
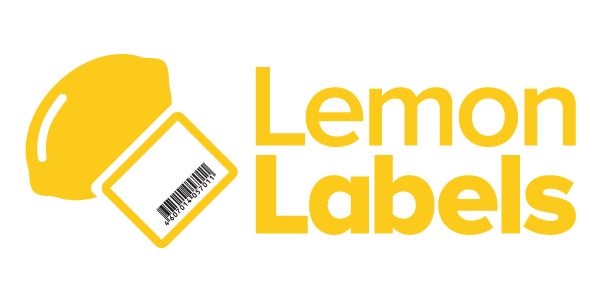
Reducing Label Waste – The Thin Liner Solution
At Lemon Labels, we are constantly striving to ensure that we are taking every possible step to reduce our environmental impact; in 2021 we moved our production into a new A+ energy-rated factory to reduce energy waste, we followed up with electric vehicles for our sales team, we have installed non-hazardous ink cleaning stations, and have been using recyclable packaging for many years.
We have been watching the developments in the linerless labels space with interest, but whilst in certain circumstances linerless labels offer a great solution, there any many situations where linerless labels are not suitable, not least of all because of incompatibility with legacy printer hardware.
So it was with great enthusiasm that we invited label industry experts John Hill UK Technical Manager, Chelsea Packman Area Sales Manager from Herma Materials, Ralph Lynch, Sales Manager from RotoMetrics and Mark Laurence Sales Manager from Daco Solutions, to visit us for an event earlier in the year to discuss Herma’s new thin liner label material, it’s benefits for the end user and the practicalities of working with the materials as a label manufacturer.
Recycling Label Liner Challenges
The challenge with label liner material is that there is a lack of suitable recycling options currently in the UK due to the silicone coating on the liner material, making it unsuitable for traditional paper product recycling routes. This new product from Herma doesn’t remove the liner from the supply chain but instead reduces the thickness of the liner, allowing the labels to continue to be used in existing end-user installations without any need to make alterations to the end users printers or settings, yet by reducing the thickness it reduces the volume of label liner material for the end user to dispose of.
Thin Label Liner Solution
In essence, the Herma solution sounds really simple, without making any changes to the actual label (the face material and adhesive are exactly the same); if we can’t altogether remove the liner material, let us reduce the quantity of it, the material on test was Herma’s HERMAtherm G BPA Free label paper on a permanent acrylic based adhesive on Herma’s honey supercalendered glassine liner (907/62dps/543), this material is offered as an alternative to the standard thermal eco papers widely used for logistics and shipping labelling.
For comparison, the new 543 “thin” liner comes in at approx. 45g/m2 grammage compared to Herma’s traditional “standard” 515 liner that has approx. 56g/m2. A reduction of 11g/m2 or nearly 20%. To place this in to context, it’s estimated that Amazon delivered approximately 15% of the estimated 5.4bn packages delivered in the UK in 2021. These packages would each likely have one address label per package. If Amazon alone adopted this thin liner technology, this would result in a reduction of label liner waste of approx. 140,000 tonnes per year, and if every parcel in the UK was delivered using a thin liner label, the liner waste would be reduced by nearly 1 million tonnes per year. To visualise this, 1 million tonnes is the equivalent of 150,000 elephants or 8,000 Boeing Dreamliner aircraft!
Our team were keen to hear from John and Chelsea about the research and development that Herma has undertaken to develop this new material with a clear drive to reduce waste but also have to overcome the technical challenges both in their manufacturing process and also considering the challenges other stakeholders may face working with the new materials.
Technical Considerations
From a technical point of view, changes in label material thickness can cause real issues when converting the jumbo roll materials into finished label rolls for end-user use due to the effects this can have on the die-cut tooling that is produced to cut out the label shapes from the jumbo roll. Before our meeting, Ralph and the team at RotoMetrics had worked with samples of the material from Herma to develop some new tooling designed specifically to suit the properties of this material.
Lemon Labels have long considered Daco Solutions as our partner in developing our label business. Mark was able to advise us of the challenges that can be faced when using different thickness liners on the press. We talked in conjunction with Ralph about the work being done to perfect adjustable anvil systems and to continually develop label-converting equipment to keep up with advances in label materials. One concern was that the thinner liners might not provide suitable strength for the tension exerted on the roll materials when die-cut at speed, a must for a high-paced manufacturing environment. It was impressive that with good tooling and excellent auto tension control from the Daco PLD machine, we could still perforate the liner of the 4 x 6” labels commonly used by most couriers and carriers in the UK.
The Results
I’m pleased to report that the material and the tooling developed by RotoMetrics worked perfectly together. We were able to die-cut the new thin liner material at 150m/minute with no loss of performance compared to our standard materials, meaning that this development will be commercially viable to introduce with little effect on the operational efficiency of a busy label-making business!
Some other key benefits of the thin liner material are;
- It reduced label liner waste.
- The label and adhesive don’t change, so the end user won’t notice any difference.
- The labels can be used in any existing thermal label printer without needing any new printers.
- The new rolls produced on the thin liner material have a smaller roll diameter due to the material thickness. Therefore we can maintain the roll diameter and add up to 20% more labels on a roll, meaning more labels per box, less packaging, less transport costs and a lower carbon footprint per delivered label.
- Increased labels per roll mean fewer roll changes for the end user, which will improve end-user operational efficiency.
Finally, I’d like to thank all of the attendees for their time, knowledge and good humour on the day; we had a blast. It was great to work with you all.
How Can We Help Reduce Your Label Waste?
If you are a label buyer and would like to learn more about how Lemon Labels can help you reduce your label liner waste, assist you in meeting your ISO 14001 targets or with any other labelling issue you may have, please get in touch with our team of friendly label specialists to arrange a chat or a visit.
Check out our most common size of thin liner labels here.
Our team is here to help with your label requirements on 01892 300737.
For more information on Lemon Labels Reducing Label Liner Waste With New Thin Liner Technology talk to Lemon Labels