
Introduction to Metal Alloy Heat Treatments
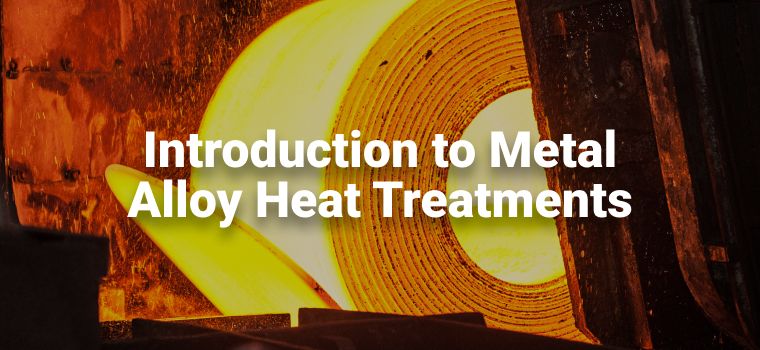
You may be familiar with a Blacksmith heating and hammering metal to a specific shape and then plunging the item into water (quenching), which usually makes the metal harder and less brittle. The quenching (cooling) of the metal is just one step, often the final step, in the process referred to as ‘heat treatments.’
Over time, Metallurgists have developed many different methods of alloy heat treatment and each ‘schedule’ or cycle refers to a different rate of heating, holding and cooling. When these methods are followed precisely, they can produce alloys of different standards with remarkedly specific physical and chemical properties.
Alloy Heat Treatment: Recrystallisation and Grain Structure
The recrystallisation temperature, also referred to as the critical temperature, is the temperature at which the crystal lattice structure of the metal becomes reoriented. The original grains are replaced by a new set of grains which nucleate and grow to replace the old structure.
Alloy heat treatment above the recrystallisation temperature alters the microstructure of the metal or alloy and can change several different properties needed for enhanced durability and performance. The metal is heated to a specific temperature, without letting it reach its molten, or melting, stage and then cooled in a specific and controlled manner. Additional heat treatments may be undertaken, or repeated, as required to achieve specific outcomes. Not all heat treatments use temperatures above the recrystallisation temperature.
While the alloy heat treatment will improve some properties it may worsen others, decisions must be made regarding the priorities of the end use and the operating environment.
Properties Influenced by Alloy Heat Treatment
- Strength – Extremely important in applications where the end-use application is exposed to extreme pressure, consider aircraft landing gear or the transportation of explosive gasses in high-pressure vessels.
- Ductility– In some applications, the metal must be deformed (or transformed) without losing toughness, therefore you need a material that is pliable and not brittle.
- Corrosion Resistance– In addition to any safety concerns, if parts need replacement due to corrosion it can be time-consuming and expensive. Chemical composition and heat treatments can extend the life cycle of materials in different operating environments
- Hardness – Required for many parts where tensile strength, yield strength or ductility may be required characteristics.
- Machinability – Increased malleability and workability during manufacturing. The material must be capable of handling any precision machining required during manufacturing, whether that is via a CNC or press brake.
Other benefits of heat treatment can enhance the electrical and magnetic properties of the metal, which can improve the compatibility of the metal with other materials.
The Stages of the Heat Treatment Cycle
Generally, there are 4 stages to the heat treatment cycle.
-
Heating– The material is uniformly heated to a specific temperature; this is done slowly to avoid uneven heating where one section may expand quicker than another leading to distorted or even cracked metal.The heating step is undertaken with consideration of the following factors: The heat conductivity of the metal, the history and condition of the material if previously hardened or stressed, the size, cross-section or shape of the material.
-
Holding – holding maintains the material at the specific required temperature for a specific duration to ensure the desired internal structure occurs. The holding period depends on the chemical structure, mass and shape of the material.
-
Cooling – The material is then cooled, often rapidly (quenching), this brings the material temperature back down to room temperature, how this cooling takes place affects the result, including hardness. Consideration must be given to the composition of the alloy itself and whether the cooling medium, air, gas, oil, water, or a combination of mediums is required to achieve the desired outcome.
-
Ageing– Ageing is used on solution heat-treated alloys to increase their strength and hardness while reducing their ductility. In some metals this is achieved naturally— simply by letting the metal alloy hang out for years – other alloys require artificial Ageing.
Artificial metal ageing is accomplished by re-heating a solution heat-treated alloy. The temperature is below the recrystallization point, but high enough to form precipitates (intermetallic compounds*1) a lot faster.
As soon as the precipitates are the appropriate size, structure and distribution the metal is rapidly cooled to prevent further growth.
*1 Intermetallic compounds involve two or more metallic or semi-metallic elements with an ordered structure and usually with well-defined and fixed proportions.
