
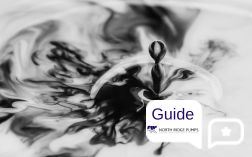
Understanding material codes is of paramount importance in multiple industries. They serve as the standardised language for describing the properties, composition, performance criteria, and testing methods for a range of different materials, from metals to polymers and ceramics.
Material codes enable clear comparisons to be made between materials, avoid misunderstandings between users and their use ensures operators can accurately identify the key attributes of a material such as its tensile strength, elasticity, thermal conductivity, or corrosion resistance helping determine its suitability for a specific application.
There are numerous material standard used worldwide, below is a brief explanation of some of the key material code standards:
-
DIN: Stands for "Deutsches Institut für Normung," the German Institute for Standardisation. It sets standards for materials and techniques in Germany and Europe.
-
EN: Short for "European Norm." One of the three European Standardization Organisations (ESOs) ratified it: CEN, CENELEC, or ETSI. ENs are used widely across Europe.
-
AISI: An abbreviation for the "American Iron and Steel Institute," which classifies different types of steel and iron based on their compositions and physical properties.
-
ASTM: Means "American Society for Testing and Materials." This organization develops and publishes technical standards for materials, products, systems, and services.
Material Code Equivalents
Material |
DIN / EN |
AISI / ASTM |
Cast Iron |
EN-GJL-250 (GG25) |
A48 Class 40B |
Nodular Cast Iron |
EN-GJS-400-15 (GGG40) |
A536 60-40-18 |
Nodular Cast Iron |
EN-GJS-400-18-LT (GGG40.3) |
A536 60-40-18 |
Cast Steel |
GP240GHGS-C25 |
A216 WCB |
Chrome Nickel Cast Steel |
GX5CrNi19-10 |
A351 CF8 |
Chrome Nickel Cast Steel (low carbon) |
GX2CrNi19-11 |
A351 CF3 |
Chrome Nickel Molybdenum Cast Steel |
GX5CrNiMo19-11-2 |
A351 CF8M |
Chrome Nickel Molybdenum Cast Steel (low carbon) |
GX2CrNiMo19-11-2 |
A351 CF3M |
Austenitic Cast Steel |
GX7NiCrMoCuNb25-20 |
A351 CN7M |
Austenitic Ferritic Cast Steel (duplex) |
GX2CrNiMoCuN25-6-3-3 |
A890 CD4MCuN |
Austenitic Ferritic Cast Steel (super duplex) |
GX2CrNiMoN26-7-4 |
A890 CE3MN |
Martensitic Stainless Cast Steel |
GX4CrNi13-4 |
A352 CA6NM |
Martensitic Stainless Cast Steel |
GX7CrNiMo12-1 |
A217 CA15 |
Stainless Steel 316 |
X5CrNiMo17-12-2 (1.4401) |
A479 (316) |
AISI 4140 Alloy Steel |
42CrMo4 (1.7225) |
A322 (4140) |
Cast Bronze (tin alloy) |
G-CuSn10 |
B427 C90700 |
Cast Bronze (nickel alloy) |
G-CuAI10Ni |
B148 C95500 |
Cast Bronze (Leaded) |
G-CuSn5ZnPb |
B584 C83600 |
Copper |
Cu-ETP (CW004A) |
B187 |
Chrome Steel |
X20Cr13 |
A276 Type 420 |
Chrome Steel (heat treated) |
X20Cr13 |
A276 Type 420+QT |
Chrome Nickel Steel |
X5CrNi18-10 |
A276 Type 304 |
Chrome Nickel Steel (low carbon) |
X2CrNiMo17-12-2 |
A276 Type 316L |
High Carbon Steel |
C45 (1.0503) |
A29/A29M (1.045) |
Duplex (austenitic-ferritic) Steel |
X3CrNiMoN27-5-2 |
AISI 329 |
Duplex (austenitic-ferritic) Steel |
X2CrNiMoN22-5-3 |
UNS S32205 |
Pure Aluminum |
EN AW-1050A (Al99.5) |
B209M |
Material Suitability Analysis
Below is a breakdown of some of the most common types of fluids, and what materials they are typically used with:
For Acids/Alkalis
-
Polypropylene (PP): Polypropylene is a robust thermoplastic polymer that exhibits exceptional resistance to acids and alkalis due to its hydrophobic nature. It is beige in colour and It's inert profile allows it to maintain its structural integrity even under prolonged exposure to these substances. It is widely adopted in chemical processing equipment not only for pumps but also within pipework.
