
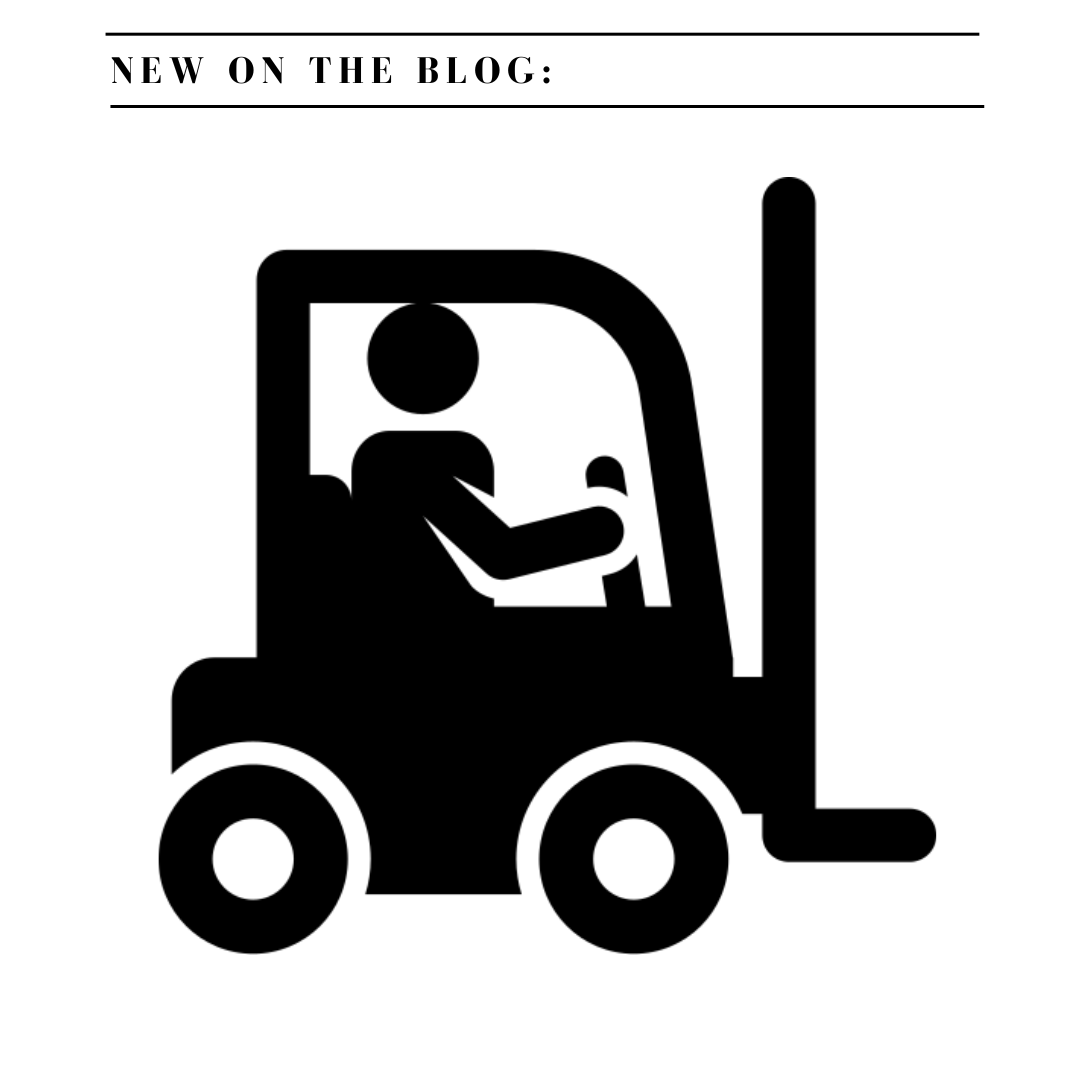
Warehouses and distribution centres are full of potentially lethal machinery and equipment. In this post we consider the vital importance of safety in warehouse environments.
Workplace related injuries in the UK are sadly very high with thousands of workers injured or killed every year in avoidable accidents. Between 2021 and 2022 around 36.8 million working days were lost due to work related injury and illness. During this time 123 workers were killed and 565,000 were injured.
