREDNESS FOR SEASONAL DEMANDS
Certain products experience the same demand all year round, whereas others are more popular during specific times of the year. Sudden influxes of demand that take you by surprise can cause damage, as your warehouse might not be prepared to take on the orders. This could be because you don’t have enough products in stock or because you don’t know where to store them on such short notice. It’s essential to be aware of the current market trends and the fluctuations in demand for the products you work with to be ready to manage your changing stock levels.
Here is how you can prepare for seasonal demands:
- Stay in contact with your manufacturers, distributors, retailers, transporters, and any other sources you have from your industry. This way, every part of the supply chain can have the same information about demand fluctuations and can work together to respond accordingly.
- You can also use demand forecasting techniques to determine what products you need in your seasonal inventory.
- Arrange and organise your products to help push out your seasonal products faster. This means placing them in the most convenient spaces in your warehouses to be easily put away and picked for orders.
- Consider warehouse equipment and automation tools such as pallet flow rack systems, forklift trucks, and AS/RS to help your processes flow better and quicker.
UNSATISFACTORY ORDER MANAGEMENT
Even though order management is one of the most critical operations in a warehouse, it also reports the most errors. Order management consists of all the processes that start when an order is received, from accepting the order to picking, packing, and shipping the right products to the right customer and handling post-sales processes like refunds and returns if needed. A mistake in any of these processes can collapse the workflow, which means redoing all the steps from the start. This is a massive waste of time and money, meaning your customer will get their order later than expected.
To help keep their orders running smoothly, a lot of businesses choose to use an order management system. This can help you manage your overall order management and fulfilment processes, including shipping, customer notifications, and depending on the type of solution you choose, even inventory management. In addition to saving time, high order fulfilment accuracy rates can also help your profitability.
POOR DAMAGE CONTROL
Damage is, unfortunately, a common issue in warehouses, especially ones that deal with a large amount of inventory and heavy-duty equipment. While avoiding damage altogether is difficult, you can always work on ways to reduce it.
Install protective gear like pallet rack protectors, special nets for racks, guard rails, anti-slip tape, lockout systems, low clearance warning bars, and accumulation conveyor systems. Also, ensure your pathways are well-lit and wide enough to move around products comfortably. These measures will help you protect your employees, equipment, and inventory and prevent workplace accidents.
Conduct regular inspections throughout your warehouse to look for early signs of damage (we can help with this) to your equipment, storage units, or vehicles. For instance, check your storage shelves and pallets for overloading, cracks, and breakage. In addition, look for other types of damage that can eventually cause problems, such as water damage or pests.
Warehouse management is one of the most essential processes in a warehouse, and it’s not one where you can afford to mess up. Since most tasks involved in warehouse management are linked in some way, a problem in one can lead to costly errors in others as well. Accidental redundancy, having a messy warehouse, poor inventory management, poor preparedness for seasonal demands, unsatisfactory order management, excessive spending on labour, and poor damage control can cost you money and derail your warehouse operations. By educating yourself about the potential warehouse challenges your warehouse may face and their solutions, you can reduce the damage caused by these errors or even prevent them from happening.
A warehouse management system can help you maintain a smooth-running warehouse without these hiccups. Many Inventory cloud-based warehouse management solutions can manage multiple warehouses, organise your sales and transfer orders, provide real-time data about your inventory, and give you accurate reports in a flash.
We hope this has provided you with insights on how to tackle the most frustrating issues in warehouse management. If you require additional help, please don’t hesitate to contact us.
For more information on FRUSTRATING WAREHOUSE MANAGEMENT PROBLEMS AND HOW TO TACKLE THEM talk to IKON Solutions ltd