
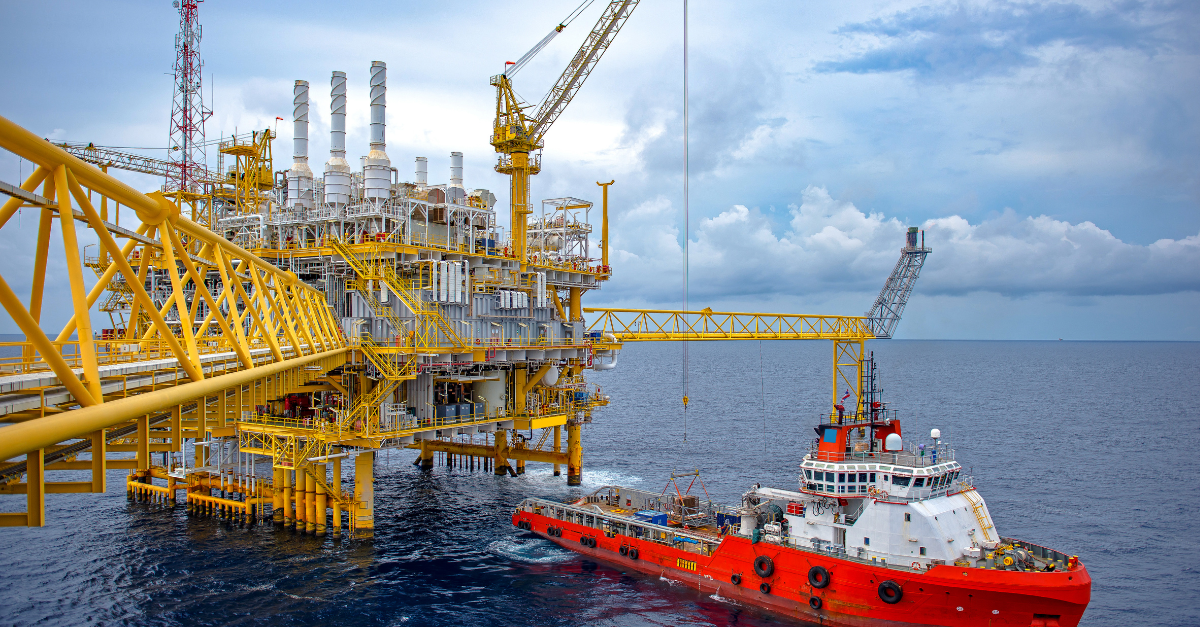
In industries where hazardous materials are handled, processed, or stored, ensuring the safety of electrical installations is paramount. The National Electrical Code (NEC) provides guidelines for these environments through its Article 500, which details the requirements for Class I, Division 2 locations. This blog will delve into what Class I, Division 2 means, its relationship to NEC 500, and the key considerations for equipment design, manufacture, and installation in these hazardous locations.
Overview of NEC Article 500
Article 500 of the NEC is the cornerstone for regulating electrical installations in hazardous locations. It outlines the classification system and sets forth requirements for equipment and wiring in these environments. The primary goals of NEC 500 include:
- Defining hazardous locations based on the presence and characteristics of flammable substances.
- Providing guidelines for the selection, installation, and protection of electrical equipment to prevent ignition of hazardous atmospheres.
- Ensuring safety through established protection techniques like explosion-proof enclosures, intrinsic safety, and purging/pressurisation.
Classification of Hazardous Locations
Class I: Locations with flammable gases, vapours, or liquids.
- Division 1: Hazardous atmospheres exist under normal conditions.
- Division 2: Hazardous atmospheres exist only under abnormal conditions.
Class II: Locations with combustible dusts.
- Division 1: Hazardous dust atmospheres exist under normal conditions.
- Division 2: Hazardous dust atmospheres exist only under abnormal conditions.
Class III: Locations with ignitable fibres or flyings.
- Division 1: Hazardous fibres or flyings exist under normal conditions.
- Division 2: Hazardous fibres or flyings exist only under abnormal conditions.
Material Groups
Groups based on ignition properties:
- Class I: Groups A, B, C, D (e.g., acetylene, hydrogen, ethylene, propane).
- Class II: Groups E, F, G (e.g., metal dust, carbon black, grain dust).
Protection Techniques
NEC 500 includes various protection techniques to ensure safety in hazardous locations:
- Explosion-proof Enclosures: Contain any explosion within the enclosure.
- Intrinsically Safe Designs: Prevent sufficient energy release to cause ignition.
- Purged and Pressurised Systems: Maintain a positive pressure within enclosures to prevent flammable gas entry.
- Non-incendive Equipment: Prevent ignition under normal conditions.
Equipment Installation
The NEC specifies approved wiring methods, sealing requirements, and temperature classifications to ensure safe installations.
Inspection and Maintenance
Regular inspection and maintenance are emphasised to ensure ongoing safety and compliance.
Documentation and Labelling
Proper documentation and labelling are required to identify hazards and safety measures.
Special Considerations
Guidelines are provided for dealing with combined hazards, corrosive environments, and industry-specific requirements.
