
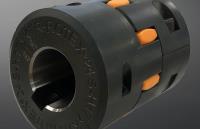
Our couplings are used all over the world and in all types of environments. More often than not, these environments are harsh and without proper preparation can wreak havoc on mechanical equipment. Whether it’s corrosion from strong chemicals or contact with salt water, our couplings must withstand the elements. While steel and cast-iron are fundamentally tough materials, a chemical coating or pre-treatment is often needed for added protection. Although different metals and applications require different pre-treatments to function optimally, one of the most common treatments we use is phosphate coating. So today, we’re going to briefly dig into the science behind phosphate coating and explain why we use it, here at KTR. What is Phosphate Coating? Phosphate coating is a conversion coating that involves the application of phosphoric acid and phosphate salts. The application can be applied in a spray or by submerging the component in the solution. Once applied, the chemicals react with the surface of the coupling in a way that forms a thin layer of insoluble, crystalline phosphates. The thin coating provides several functional benefits without affecting the surface of the component to which it is applied. What is the Purpose of Applying Phosphate Coating? Phosphate Coating performs three main roles when applied as a pre-treatment. Corrosion Prevention: The layer of crystalline phosphates that form during the phosphate coating process produces an electrically non-conducting surface. This inhibits electron transfer, which in turn prevents the formation of metal oxide (rust). The coating also separates anodic and cathodic components, which further protects against underfilm (also known as filiform) corrosion. Lubricant Layer: Phosphate coating can also serve as a lubricating base layer when used on working mechanical parts. Adhesion Primer: When used as a pre-treatment, phosphate coasting is also an ideal primer that can help with the adhesion of additional coating layers. Why Do We Use Phosphate Coating at KTR? We use phosphate coating for the three main reasons listed above. It’s strong adhesion and corrosion protection are particularly useful when applied to steel parts as the iron is needed for the crystalline phosphate coating to form. Depending upon the application, phosphate coating is also followed by other coatings such as an oil coating that further protects against rusting and galling (a form of adhesive wear caused by the transference of material between metallic sliding surfaces). When compared to other applications, phosphate coating is also relatively cheap and does not need to be reapplied, which makes it a very economical solution. However, it’s important to keep in mind that the application of phosphate coating will increase delivery time by two to three weeks as we have our vendors apply it abroad. Here at KTR, we are continuously exploring new solutions that will help our clients achieve long-lasting, optimal system operation. If you have questions about whether phosphate coating would improve the lifespan of your system, give us a ring – we’d be happy to help.
For more information on What is Phosphate Coating and Why Do We Use It? talk to KTR U.K. Ltd