
Sign In
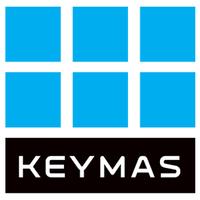
Automated dispatch solutions can be used to improve efficiency, increase accuracy and reduce bottlenecks in a warehouse environment. In this blog post we look at the different types of warehouse dispatch automation available and how they can benefit your warehouse.
Types of automated dispatch systems
There are many types of technology solutions that can help you efficiently dispatch goods from your warehouse, including:
Sorting conveyors that sort packages according to where they need to be delivered.
Automatic palletisers that take products from a conveyor and load them onto pallets ready for delivery.
Counting equipment that automatically counts the number of products to be delivered to a client.
Automatic inline weigh-scales that weigh packages and choose the most cost-efficient courier for delivery.
Barcode scanning solutions that allow employees to scan each package and directly assign it to different vehicles and delivery locations.
Shipping label printers and supporting software that automatically notify couriers when a package needs to be collected.
Each of these solutions has a number of advantages. We have detailed the most important benefits of warehouse dispatch automation technology below.
Save money
Although it represents a high initial investment, dispatch automation has the potential to save money on the day-to-day running of a warehouse, particularly on staffing costs.
Conveyor automation solutions, like sorting machines and automatic palletisers reduce the need for manual handling. Whilst technologies such as label printers and barcode scanners, allow workers to do their jobs faster. The result is a saving against staffing costs. And with recruitment becoming increasingly challenging for warehouses, automation maybe the answer to longer-term resource problems.
Improve accuracy
Accuracy is critical at the dispatch stage of warehouse management. Incorrect orders can lead to dissatisfied customers, poor reviews and potential fines.
Machines that weigh or count products as they travel through the dispatch stages add an automatic check to orders. Similarly, labeling and manifest printing systems can reduce errors by telling employees exactly what should be in each package and/or consignment. And, if things do go wrong, these systems also improve traceability, so errors can be corrected for next time.
Save space
Warehouse dispatching areas can be chaotic. Often dispatch is confined to a small physical space which gets smaller and smaller as boxes and pallets pile up for shipping.
Automation systems are designed to make the most efficient use of the space you have available. They will also speed up the dispatch process, so packages will move through the dispatch area quicker, helping alleviate the clutter. A more organised dispatch area will also help ensure the right boxes go out on the right delivery and lower the risk of orders being misplaced.
Integrate with delivery companies
Effective communication between a dispatch operator and its delivery companies is critical to the success of a supply chain.
More sophisticated shipping label printing solutions can calculate which courier will be the most cost-effective based on a package’s weight or simply based on barcode data. They can also communicate directly with all your couriers, automatically requesting pick-ups and providing delivery details.
Reduce bottlenecks
Warehouses that process a lot of deliveries can be prone to bottlenecks at the dispatch stage, particularly if automation is used up-the-line (which can cope with fluctuations in demand). By introducing automation technology at dispatch too, you can boost efficiency and throughput to eliminate these bottlenecks.
If you’re considering automating your warehouse, don’t forget to include the dispatch process. Your productivity will only be as good as the weakest part of your operation. It won’t matter how fast you can move goods through your warehouse, if they then sit in your dispatch area awaiting delivery, your overall throughput will remain the same.
Two examples of automated dispatch
Individual technology solutions like sorting machines and label printers can work well by themselves, but the individual solutions work best as part of a unified system.
To illustrate how the above solutions can be used together, we have created two real-world examples of how warehouses have implemented automated dispatch in the past.
Example one:
A food manufacturer receives a supermarket order for 10,000 products to be delivered to 20 different stores. As products exit the production line, they travel along a conveyor and barcode technology directs them down the correct lane based on delivery region.
Counting technology counts products as they pass through, so that each store receives its guaranteed quota. Automatic palletisers take products from the sorting bays and load them onto pallets. Each pallet receives an automatically printed label telling staff which truck the pallet needs to be loaded on to.
Example two:
An e-commerce retailer receives hundreds of orders from customers across the UK. At the start of the process, a box is made up with a tracking label informing pickers what needs to be included in each order. Pickers use barcode scanners to pick the items and confirm the order.
After picking, the box travels along a conveyor to dispatch, where an inline weigh-checker rejects or accepts it based on its weight. If rejected, the box goes back to picking. If accepted, the machine prints a shipping label from one of three couriers, according to the weight and the courier’s cost-effectiveness. The system also informs the courier that the box is ready for collection. The box then travels along a conveyor and is sorted according to whether it will be travelling north or south.
For more information on The benefits of automated dispatch systems for warehouses talk to Keymas Ltd
Enquire Now
List your company on FindTheNeedle.