This framework ensures that electrical installations in hazardous locations are safe, compliant, and well-maintained to prevent fires and explosions.
What is Class I, Division 2?
Class I, Division 2 is a classification used to identify hazardous locations where flammable gases, vapours, or liquids may be present under certain conditions. According to NEC Article 500, Class I refers to environments where these substances are handled, processed, or used. Division 2 specifically indicates locations where:
- An explosive atmosphere is not present during normal operating conditions.
- If an explosive atmosphere does occur, it will only persist for a short period.
- These conditions might arise during repair or maintenance activities, accidental rupture of a container, or failure of a ventilation system.
Class I, Division 2 areas also include zones immediately adjacent to Division 1 locations, where the potential for a hazardous atmosphere is still significant, but less frequent.
Equipment Requirements and Protection Techniques
Electrical and electronic equipment used in Class I, Division 2 locations must meet rigorous standards to ensure safety. NEC 500 and UL121201 highlights several protection techniques, including:
- Non-incendive Equipment: Designed to prevent ignition under normal operating conditions without requiring an explosion-proof enclosure.
- Hermetically Sealed Equipment: Sealed against the entrance of external atmospheres, preventing the escape of ignitable substances.
- Non-sparking Equipment: Operates without generating sparks during normal use.
- Purged and Pressurised Systems: Utilise clean air or inert gas to maintain a positive pressure within the enclosure, preventing the entry of flammable gases.
- Enclosed Break Devices: Contain any arcs or sparks within an enclosure that can withstand the explosion pressure.
- Oil Immersion: Submerges electrical components in oil to prevent the ignition of flammable gases.
Hydrogen Environments in Class 1, Division 2
Hydrogen, classified as a Class I, Group B material, presents unique challenges due to its high flammability and potential for embrittlement of materials. In Class I, Division 2 locations, hydrogen environments require:
- Specific Material Selection: Materials like austenitic stainless steels (304, 316), aluminium alloys (6061), and nickel alloys (Inconel, Monel) are preferred due to their resistance to hydrogen embrittlement and compatibility with hydrogen service.
- Proper Design and Construction: Equipment must be designed to prevent ignition and withstand hydrogen exposure, including non-sparking components and static dissipative properties for non-metallic materials.
- Compliance with Standards: Adherence to NFPA 70, NFPA 55, and other relevant standards is essential for ensuring safety in hydrogen environments.
Key Considerations for Compliance
To ensure compliance with UL121201 for Class I, Division 2 locations, the design, manufacture, and installation of equipment must adhere to several critical considerations:
1. Component Selection: All components must be listed or recognised by NRTL (Nationally Recognised Testing Laboratory)
- Enclosure Requirements: Select UL50E compliant enclosures made of non-combustible, corrosion-resistant materials like stainless steel, aluminium, and reinforced thermoplastics and rated Type 4 or Type 4X for outdoor locations.
- Wiring and Sealing: Proper wiring methods and sealing techniques must be implemented, especially at boundaries between classified and unclassified areas.
- Temperature Ratings: Equipment must have temperature ratings below the auto-ignition temperature of any hazardous substances present.
- Documentation and Labelling: Comprehensive documentation and proper labelling are crucial for installation, operation, and maintenance.
- Regular Maintenance and Inspection: Ongoing maintenance and regular inspections are necessary to ensure continued compliance and safe operation.
Challenges in Global Compliance
While NEC 500 provides a robust framework for hazardous locations in North America, manufacturers face challenges when exporting equipment globally. The primary issues include:
- Incompatibility with International Standards: NEC 500 uses a different classification system compared to ATEX/IECEx standards, leading to certification challenges.
- Multiple Certification Requirements: Manufacturers often need to obtain multiple certifications (NEC 500, NEC 505, and IECEx) to access international markets, increasing costs and complexity.
- Different Protection Techniques: Varying standards between NEC and international regulations necessitate design adaptations for different markets.
Innovations and Emerging Trends
Advancements in technology continue to drive innovations in Class I, Division 2 equipment. Recent trends include:
- Smart Materials and Designs: Utilising advanced materials that offer better resistance to extreme conditions and hydrogen embrittlement.
- IoT and AI Integration: Incorporating real-time monitoring and predictive maintenance to enhance safety and efficiency.
- Energy-efficient Solutions: Developing environmentally friendly and energy-efficient equipment, aligning with sustainability goals.
- Expanded Range of Components: More automation components, including advanced HMIs, PLCs, and VFDs, are now available specifically rated for Class I, Division 2 environments.
Conclusion
Understanding Class I, Division 2 and its relationship to NEC 500 is crucial for ensuring safety in hazardous environments. By adhering to NEC 500 guidelines, selecting appropriate equipment, and considering the latest innovations, industries can mitigate risks and maintain compliance in potentially explosive atmospheres. As technology evolves, staying informed about emerging trends and global standards will be essential for navigating the complexities of hazardous location equipment certification and installation.
For more information on Understanding Class I, Division 2 Hazardous Locations and NEC 500 Compliance talk to JCE Group (UK) Ltd