
Sign In
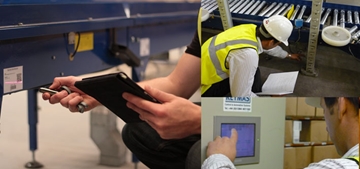
With over 30 years experience in providing materials handling and storage solutions, Keymas are committed to providing industry with a professional and responsive maintenance and support service, that is flexible to meet individual customers needs, whilst providing an ongoing commitment to improve safety, productivity, and return on investment.
The many benefits of scheduled maintenance
If you want to ensure safety and optimum performance from all of your storage and materials handling equipment, maintenance is essential in continuing efficiencies and making early servicing repairs, can often avoid serious and costly breakdowns.
Operating scheduled and recorded maintenance manuals also records the fact that the company is taking reasonable care to prevent accidents and ensure high standards of safety to satisfy Health and Safety and European Directives.
Keymas maintenance and servicing procedure offer many benefits including:-
Prevent costly downtime due to equipment failure.
Maintain reliable and efficient operations.
Reduce operative frustrations and product wastage.
Regular servicing simplifies maintenance operations.
Early diagnosis can prevent key component failure.
Increases the systems life expectancy.
Contracting out can reduce overheads and administration.
A small investment in routine maintenance and servicing reduces the cost of repairs and breakdowns over the life of your system.
Keymas dedicated to Customer Maintenance and Servicing
Keymas has significant first hand experience and a working knowledge gained through designing and installing integrated handling systems with customised controls to ensure track and traceability of production, sortation sequences, through to storage and despatch that makes them fully qualified to maintain and service any system.
Supported by a team of dedicated service engineers, Keymas can offer a one-stop solution to maintenance and servicing, removing the hassle of having to liaise and co-ordinate with multiple suppliers. In partnership with the customer, Keymas has developed bespoke packages that schedule and provide for instant reaction to breakdown and include:-
Preventative Maintenance Programmes – Inspections & Servicing
Site Call Out – Contracted or Emergency Services
Telephone Assistance 24/7
Electrical & Mechanical Services
Racking Inspection & Repairs
Repairs, Overhaul & Upgrade
Retrofit Replacement Equipment
Relocation of Equipment
Software Support & Upgrades
Total Facility Management
Consultancy – to identify cost savings and improve operational efficiencies
Any damaged equipment can be spotted and reported before equipment failure or accident. In maintaining equipment recommendations on repair work will be registered and quoted for prior to rectification. Partnered with many key suppliers, this allows Keymas to quickly access parts to service and maintenance all types of equipment and operating systems such as:-
Conveying Systems – Case, Carton, Tote, Pallet, Sortation, Elevator, Hanging Garments, etc
AGV Systems – Automated Guided Vehicles, Towline-in-floor Chain Conveyors, etc
Warehouse Equipment – Shelving, Static /Live Carton & Pallet Racking, Vertical Carousels, Mezzanine floors
IT Systems – WMS systems, PLC/PC Controls, Bar Coding, Data Management, RF Picking & Tracking Systems, Report Generation Comprehensive Maintenance & Safety Analysis
At Keymas, our highly-trained technicians will work with your personnel to provide a low-cost maintenance review on your system to develop a comprehensive service maintenance program unique to your application and needs.
Maintenance and servicing creates a safe working environment by ensuring your system is operating safely, whilst providing for the optimum production efficiency and virtually eliminating downtime on a day-to-day basis to produce measurable return on investment over the life of your equipment.
For more information on Conveyor System Maintenance talk to Keymas Ltd
Enquire Now
List your company on FindTheNeedle.