Latest figures from the Health and Safety Executive (July 2023) show a 10% year-on-year increase in the number of workers killed in work related incidents to 135 between 2022 and 2023. This is equivalent to the number recorded in 2016/17 but fewer than the number of deaths in 2018/19 when 149 people lost their lives in work related accidents.
Most Common Warehouse Accidents
While the construction sector has the highest number of workplace fatalities the safety and security of distribution centre and warehouse workers has been highlighted by issues at various locations.
Forklift related accidents are cited as a primary cause of many injuries and deaths. It is estimated that thousands of workers are injured every year due to the use of forklifts. Warehouses and distribution centres are busy environments in which people are working under pressure to maintain the flow of often cumbersome items. Those responsible for operating forklifts need to be properly trained and vehicles must be well maintained and always used in accordance with strict best practices.
Slips, trips and falls are another of the most common accidents suffered by warehouse workers. Spills of powders, oil and fluids create hazards along with exposed electrical cabling and items obstructing walkways. It is essential that all workers are fully trained in safe working practices and hazards are recognised and promptly dealt with when they arise.
Overexertion and improper lifting is another common cause of musculoskeletal injuries to warehouse workers. Warehouse staff are far more likely to experience injury due to poor lifting practices than workers in other industries. This is another example of where appropriate training along with suitable assistive technologies are vital.
Warehouse workers are also particularly susceptible to being hit by falling objects. Lofty warehouse storage systems and pallet stacks can present safety risks. Falling objects and collapsing stacks of pallets are known to have caused staff injuries.
The safe handling of hazardous materials is another common responsibility for warehouse workers. If consignments of hazardous materials are damaged the spilled contents can potentially cause burns, respiratory issues and fire risk. Some materials may even be carcinogenic or cause organ failure.
How to Make Warehouse Environments Safe for Workers
Warehouse safety requirements are complex and can vary from one site to another. Various elements of UK legislation on warehouse safety have been collated into a useful publication from the Health and Safety Executive called: Warehousing And Storage: A Guide To Health And Safety, HSG76. This book is the go-to safety reference resource for all warehouse and distribution centre operators in the UK.
Creating and maintaining a safe warehouse working environment requires commitment from all levels of an organisation. It involves an effective combination of property planning, staff training, adherence to rigorous best practices and the use of appropriate equipment and safety systems.
Risk Assessment and Planning
Risk assessment is a vital requirement in all warehouse environments. Its an ongoing process that needs to be routinely conducted to ensure developing hazards are spotted and mitigated before they cause accidents and injuries.
All potential hazards need to be identified such as the use of forklifts and other moving machinery, the handling of hazardous materials, high storage shelving and racks, uneven surfaces, poor lighting and slippery surfaces. Risks should be allocated appropriate priorities based on the threats they present and steps should be taken to ensure staff safety.
The design, layout and organisation of warehouse environments should be considerately planned to minimise congestion, reduce the risk of collisions and ensure optimal, safe flow and movement throughout the warehouse environment.
Staff Training and Education
Inadequate or out of date employee training is often cited as a primary cause of warehouse accidents. It should be ensured that all staff are fully trained in all aspects of warehouse safety including safety protocols, how to safely use various pieces of warehouse equipment (including forklifts), emergency procedures, safe material handling, safe lifting practices and how to properly use personal protective equipment.
Staff should routinely undergo safety training updates to make certain they are always up to date with new safety procedures. Employers need to ensure safe working practices are always a staff priority.
Personal Protective Equipment (PPE)
Its essential that warehouse workers are provided with appropriate personal protective equipment and they know how to use it. PPE items typically include helmets, goggles, gloves, high-visibility jackets and vests, steel-toecap footwear and respiratory protection masks. In environments where hazardous materials are being handled staff should be fully trained in safe handling, how to protect themselves with PPE and what to do in the event of a spill.
Handling Procedures
As previously highlighted, many workers experience injury due to poor lifting and carrying techniques. Employees need to know how to assess objects before attempting to lift them, correct and safe lifting procedures and how to carry items safely. They also need to know how to safely and correctly use warehouse equipment such as forklifts, lifting aids and pallet jacks.
