
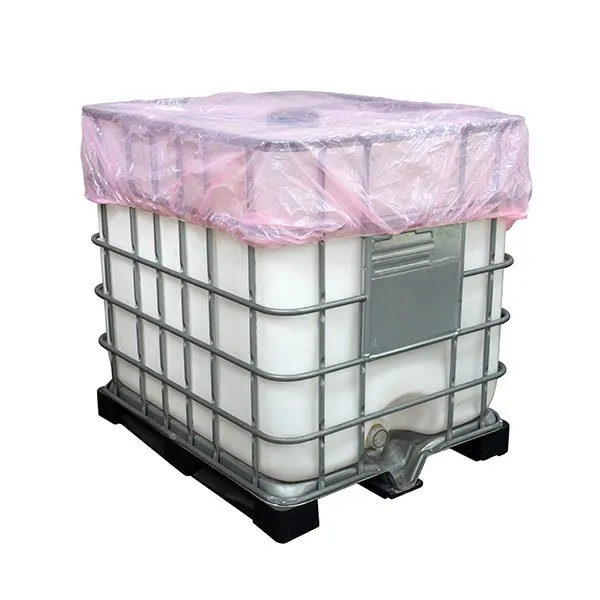
Intermediate Bulk Containers (IBCs) play a critical role in the safe storage and transport of various liquids and bulk materials across industries. However, ensuring the safe and compliant use of IBC containers requires a thorough understanding of the regulations and certifications that govern their manufacture, handling, and application.
At ITP Packaging, we recognise the importance of compliance and aim to help businesses navigate the complexities of regulations, particularly in the UK.
In this guide, we explore key certifications, industry-specific compliance requirements, and the potential penalties for non-compliance, alongside strategies to avoid them.
UK Regulations and Certifications
In the UK, the use of IBC containers is subject to several regulations aimed at ensuring safety and environmental responsibility.
These standards are particularly critical for industries that deal with hazardous materials or food-grade products, as the risks associated with improper handling can be significant.
One of the most important certifications for IBC containers is UN approval. This certification indicates that the container meets the rigorous standards set by the United Nations for the safe transport of dangerous goods.
These standards include tests for impact resistance, leak prevention, and chemical compatibility, ensuring that the container can safely store and transport hazardous substances.
For food-grade IBC containers, additional regulations apply to guarantee the safety of consumable products.
Containers intended for the storage or transport of food and beverages must comply with the standards set by the UK Food Standards Agency (FSA) and relevant European Union regulations, such as EC 1935/2004.
These standards ensure that the materials used in the manufacture of IBCs do not pose a risk of contamination and are safe for direct contact with food products.
Another key regulation relevant to IBC containers is the Carriage of Dangerous Goods and Use of Transportable Pressure Equipment Regulations (CDG). This legislation governs the transportation of hazardous materials by road and aligns with the European Agreement concerning the International Carriage of Dangerous Goods by Road (ADR).
Compliance with these regulations requires appropriate labelling, the use of certified containers, and thorough documentation to accompany shipments.
Failure to adhere to CDG or ADR regulations can result in severe penalties, including fines or legal action.
Additionally, businesses transporting hazardous goods via sea or air must comply with the International Maritime Dangerous Goods (IMDG) Code or the International Civil Aviation Organisation’s (ICAO) Technical Instructions, respectively. These regulations set out requirements for the packaging, labelling, and handling of dangerous goods, ensuring safe transport in different environments.
Industry-Specific Compliance
Compliance requirements for IBC containers can vary significantly depending on the industry and the materials being handled.
For industries dealing with food or beverages, the primary focus is on hygiene and contamination prevention.
Food-grade IBCs are typically manufactured from virgin HDPE (high-density polyethylene) to avoid the risk of chemical leaching or contamination from recycled materials.
These containers must also be fitted with airtight lids and high-quality valves to ensure the safe and hygienic storage of liquid food products.
In contrast, industries handling hazardous materials face a different set of challenges and compliance requirements. These include ensuring that the IBC container is constructed to resist chemical reactions, withstand extreme temperatures, and prevent leaks during transport.
UN-certified containers are a mandatory requirement for hazardous goods, as they undergo extensive testing to ensure their suitability for such applications.
Businesses must also ensure that containers are appropriately labelled with hazard symbols, UN numbers, and any other required markings to indicate the nature of the materials being transported.
The pharmaceutical industry, similarly, has strict requirements for the storage and transport of medical and chemical products.
Containers used in this sector must meet stringent standards for sterility and compatibility with sensitive substances.
Compliance with the Good Manufacturing Practice (GMP) guidelines is often necessary, as is adherence to specific labelling and documentation protocols to ensure traceability and safety.
Penalties for Non-Compliance and How to Avoid Them
Non-compliance with regulations and certifications for IBC containers can result in severe consequences for businesses.
Penalties may include substantial fines, legal action, damage to reputation, and even the suspension of business operations.
Additionally, incidents caused by non-compliance, such as spills, leaks, or contamination, can lead to environmental damage, health risks, and costly clean-up efforts.
One of the most effective ways to avoid non-compliance is to source IBC containers from reputable suppliers like ITP Packaging.
Our containers are manufactured to meet or exceed all relevant UK and international standards, providing peace of mind that your business is operating within the law.
We also offer guidance on selecting the right type of IBC for your specific application, ensuring that the container you choose is appropriate for the materials you are handling.
Regular maintenance and inspection of IBC containers are essential for ensuring ongoing compliance. Over time, containers can develop wear and tear, which may compromise their integrity and render them non-compliant.
Periodic checks should be conducted to identify any signs of damage, such as cracks, leaks, or weakened structures. Valves and seals should also be inspected to ensure they are functioning correctly.
At ITP Packaging, we recommend adhering to a regular inspection schedule and replacing or repairing any damaged components promptly.
Training and education are equally important in maintaining compliance. Employees involved in the handling, storage, or transport of IBC containers should receive proper training to ensure they understand the relevant regulations and best practices. This includes knowing how to properly label containers, complete necessary documentation, and respond to emergencies such as spills or leaks.
Providing ongoing training helps to create a culture of compliance and minimises the risk of errors that could lead to regulatory breaches.
Finally, keeping up to date with regulatory changes is crucial. Laws and standards governing IBC containers are subject to periodic updates, and businesses must stay informed to remain compliant.
Partnering with a trusted supplier like ITP Packaging can help as we monitor regulatory developments and ensure our products and guidance align with the latest requirements.
Contact Us
At ITP Packaging, we are committed to helping businesses navigate these complex requirements.
Our range of high-quality IBC containers meets the most stringent industry standards, providing a reliable and compliant solution for your storage and transport needs.
To learn more about our products and how they can support your operations, visit ITP Packaging, call 0333 987 4565 or email hello@itppackaging.com
For more information on Understanding the Regulations and Certifications for IBC Containers talk to ITP Packaging Ltd