-
Ultra High Molecular Weight Polyethylene (PE-UHMW): PE-UHMW is a subset of polyethylene characterized by its high molecular weight. It results in superior resistance to corrosive substances such as acids and alkalis. Its high tensile strength, impact resistance, and low absorption rate makes it ideal for applications demanding high chemical resistance.
-
Duplex Stainless Steel: Duplex Stainless Steel is a balanced mix of austenite and ferrite structures, providing excellent resistance to corrosive elements, including those with acids and alkalis. It boasts improved pitting and stress corrosion resistance, thanks to its high chromium, molybdenum, and nitrogen content, and used within chemical processing applications, and Oil and Gas applications including those involving seawater.
-
EPDM: Also known as Ethylene Propylene Diene Monomer, EPDM has a high resistance to corrosive chemicals, ensuring its longevity and reliability in challenging environments, and is frequently used in the handling of chemicals such as solvents, acids and alkalis.
-
CSM: Commonly called Hypalon, CSM is renowned for its excellent chemical resistance against concentrated acids and bases. It provides durability in harsh chemical conditions and has an excellent resistance with oxidative substances preventing loss of integrity or deformation.
For Fuels
-
Cast Iron GG25: This is one of the most commonly used Irons due to its low price point, quality and robustness meaning it is used widely in not only fuel transfer applications but also those involving clean water, waste water, effluent and sewage being used as a material for not only pumps, but also valves, pipes and strainers.
It is an alloy primarily composed of iron, carbon (2.5-3.5%), and silicon, has good wear resistance and durability. Although it can rust when not protected, this commonly only happens when in contact with air, and it has been known to be ok with use with low salinity seawaters. It exhibits excellent heat retention and even distribution heat exchanger applications used within fuel systems. It is however brittle as it contains flakes of graphite/carbon within its structure, meaning it can fragment under impact or when dropped as the material will break where the flakes of graphite /carbon lie within its structure. -
Ductile Iron GGG40: Has similar properties to cast iron but its structure is altered through the addition of magnesium which is added during casting causing the flakes of carbon/graphite within its structure to form balls which is why Ductile Iron is also known as Spheroidal Graphite Iron.
The balls are microscopic and with the addition of magnesium its structure now offers superior tensile strength, elongation, and impact resistance - attributes that are necessary for high-pressure applications involving fuel injection systems where robustness and reliability are critical. The ease in which it can be cast and machined allow for the production of complex components with precise geometries, which can improve fuel delivery efficiency and reduce waste. -
Cast Stainless Steel: Its impellers are used in a horizontal multistage pump to accommodate the demineralized water at temperatures up to 125°C. The material's inherent durability and resistance to corrosion are suitable for demanding high-pressure applications.
-
NBR: Nitrile Butadiene Rubber (NBR), often called Buna N, is an adaptable hose material compatible with oily and fatty substances. Its compatibility with a variety of hydrocarbons makes it suitable as a material for elastomers or internal parts in the fuel industry.
Cast Vs. Pressed Materials
Cast and Pressed materials are built differently. A defining feature of pumps constructed from pressed metal is that inlet and outlet fittings are usually welded to the pump casing which poses potential issues as the weld may leak due to perforation, chemical attack and such connections are not usually built to endure high pressure. The welds which can be performed in a differing material, are usually the first to be subject to chemical attack, can be affected when handling aggressive or non-compatible fluids and are more susceptible to damage by solids.
-
Stainless Steel (304 or 316): These materials are typically used to manufacture pressed pumps. They're light and easily shaped but may be prone to chemical attack at locations where the material has been welded and cannot handle high pressures or aggressive fluids. Pressed pumps made from these materials are often designed for clean fluids only.
-
Cast Iron: It is a popular choice for Cast pumps, often used in conjunction with plastics or rubber though lining to enhance durability. Cast iron impellers offer improved solid handling and have the added benefit of being also suited for clean fluids.
-
Stainless Steel 316L: This material is commonly used in cast and pressed pumps. The L designates Low Carbon and can be used for a variety of process fluids.
