
Sign In
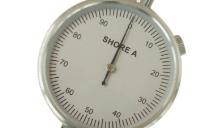
Selecting flexible coupling insert with the correct shore hardness are key to performance and dealing with vibration and misalignment will in your drive systems.
Machinery shutdowns are often caused by damage from balancing and/or vibration problems stemming from misaligned components. Not only are shutdowns due to misalignment inconvenient, but they are also costly and have the potential to be dangerous as well. Fortunately, utilising elastomeric couplings offsets the damage of misaligned drive systems, preventing costly and inconvenient shutdowns. One of the most popular elastomeric designs in use is the jaw-type coupling, which consists of two metallic hubs, often positioned on the ends of drive and driven shafts, and a spider element (also known as an elastomer insert) fitted securely between them. These spider elements are typically made out of a plastic or rubber material which helps with electrical isolation, vibrational dampening, and misalignment.
There is no single spider element that will be appropriate for every function. Instead, they are available in varying levels of hardness, which are all suited for different functions. As jaw couplings are used in a number of different situations, it is critical to know the exact torque requirements involved in order to ensure that the material hardness of the spider chosen meets the specific requirements of the application. Fortunately, spider hardness is typically standardised at various levels and organised by manufacturer specific colours, but how exactly do we, as the manufacturers, ensure each spider is the correct hardness?
Measuring Shore Hardness
In order to determine the hardness of a spider element (known as Shore Hardness), we use the durometer scale. The durometer scale is named after the instrument itself which determines the hardness of materials by measuring their resistance to permanent indentation. Originally, a ball or diamond pyramid was utilised to press into the substance at varying pressures. However, this method was found to be ineffective for measuring the hardness of softer materials and a more effective, spherical instrument (still referred to as a durometer) was introduced in 1941.
The durometer is pressed into the sample substance with strong, consistent force in order to obtain the most accurate result. However, it’s worth noting that regardless of the accuracy of measurement, the result may still change over time. This is due to the resilience of rubbers and plastics and their response to varying temperatures (i.e.: colder temperatures will produce harder results). Therefore, the hardness number should be recorded along with the test duration, and temperature.
Why Shore Hardness Matters for Spider Jaw-Type Couplings
Shore Hardness is one of the main factors involved in fine-tuning jaw-type couplings to their specific applications. Quite often the performance of the While there are a number of scales in use, the Shore A and Shore D scale are most commonly used to measure rubbers and elastomers. As seen in the diagram below, the Shore A scale is used for more flexible elements composed of soft rubbers and plastics, while the Shore D scale is used to measure harder, more rigid ones.
For more information on The importance of Shore Hardness for couplings talk to KTR U.K. Ltd
Enquire Now
List your company on FindTheNeedle.