
Dielectric Recirculation Pump for Test Rig
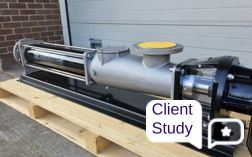
Dielectric Recirculation Pump for Test Rig
For our latest case study, we’re discussing a dielectric coolant pump we supplied for a client’s test rig.
As new equipment is developed or new fluids tested, a small scale rig is often built as a proof of concept allowing testing to take place, and for theories or limits to be checked before the full scale plant is built.
Test rig pumps are often a key part of the rig and enable testing of concepts and components. They’re also used in educational machinery to help students understand important engineering principles such as fluid dynamics.
A customer recently contacted North Ridge asking for a pump to help test dielectric coolant fluids on a test rig in both the UK and US, meaning that the pump would have to work at dual frequencies.
So what is a dielectric fluid?
It’s a dielectric material in a liquid state. Its main purpose is to prevent and quench electric discharges rapidly, which is why they’re used as insulators in high electric voltage applications such as capacitors, transformers, switchgear, high voltage cables and so on.
In addition, they provide electric insulation by suppressing arcing and corona, plus they serve as a dielectric coolant. A good dielectric fluid should have high dielectric strength, high thermal stability and inertness against the construction materials used, non-flammability, low toxicity, good heat transfer properties, and be low cost.
Dielectric fluids are also used in Electrical Discharge Machining (EDM) as de-ionised water, and this helps to improve their performance. As in the dielectric fluid, the micro-EDM process takes place, so the key properties of dielectric fluid like viscosity, dielectric strength, cooling capability, and chemical compositions play a key role in efficient and stable discharge during machining.
Some examples of dielectric coolant fluids include castor, silicone and mineral oil, heptane, benzene, hexane, de-ionised water, Fluorinert, and Novec.
How are they used?
In general, dielectric fluids maintain electric fields, cool heated electrical components, and provide electrical insulation. They are used in power transformers, capacitors and other equipment where their specific properties are required.
These days, dielectric fluids are being used more and more in data centres for immersion cooling. In this application, they have to operate 24/7 and be reliable, heavy duty and work at low RPM to ensure longevity in these demanding and mission-critical situations.
Why are companies starting to use immersion cooling?
Air or water cooling are the usual methods for cooling down servers in large data centres. However, the steady rise in global data centre energy consumption combined with the increase in server racks’ power dissipation mean that more energy efficient cooling methods have to be found.
In fact, data centres worldwide currently account for around 3% of global electricity consumption – that’s roughly equal to Japan’s overall annual energy use. More alarmingly, data centre energy consumption is nearly doubling every four years and has the fastest-growing carbon footprint of any area in IT– about the same as the global aviation industry.
The more sustainable solution
There are a variety of reasons why large companies and enterprises are migrating to immersion cooling using dielectric fluids.
Perhaps the biggest reason is sustainability. Traditional fan or water cooling methods account for about 40% of the total energy that data centres consume. Liquid cooling methods for instance, use an Olympic-sized pool of water every two days on average.
In contrast, immersion cooling is an ecological, energy-efficient way to bring huge energy savings, reduce a company’s carbon footprint, and provide one answer to the global energy challenges we’re all facing. There are more reasons why IT companies are switching to immersion cooling:
-
It enables chips to work harder
-
Saves energy compared to fan or water cooling which can make up over 50% of data centre energy costs
-
Reduces energy bills
-
Safer – it’s not electrically conductive so there’s no risk of electrocution
-
Environmentally friendly – it’s a natural, hazard-free biodegradable coolant
-
No fans and less noise mean a quieter working environment and better worker quality of life
What are single-phase and double-phase immersion cooling – and what’s the difference?
Single-phase immersion cooling
The servers and other IT components are submerged in a thermally conductive dielectric fluid. This never changes state, never boils or freezes and always remains in a liquid form. It’s pumped to a heat exchanger where heat is transferred to a cooler water circuit. This process uses open baths as there’s little or no risk of the coolant evaporating.
Two-phase immersion cooling
The servers and other IT components are submerged in a thermally conductive dielectric coolant fluid. Heat is removed from the system by circulating the fluid around hot components. The fluid then goes through a low-temperature evaporation process to cool the hot components and transfer the heat out of the liquid. The gas is cooled again by a heat exchanging method, such as a condenser coil, to enable return flow into the bigger liquid volume.
