
Sign In
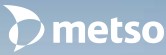
Final elements, such as ESD valves, are a critical part in the safety lifecycle. When they are not working properly, the safety of the entire plant is in jeopardy. To ensure overall plant safety, correct ESD valve selection plays a vital role. A lot of uncertainty prevails around the relatively new standards IEC 61508 and IEC 61511 and how they should be interpreted for safety valves. This blog post looks closer at this issue and sheds some light on what is an essential but confusing subject.
This topic was discussed in my Valve World Conference presentation About correct valve selection for ESD - Metso expert at Valve World Conference
In recent years, we’ve seen an increase in discussion about the probability of failure on demand (PFD), safety integrity levels (SIL) and optimal Lambda values. Indeed, these functional safety calculations are a valuable way to maintain overall safety. But these calculations are only valid if the valve itself has been correctly selected. If systematic errors exist in the valve selection, then it is not possible to gain any advantage from the PDF calculations. And although certification has become the industry standard, verification of the valve’s safety integrity or valve assembly extends beyond SIL certification, SIL levels or good PFD values.
We believe these are the necessary steps to correctly select a valve and ensure that the final elements are capable of performing reliably in emergency situations.
Step one – define the application
Our years of experience in the field have repeatedly proven that only application-based valve selection guarantees a valve will work as intended in case of emergency. Correct ESD valve selection goes hand in hand with a range of application challenges that should be properly considered at the start, including pressure class, temperature and materials.
If the selection does not match the application in question, valve failures do occur.
Step two – complete calculations
Once the valve is capable of working in the designated application, you can then proceed to the functional safety calculations. But before you jump into your calculations, note that the certification is only a document to prove that the valve as a component is capable of working in a certain SIL loop. It does not guarantee that the whole assembly is SIL approved.
To know the final safety system’s capability, the complete assembly must be calculated, taking into account SIL certifications and PFD values for all components, such as the valve body, actuator or intelligent safety solenoid.
Step three – install and test
ESD valves are not so-called “install and forget” devices. The only way to maintain their safety integrity is to perform systematic valve testing. This is done with a partial stroke test (PST) without stopping the plant’s operations and with a more comprehensive proof test that takes place during shutdowns.
In summary, the key of successfully operating an ESD valve starts from the very basics of valve selection. Only after making the correct valve selection can we look at SIL and PFD calculations. Even then, the valve’s lifecycle and regular valve testing cannot be neglected if you want to ensure that the ESD valve will work in any emergency situation.
For more information on Blog: 3 steps to ensure ESD valve reliability beyond certification talk to Metso UK Ltd
Enquire Now
More News
List your company on FindTheNeedle.