Example of Artificial Ageing Alloy Heat Treatment (Material Specification)
Alloy heat treatment may be included on a material specification, the example below is for the appropriate ageing heat treatment of alloy 718.
As stated in the material specification below, it is not required if the alloy already meets the requirement.
3.4.5 Ageing
3.4.5.1 Ageing is required unless the material is procured already aged per AMS 5663 to 150 psi (1034 Mph) minimum yield strength.
3.4.5.2 The Ageing heat treatment may be performed either on the raw material or after rough machining. In the latter case, the part must be cleaned again to remove all traces of oil.
The material shall be aged according to one of the following heat treatment cycles.
3.4.5.2.1 Cycle 1
- 718°C (1325°F) +/- 14° C (25° F) for 8 hours
- Furnace cool at 38°C (100°F) / hour to 621°C (1150°F) +/- 14°C (25° F
- Hold at 621°C (1150°F) for a total Ageing time of 18 hours
- Air Cool
3.4.5.2.2 Cycle 2
- 760°C (1400°F) +/- 14° C (25° F) for 5 hours
- Furnace cool at 38°C (100°F) / hour to 649°C (1200°F) +/- 14°C (25° F)
- Hold at 649°C (1200°F) for a total Ageing time of 8 hours
- Air Cool
Types of Common Alloy Heat Treatment
Annealing – is a method where a metal is heated beyond the upper critical temperature and then cooled at a slow rate by air, not by liquid or oil. The purpose of the annealing method is to soften the metal (by decreasing its hardness) and render the metal more suitable for cold working and forming. It also relieves stresses the metal may have due to prior cold working processes.
Annealing also enhances the metal’s machinability, ductility and toughness. There are several annealing techniques such as re-crystallisation annealing, full annealing, partial annealing and final annealing.
For further information on annealing, see our article:Annealing: What is it and how it works
Normalising – is a heat treatment process used for relieving internal stresses caused by processes such as welding, casting, or quenching. The metal is heated to a temperature that is 30-50° C above its upper critical temperature and is higher than the one used for hardening or annealing. After holding at this temperature for a designated time, it is cooled in air.
Normalising creates a uniform grain size and composition throughout the material. Steels in a normalised form are harder and stronger than in any other condition, making them suitable for handling massive external loads or impact strength.
Hardening – is used to increase the hardness of a metal. In some cases, only the outer surface may be hardened (case hardening). The metal is hardened by heating it to the specified temperature, then cooled rapidly, aka quenched, by submerging it into a cooling medium, which can be oil, brine, polymers or most commonly water.
The resulting material will have increased hardness and strength, but simultaneously the brittleness increases too. Case hardening uses the same method but only a thin outer layer is transformed resulting in a hard outer layer with a softer core.
Ageing – Ageing or precipitation hardening is a method mostly used to increase the yield strength of malleable metals. The process produces uniformly dispersed particles within a metal’s grain structure which subsequently changes the materials’ properties. Precipitation hardening usually follows another heat treatment process that reaches higher temperatures.
Ageing, however, only elevates the temperature to medium levels and brings it down quickly again. Some metals can age naturally at room temperature while others will only age artificially at elevated temperatures.
Stress Relieving – this method is common for boiler parts, air bottles, accumulators, etc. This method takes the metal to a temperature just below its lower critical border. The cooling process is slow and uniform. This is done to relieve stresses that have built up in the parts due to earlier processes such as forming, machining, rolling or straightening.
Tempering – Tempering is a method used to reduce brittleness and increase the strength of the metal. Most iron-based alloys are very hard and therefore very brittle. When tempered, these metals are heated to a temperature lower than the critical point. This reduces brittleness and maintains hardness.
Carburisation – In this heat treatment process, the metal is heated in the presence of another material that releases carbon on decomposition. The released carbon is absorbed into the surface of the metal. The carbon content of the surface increases, making it harder than the inner core.
Decarburization Involves the removal of carbon from the surface of steel, either by applying heat or through the normal ageing process of oxidation.
Nitriding – involves heating the steel in the presence of ammonia or other nitrogenous material, which adds nitrogen to the metal surface and produces case hardening without requiring any quenching. Nitriding also achieves a higher hardness on the surface than the carburizing method, which increases resistance to wear and tear and improves the fatigue life of the metal.
We’ve discussed alloy heat treatment, properties influenced by it, and the stages of the heat treatment cycle. For alloy heat treatment to be effective, it relies on the correct alloy choice. Reach out to us for guidance in selecting the NeoNickel alloy tailored to your application.
For more information on Introduction to Metal Alloy Heat Treatments talk to NeoNickel