While the two systems are far above traditional air and water cooling methods in terms of efficiency, cost, and environmental friendliness, single-phase liquid immersion cooling works better than the two-phase technique. It’s the better option for cooling high-performance IT equipment.
Which circulation pump is best for dielectric coolants?
At North Ridge Pumps, we’re not tied down to a single pump technology. Using our experience, we can specify the best pump for any client and any application at the lowest lifetime cost. In short, we use our expertise to offer a bespoke solution - not something just off the shelf.
When looking for a cooling pump there are a number of criteria which determine the best pump - the required duty points, the daily hours of operation, the viscosity of the fluid being pumped and how friction losses may vary with pipe runs.
What’s more, different pump types will give different results. A positive displacement pump will transfer the same amount of dielectric fluid even if pressure losses change, for instance if the number of circuits needed to be cooled increases. In contrast, centrifugal pump flow will change according to the pump speed.
Materials used for circulation pumps can vary from cast iron for use with oils, to stainless steel, duplex metals or non-ferrous metals when used with more aggressive fluids, or to prevent cross contamination with high cost fluids, and ensure cleanliness.
In short, any pump specified for cooling should be engineered to meet any duty points demanded by the application - at both peak and off-peak demand.
Why we specified a positive displacement pump
At first, our client asked for a centrifugal pump for this application. However, we recommended that the customer look at a positive displacement pump for this process.
We selected a positive displacement pump because it would ensure flow rates would be proportional to speed, and discharge pressures would be constant. This would make conclusions much easier to be drawn than a pump in which both flow rate and pressure changed during the testing process. We would make these assessments using pump performance curves.
What is a pump performance curve?
Pump performance is governed by pressure losses in the system, with pumps producing different flows and pressures depending on conditions at the inlet. A pump performance curve is simply a diagram showing the flows and differential pressures being produced by a pump.
To enable us to specify a pump for a particular application and process, we need to know the:
-
Application
-
Fluid being pumped
-
Flow and pressure required
-
Viscosity of the fluid and its specific gravity
-
Temperature
-
Power available and the power medium driving the pump
Centrifugal pump performance curve
Centrifugal pumps are used in 70% of pumping applications, and their curves are generally a half-moon shape as shown above. The highest point on the left shows highest pressure but lowest flow. The far right end of the curve shows the highest flow but lowest pressure. The duty point is marked with the efficiency indicated in percentage.
Positive displacement pump performance curve
As you can see, a positive displacement curve is actually a straight line. This is because, unlike a centrifugal pump, a positive displacement pump flow is proportional to RPM and does not decrease with pressure. In addition, a positive displacement pump curve usually has a separate axis for viscosity, where the pump will show a flow against viscosity as below.
Specific client requirements
For this particular application, the client requested that the pump be able to operate at both 50Hz and 60Hz as the test rig was being used in both the UK and the US.
They also wanted to easily control the pump’s performance. To achieve this, we specified the pump with an integrated inverter allowing operators to adjust pump speed directly on the pump, without having to pay for an external control panel. This would enable low cost trials to be carried out without affecting the validity of the results.
Three ways we improved the pump’s cooling efficiency
Clearly, data centres around the world operate 24/7 and need cooling 24/7. This means that a pump’s power consumption will be its biggest cost and needs to be minimised as far as possible. To make sure that the pump operates as efficiently and cost-effectively as possible, there are a number of specifications we incorporated.
Operating a pump via a variable frequency drive will ensure that pump performance will meet the required cooling demand. Having a pump operate at low speeds ensures we don’t add to the problem. Having a pump working at high speed can add heat to the fluid which is then recirculating within the casing and needing further cooling.
Secondly, using surface-mounted pumps rather than immersion pumps can also help. Surface-mounted pumps draw fluid from levels in tanks where it’s hottest so cooling takes place more quickly, whereas immersion pumps draw fluid from the coolest part of the tank.
Thirdly, filtration might need to be used due to the dielectric coolant fluid becoming dirty or contaminated which can cause conductivity – the very thing we are trying to avoid. If so, we can specify a pump which is large enough to overcome additional pressure losses from a clogged strainer. This will help ensure that the pump always operate at the highest efficiency.
If you’re developing a new product or machine, are involved in the testing of a new fluid or are looking for dielectric cooling pumps for your process, speak to North Ridge Pumps to see how we can help.
For more information on Dielectric Recirculation Pump for Test Rig talk to North Ridge Pumps Ltd