
Sign In
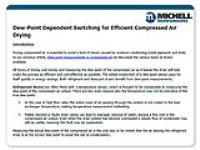
Introduction
Drying compressed air is essential to avoid a host of issues caused by moisture condensing inside pipework and tools. In our previous article, Dew - point measurements in compressed air we discussed the various types of dryers available.
All forms of drying cost money and measuring the dew point of the compressed air as it leaves the dryer will help make the process as efficient and cost-effective as possible. The added investment of a dew-point sensor pays for itself quickly in energy savings. Both refrigerant and desiccant dryers benefit from dew-point measurements.
Refrigerant dryers are often fitted with a temperature sensor, which is thought to be comparable to measuring the dew point of the compressed air output. There are two main reasons why the temperature may not be indicative of the true dew point:
• In the case of high flow rates, the entire mass of air passing through the system is not cooled to the heat exchanger temperature, making temperature measurement misleading.
• Failed, blocked or faulty drain valves can lead to improper removal of water, leaving a fine mist in the compressed air output. Even when the drain system has become overloaded a steady flow of condensate may still be visible, meaning this fault may be overlooked.
Measuring the actual dew-point of the compressed air is the only way to be certain that the air leaving the refrigerant dryer is at the correct dew-point to avoid the risk of condensation.
Desiccant dryers are more efficient that refrigerant dryers, but many rely on pre-set cycle timers to determine when to switch from the active to the inactive columns. Relying on a timer means that energy can be wasted as the columns switch before the desiccant has absorbed the maximum amount of moisture.
Using a dew-point sensor to determine the dew point of the active, drying column increases efficiency by only switching when it is necessary to do so. With dew-point dependent systems (DDS) the regeneration of the inactive column is still based on time, but once the pre-determined regeneration time has elapsed, purge air is switched off completely (as are the heaters in heat regenerative dryers). When demand is low, the active, drying, column is in operation for much longer, resulting in a large saving in purge air and heating costs.
For more information on Dew-Point Dependent Switching for Efficient Compressed Air Drying talk to Michell Instruments Ltd (A PST Brand)
Enquire Now
List your company on FindTheNeedle.