
Sign In
Preparing for the Future
31-01-2019
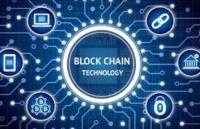
Manufacturing Industry Trends for 2019
As we’ve discussed previously, the manufacturing industry is undergoing what many have deemed the fourth industrial revolution, or Industry 4.0. A revolution characterized by the adoption and application of the Internet of Things (IoT), Artificial Intelligence (AI), and Additive Manufacturing (3D Printing). However, Industry 4.0 is not the only variable to prepare for as we embark on a new year. Technological advances will be progressing across the board with the potential to drastically affect the industry. So, for your reading pleasure (and our own personal curiosity), we’ve rounded up the most significant trends to hit the manufacturing industry this year.
Cybersecurity and 5G Networks: As the manufacturing industry relies more heavily on the Internet of Things and real-time data collection, the need for more bandwidth and a more reliable network will also increase. Although large corporations often install Industrial Ethernet Systems, these require a significant investment and aren’t entirely practical for truly connected manufacturing. Wireless 5G networks on the other hand, provide the bandwidth necessary to support all that comes with Industry 4.0. Unfortunately, relying more heavily on wireless connectivity and cloud technology also puts UK companies at increased risk for cyberattacks. In 2018, nearly half of all UK businesses faced some sort of cyberattack, demonstrating just how vulnerable we all are. As such, 2019 will undoubtedly see an influx of CISOs (Chief Information Security Officer) to ensure sensitive data remains protected and secure.
Digital Twins: A digital twin is a digital simulation of an existing operating system. The digital twin is able to change nearly instantaneously with its physical counterpart with the help of artificial intelligence, machine learning, and software analytics. They are most commonly used to predict how complex machinery will respond to varying scenarios. For example, Rolls-Royce is using digital twins to study how jet engines respond to in-flight complications, such as losing a blade. The aim of their research is to create a safer jet engine capable of operating under the most extreme of circumstances. A feat which couldn’t be tested without putting human lives at risk prior to the adoption of this technology.
Blockchain & Supply Chain Management: Blockchain provides a way of record keeping that can be verified across servers. Each record or ‘block’ is validated by a community through a distributed network of computers with previous data entries in the chain. The key here is the distributed network that certifies and logs everything that has happened in the chain. This prevents any single entity from going back and altering pre-existing data, which creates a layer of security that is not available with centralized databases of information.
To date, blockchain has been popularized for its applications in the financial sector, however its applications reach far beyond that. Blockchain has the ability to improve one of the manufacturing industry’s biggest headaches; supply chain management. More often than not, manually tracking a product’s journey can take a couple of days as suppliers, manufacturers, distributors, and retailers are all contacted to find a lost or damaged product. This can be completed in mere seconds utilizing blockchain technology, as each point of contact is logged in the system. This type of transparency and convenience would be invaluable to supply chain management and will likely be a top trend this year and for years to come.
Servitization of Manufacturing: While it may sound odd that the product-centric manufacturing industry could shift to a service-based one, it’s becoming a reality due in large part to the popularity of on-demand services such as Uber. In this model, businesses would make use of a shared network of manufacturing infrastructure to produce goods including everything from machines, to maintenance and software. Customers would request a part by providing design files and specifications and based on location, workloads, scale, and available materials, the network would route the order to the facility that would most efficiently fulfill the order. Although this model presents a cost-effective solution for those utilizing it, the manufacturing industry will undoubtedly struggle to provide the high degree of flexibility required to execute such a model.
Although the engineering industry can be slow to adopt change, Industry 4.0 will continue to propel the industry forward. So, while these trends may not cause monumental changes this year, the evolution is inevitable, which is why it’s always best to be prepared.
For more information on Preparing for the Future talk to KTR U.K. Ltd
Enquire Now
List your company on FindTheNeedle.