Shelving and racking systems should be clearly labelled with weight limits and workers need to understand how to avoid overloading. They also need to be instructed in how to safely stow items on storage shelving to avoid the risk of things falling.
As noted, warehouse workers also need to know how to deal with damage and spills. If there are hazardous materials they need to know what they are and how they can be safety dealt with if packaging is damaged.
Equipment Maintenance and Safety
Ongoing maintenance and routine inspection of equipment and storage systems is vitally important. Any faults in forklifts, loading dock equipment, conveyors and other systems must be identified and promptly fixed. Shelving, racks and storage containers should be regularly inspected and verified as safe.
Emergency Procedures
All warehouse environments require clearly defined and shared evacuation plans. Staff should be trained in all emergency procedures and regular drills must be carried out to make certain all staff know where the emergency exits are located and where they need to muster in the event of an emergency.
The locations of first aid kits, fire extinguishers and safety equipment should be easily accessible and all staff should know where they are. Staff should also know who the designated first-aiders are and what they need to do if a workmate needs urgent attention.
Fire Safety
Fire safety starts with fire prevention. Risk assessment should determine the potential for fire, enabling appropriate preventative measures to be established. Electrical systems, for example, can cause fires if overloaded, damaged or poorly maintained. And handling flammable materials is another potential fire-risk factor.
Fire extinguishers should be suitable for the environment and types of fire that may occur. They should be located in easily accessed locations with clear signage and all staff should be trained in how to use them. Extinguishers need to be routinely inspected for damage or tampering and serviced every 12 months.
Appropriate Signage and Clear Communication
Its important to ensure signage, such as shelving weight limits, is clear and visible. Emergency exits should be easily identified along with the locations of all fire extinguishers and first aid kits. Safety procedures should be prominently displayed and hazardous areas clearly identified.
Procedures for reporting safety concerns and incidents should be known to all staff and effective lines of communication should encourage workers to express their safety concerns.
Ergonomics and Employee Wellness
Accidents can happen when people are tired and losing concentration. Its important to provide facilities for staff to take breaks and rest. The ergonomics of various work areas should be examined and designed to prevent repetitive strain injury and enable staff to work safely in comfort.
Continuous Reassessment and Improvement
Its important that employers understand the need for continuous reassessment of all aspects of workplace safety and conduct regular audits to make certain new risks are identified before they cause problems. Encouraging employees to provide feedback on safety concerns and suggestions for safety enhancement is also very valuable.
How Convex Mirrors Improve Warehouse Safety
Warehouses and distribution centres are highly dynamic, busy environments that are often operational 24 hours a day. Staff need to safely use walkways alongside forklifts, pallet jacks and other pieces of potentially dangerous equipment. Safely maintaining a steady flow of items both in and out of warehouse environments is challenging.

One of the challenges in these busy environments is poor visibility. Shelving, storage and racking systems make it impossible to see what’s around the corner and who might be approaching. This is where some considerately located convex mirrors significantly enhance safety.
Convex mirrors provide a wide field of view which is why they are widely used to aid road safety. They are often located on the roadside, opposite driveways, enabling drivers to see oncoming traffic before they pull out onto the road. Similarly, in warehouse environments convex mirrors make it easier for workers and equipment operators to effectively see around corners and avoid collisions.
Warehouses often have intersections and areas where its difficult for staff to see what’s coming. And when workers are busy the potential for accidents increases. Improving visibility in these warehouse areas reduces the risk of accidents involving vehicles, equipment and pedestrians. When forklift drivers and those on foot can clearly see each other they can react quickly to avoid nasty collisions. Convex mirrors enable workers to anticipate potential hazards and mitigate risks.
Convex mirrors in warehouses also improve traffic flow which boosts efficiency. Enabling drivers and pedestrians to see what’s coming serves to optimise the safe flow of warehouse traffic. And convex mirrors are a benefit to warehouse surveillance by making otherwise hard-to-monitor areas visible to supervisors and security personnel.
Compared to other safety and security measures, such as CCTV camera systems, convex mirrors are very low cost, easily installed, low maintenance and long lasting. High quality, robust convex mirrors are designed to be weather resistant making them ideal for both indoor and outdoor applications. They can be easily installed wherever improved visibility is needed.
For more information on Making Warehouse Environments Safe for Workers talk to Insight Security