
Sign In
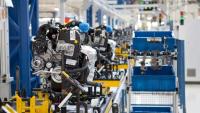
Industrial robots have been used in car factories around the world for decades, but those in use today are more advanced than ever. It is estimated that in the UK alone, the annual turnover of the automotive industry is over ?50 billion, and in 2018 the number of new vehicle registrations was 2,367,147. So, it makes sense that car manufacturers have turned to robotics to help speed up production processes.
Robots are an absolute necessity for car production companies in order to keep up with competitors due to extremely high demand, the complex nature of the product, and a lengthy assembly process. There is a range of practical applications for automotive robotics, and each application is responsible for making a specific process more accurate and efficient.
Practical applications of automotive robotics
Each application of robotics within the automotive industry is designed to either increase productivity, cut down on waste materials, reduce safety risks, or improve quality standards. There is a multitude of ways in which robots can be used in the car manufacturing process, and we?ve outlined some of the main ones below.
Initial manufacturing stage
Welding
Robots are an excellent tool for automating welding processes in car production, as robots can both perform the actual welding whilst handling the relevant parts. Common uses include arc welding and resistance spot welding, with arc welding accounting for roughly 20% of all industrial robotic applications. Robot welding is a staple application of automotive robotics due to its ability to increase throughput, accuracy, and repeatability, whilst making the production process safer and more efficient.
Assembly
Repetitive but important tasks such as wheel mounting, screwdriving, and windscreen installation can be carried out at speed with highly accurate automotive robots. Robotics also improves the reliability of the assembly line, as the production cycle can run round the clock and the production schedule is also consistent each day.
Handling and part transfer
The handling of car parts is often one of the most dangerous parts of a production line for human employees, due to external risk factors such as molten metal, sharp edges or trip hazards. Risks can also include repetitive strain injuries, or back problems due to lifting significant weight or lifting at awkward angles.
Robots are the perfect solution, as they can be exposed to these hazards with relatively little risk to the machinery itself. This both speeds up the handling process, as well as reducing accident rates and injury claims by removing the need for humans to be present in dangerous environments.
Robotic hands
Robotic hands and exoskeletons are being trialled by some car companies around the world to give their human employees a helping hand when it comes to manual work. For example, tasks such as lifting, drilling, and other overhead work can quickly cause fatigue and lead to a slip in standards.
Robotic hands and exoskeletons are designed to be worn by human employees and can provide extra strength and lift assistance to take the weight off human muscles. Some exoskeletons have been described as ?cancelling out the effect of gravity? to reduce muscle strain and fatigue for workers on the assembly line.
Finishes and quality checks
Robotic painting
Another application for robotics which has been around in the automotive industry for decades is robotic painting. Early versions of paint robots tended to be hydraulic variants and these may still be used today, though with lower quality results and more safety risk. Newer variants are electronic, highly accurate, and produce a much more consistent coating to exact requirements. Many car factories use paint robots to apply paint across the entire exterior of cars, and some can even be used to paint the internal furnishings of the vehicle.
Robotic vision
Robotic vision was developed back in the 1980s with the aim of creating a programmable robot which could ?see?. The robot works using an algorithm and a camera which aims to match pictures of parts that the robot will interact with. If the algorithm cannot match the picture, the part is not accepted and the robot will not carry out any work on it. Robotic vision is highly valued in the automotive industry as it allows individual car parts to be fitted together with exact precision to create a higher quality product.
Quality control
Robotic vision often referred to as ?machine vision? is also a key tool for quality control, or vision checking, as it can flag finished products which do not meet certain standards or a specification for review, preventing sub-par products from reaching the point of sale. This can include colour analysis, blob detection, pattern recognition, edge detection, and much more.
Overall, the nature of the fast-advancing automotive industry makes it an excellent playground for new robotic developments and innovations, and we are sure to see even more advanced robotic applications emerging across the industry over the coming years.
For more information on Robotic Applications In The Automotive Industry talk to L-A-C Logistics Automation
Enquire Now
List your company on FindTheNeedle.