
Sign In
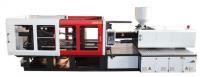
Injection moulding is one of the prime processes for producing plastic products due to the speed of the process and the ability to produce large numbers of identical products, anything from high precision engineering components to disposable consumer goods.
Typically, thermoplastics are used in the process, and materials such as Nylon PA, Polycarbonate PC, PP and GPPS are most commonly used. Plastics are increasingly being used instead of conventional materials because of their high durability properties, but this is not a new concept, as it came into existence in 1872.
Virtually all manufacturers use injection-moulded parts, for instance bumpers and wheelie bins, due to the flexibility in size and shape which makes it possible to extend the boundaries of plastic design. This enables traditional materials to be replaced with a cheaper and lightweight alternative. Here are a few examples of products that use injection moulding:
Telephone handsets
Automotive dashboards
Syringes
Disposable razors
Bottle lids
Injection moulding can even be considered revolutionary as recycled materials have been introduced into the process. The material is fed via a hopper into a heated barrel containing a reciprocating screw. The screw acts as a ram in the injection phase, but also provides additional heat from the shearing action. Driven by a hydraulic motor, the screw feeds the molten polymer into a temperature controlled split mould. The polymer is injected into a mould at high pressure, which defines the shape of the finished product.
Tools are more often manufactured from steels and aluminium alloys for increased cutting and polishing speeds, but the costs associated with tool manufacture mean that alternative methods of production need to be considered. Here is where injection moulding becomes the favoured process for its speed and high volume turn over.
For more information on Role of Recycled Materials in Injection Moulding talk to KTR U.K. Ltd
Enquire Now
List your company on FindTheNeedle.