
Sign In
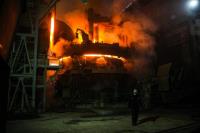
Pore size measurements must be conducted on the raw materials for powder metallurgy processes, to ensure that end-products yield desirable mechanical properties. The strength, weight, hardness, and permeability of metal alloys produced from powder minerals depends upon the porosity of the raw constituents.
Powder Metallurgy and the Importance of Pore Size Measurements
Powder metallurgy refers to a family of innovative production technologies that deviate from the established metallurgical processes of forging high-performance alloys. Conventional forging involves mixing the molten minerals and forming alloys into billets or ingots for further processing. This technique has been used for centuries, but powder metallurgy is more closely linked to ceramics sintering than blacksmithing.
In a typical powder metallurgy process, raw mineral powders are mixed with lubricating or binding agents before densification in a rigid housing. Compacting the raw materials is critical for achieving the required thermodynamic characteristics of the end-product. Ceramics manufacturers aim to achieve fully-densified materials from the sintering process, but metals are more often pressed using what is known as the sponge iron process. This technique aims to retain the internal porous structures of compacted particles to achieve high-strength at reduced density.
Pore size measurements are carried out on direct reduced iron (DRI) powders, which are produced by crushing iron oxides with additive minerals. These feedstocks typically feature broad particle size distributions and extremely irregular shapes. They are also highly porous in nature ? as the name ?sponge iron? suggests. The high open porosity of DRI offers easy compaction and good green strength, translating to higher ultimate tensile strengths at lower densities.
DRI can be subjected to pore size measurements using the principle of capillary flow porometry. This describes the method of introducing a non-wetting liquid into the porous structures of a sample before displacing that liquid with an inert gas. The pressure required to remove liquid from a pore is inversely proportional to the diameter of its throat. This parameter can be used to calculate pore size as a function of liquid surface tension, the contact angle of the liquid, and the differential gas pressure. Yet this assumes that pores are roughly cylindrical.
Pore distribution, size frequency, and density are three additional parameters that must be considered for fully-rounded pore size measurements. These are useful for characterizing DRIs and other powdered metals with respect to their density and porous properties.
Pore Size Measurements with Meritics
Meritics is the UK?s leading supplier of analytical instruments equipped to perform pore size measurements of metal powders and metallurgical raw materials. The iPore Capillary Flow Porometer is an advanced series of capillary flow instruments suitable for measuring the porous structures of DRI powders across a potential size range of 0.013 ? 500 micrometres (?m). These instruments are applicable with any nonwetting liquid and operate up to a maximum pressure of 500psi.
These measurements are beneficial for R&D or quality control (QC) of powder metallurgy processes. If you would like any more information about our pore size measurements capabilities, please contact us directly. We are happy to answer any questions.
For more information on Pore Size Measurements for Powder Metallurgy Raw Materials talk to Meritics Ltd
Enquire Now
List your company on FindTheNeedle.