
Sign In
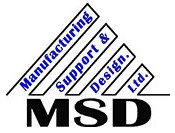
When you operate a business that uses tubes that are filled with different products and dispensed to sellers, you need to have checks in place to ensure quality at all stages. One of the key elements of this is the use of Tube testing machines which ensure that the seal integrity of the empty or filled tubes is to the required standard.
What is tube testing?
Tube testing is a high-quality process that allows for the testing of sealed tubes that are small in size and to ensure they are sealed in a consistent way. The testing machine can be located on the factory floor, so it becomes an integral part of the quality control process and can be used by operators, setters and the QC department.
By using a tube testing process, you have a definable and repeatable process in place that can test tubes that are filled and sealed. It is a far better system than the traditional compression cylinders that are used to pinch the tube. Instead, it checks the tube with a stress test and the internal seal is checked for flaws or weaknesses. It also offers a consistent way to check large or small tubes as well as empty ones.
How it works
The process of using a tube testing machine is a relatively simple one. The tube is put into the machine via a hinged door at the front of the machine. The tube is screwed onto a threaded mandrel that is chosen depending on the size of the tube. The door is then closed, and the machine is ready to run the test.
Once the start button is pressed, the test cycle inflates the tube without a shock process and puts a set amount of pressure on it for a set time. These values can be set before the test, although machines come with a standard setting that you can use if you don’t know what to choose.
You can monitor the pressure achieved by the pressure gauge on the machine but also means that the machine doesn’t need hands-on monitoring to complete its process. You can also stop the process at any point manually.
Sealing options
Once you are confident that the tubes you are using meet the right standards and are as strong as you need, you can then set about using them and sealing them. There are various options for sealing and once they are sealed, the tube testing machine can then check the seal as well.
Choosing the right sealing option depends on the kind of tube and products that you are packaging. For example, plastic seals work well with polyethylene tubes that have a single layer. But they don’t work as well with tubes that have a multi-layer design. Currently, hot air plastic tube sealers and ultrasonic plastic tube sealers are the two top options on the market.
Hot air tube sealing is most often seen in manufacturing. Hot air passes into the open end of the tube, making the plastic softer. Sealing jaws then grip the end of the tube, clamping it shut. Ultrasonic tube sealers are better for small volume systems or where hot air sealing doesn’t work. It uses an ultrasonic sealing horn to soften the plastic and allow it to be clamped.
Get the right equipment
MSD offer tube testing machines as well as both types of sealing machines to help you assemble the right set up for your business. That way you can have tubes sealed in an efficient way and have equipment on hand that tests the tubes at either end of the process to ensure top quality.
For more information on Does Your Process Need Tube Testing Machines? talk to MSD Ltd (Manufacturing Support & Design)
Enquire Now
List your company on FindTheNeedle.