
Sign In
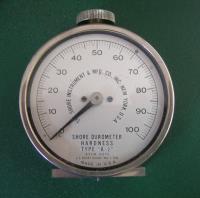
What is a Durometer?
A durometer is an instrument used to measure the hardness of a material, and this is defined on the basis of the materials resistance to permanent indentation. A ball or diamond pyramid is pressed into the material at various pressures, however this technique proved inaccurate for softer materials such as elastomers. As the indentation was measured in-situ, the indentation would remain on the surface of metals but not the softer materials.
A Shore Durometer
History of Shore Durometer
Albert F. Shore was born in 1876 and founded the Shore Instrument Co. Inc, and during his lifetime produced the first quadrant type durometer in 1915 at the company base in New York City. The durometer and its scaling structure were developed in the 1920s by Shore to measure the hardness of polymers, elastomers and rubbers.
Shore also developed another instrument designed to test load indentation prior to the durometer. Known as the Scleroscope, this method involved dropping a hammer down a tube onto the chosen material and recording the rebound height of the fallen hammer.
Shore died in 1936, and it was his son Fred who continued to develop the durometer - producing a round style durometer in 1941. Over the years, the company has had several owners, but in 1995 they were taken over by The Instron Corporation.
Further Developments to the Shore Durometer
Even though Shore is still credited as the originator of the durometer, over the years others have developed the instrument further.
Germany
Heinrich Bareiss founded Bareiss Prüfgerätebau GmbH, a significant manufacturer of testing equipment in 1954. They should be attributed to the introduction of the first round style durometer to test material hardness. It was simpler to use and increased the resolution from 5degrees Shore to 1 degree Shore.
The Bareiss Durometer was noted for its precision and for meeting the American Society for Testing and Materials (ASTM) test method.
Japan
In 1956, founder Mr Akashi set up Kobunshi Keiki Seisakusho. The company later changed its name in 1972 to Kobunshi Keiki Co. Ltd. Their range of durometers met the Japanese standards as well as the ASTM test methods.
Durometer Contemporaries
When these types of instruments were first developed, non-metallic hardness testers were generally used for rubber. Many of the early inventions varied greatly as the preferences of individual manufacturers and national distinctions meant that requirements differed. However many of these instruments became extinct or went on to be developed into the instruments we see today.
The reason that the durometer survived when others failed is that it was adaptable and evolved to keep up with new materials as they appeared on the market, such as plastics, polyurethanes and sponge rubber.
Evolution of the Shore Durometer Scale
How the Shore scales evolved is unknown. Rubber testing was originally known as durometer hardness until an instrument was needed to measure harder rubbers. Albert Shore set up a strange scaling system for the durometer to measure the hardness of materials. The first scale was "A", but when harder materials needed to be tested a stronger spring was used and the scale then became "B", then "C" and so on. The "D" scale was created to test new harder plastics as they came onto the market, but it wasn't until the 70s and 80s that the need for a scale softer than A was needed. To overcome this problem, a scale "A" spring was used with a spherical indenter.
How does the test work?
The test requires the same amount of force to be applied as a constant but without shock measuring the hardness. The Shore hardness or durometer hardness test measures the hardness value by penetrating the material with the durometer indenter.
In terms of results, they are a useful measure of resistance to indentation of various grades of polymers. However, the Shore hardness test does not show other properties other than the hardness. For example, the durometer does not determine strength, resistance to scratches or abrasions so this instrument should not be used solely for product design specifications. At times, the test is used to measure flexibility for elastomers particularly with a series of grades from the same product line.
Rubbers and plastics have resilience so over time the indentation may decrease. To avoid this the test duration should be reported with the hardness number e.g. 3 seconds. Another control procedure that must be adhered to is recording the temperature as this can affect the results, as the colder the material the harder it becomes.
ISO Make Changes
The International Standards Organisation issued a revised version of ISO 7619 at the beginning of the new millennium. For 90 years the extension of the durometer was set to 0.100inch worldwide, and each 100th increment was equal to 1-degree shore.
When the revised ISO was issued, imperial measurements were eliminated to make way for the metric system. The indenter extension was re-set to 2.5mm, but this is not the equivalent to 0.100inch, it is actually 0.098inch.
Due to the ‘mix-up', many durometers didn't meet the new test method standards, particularly the instruments with conventional dial gauge indicators. The new metric instruments were also sold at a higher value to their predecessors due to their metric based movements.
How is the Shore Durometer used for KTR Couplings products?
At KTR we use the shore durometer method to test the hardness of our products. This is particularly the case for the spiders for our ROTEX couplings. As jaw couplings are used in various situations, it is important to know the specific torque requirements involved in order to ensure the correct material hardness of the spider chosen meets the specific requirements of the application.
For more information on The History of Shore Durometer Hardness & KTR’s Elements for ROTEX Couplings talk to KTR U.K. Ltd
Enquire Now
List your company on FindTheNeedle.