-
Aluminium Bronze: This material is utilized in cast pumps due to its compatibility with seawater. Bronze is typically a soft material and with the addition or aluminium and nickel its strength and resistance to sand, solids and high pressures is improved without risk of deformation.
-
Bronze: This is another material frequently used for cast pumps for use with seawater. Although its hardness is not as high as other cast materials, it is known for its durability being used for pump casings, impellers and even ships propellers. Bronze is cast and machined with relative ease enabling its use for complex shapes including impellers, yet still have the strength to handle solids without misshaping.
Material Strength Evaluations - Materials with Good and Poor Tensile Strength
Materials with Good Tensile Strength:
-
Ductile Iron exhibits excellent tensile strength due to its unique microstructure with brittle graphite nodules dispersed within its structure making it ductile with a strength ranging from 420 MPa to 700 MPa. It has high resistance to tensile loads and can be elongated without fracturing.
-
Natural Rubber (NR) Hosing is a resilient material that, when reinforced with a sturdy textile inlay, boasts enhanced structural integrity and increased tensile strength. The addition of the textile inlay not only strengthens rubber but also provides a high degree of flexibility and resilience, which is required for demanding applications.
-
NBR, NBR-A, and EPDM Hosing: NBR, its food-grade variant NBR-A, and EPDM all share a common feature – they are reinforced with extremely tough textile inlays. It contributes to their robust structure and imparts remarkable tensile strength, which enables these materials to withstand stress and strain levels without deformation or breakage.
Materials with Poor Tensile Strength:
-
Cast Iron (GG25): Despite its impressive compressive strength and excellent wear resistance, cast iron exhibits poor tensile strength due to its high carbon content and brittle crystalline flake structure. These properties cause cast iron to fracture under high tensile or shock loads.
-
Norprene A60F Tubing: Although this has a wide chemical resistance it is not reinforced meaning it has a low maximum pressure rating of only 2 bar.
Materials with Good and Poor Abrasion Resistance
Materials with Good Abrasion Resistance:
-
White Iron has superior abrasion resistance due to the high volume of hard, brittle iron carbides in its microstructure which provides a rigid matrix that resists wear.
-
Low-Carbon Chrome Nickel Steel has increased abrasion resistance due to the addition of chromium and nickel, which form a protective surface layer reducing wear rates.
-
Natural Rubber (NR) hosing has high abrasion resistance and can withstand intense friction or rubbing without substantial wear and tear. It is preferred in industrial applications where contact with harsh surfaces or abrasive materials is frequent.
Materials with Poor Abrasion Resistance:
-
Pure Aluminium: While it has many useful properties, pure aluminium has poor abrasion resistance due to its low hardness which can lead to surface wear in high-friction environments.
-
Low-Density Polyethylene (LDPE): LDPE has relatively poor abrasion resistance when compared to other polymers - it wears out quickly when subjected to friction and mechanical stress.
-
Copper: Despite its excellent thermal and electrical conductivity, copper is relatively soft and has low abrasion resistance. It is inappropriate for applications where high friction is expected.
-
Bronze - Bronze is known to have a low hardness and if particles / solids are expected to be encountered in an application, NiAL Bronze is preferred.
Materials with Good and Poor Impact Resistance
Materials with Good Impact Resistance:
-
High-Density Polyethylene (HDPE): This thermoplastic polymer is renowned for its high impact resistance, largely due to its high-density structure. What's more, it's commonly employed in applications requiring superior durability where pumps are made from solid block.
-
AISI 4140 Alloy Steel: A chromium-molybdenum alloy steel, AISI 4140, offers excellent impact resistance. It's used in applications requiring high structural strength.
-
Polyether Ether Ketone (PEEK): This high-performance thermoplastic possesses excellent impact resistance and mechanical properties, which are equally helpful for demanding applications like aerospace components and medical implants.
Materials with Poor Impact Resistance:
-
High Carbon Steel: Although incredibly strong and hard, high carbon steels lack good impact resistance due to their brittleness. They are only used in applications with desired hardness, including cutters on pumps, knives and cutting tools.
-
Low-Density Polyethylene (LDPE): LDPE is flexible and lightweight, but its low-density structure results in poor impact resistance. It's only suitable for plastic bags and film wraps.
-
Polymethyl Methacrylate (PMMA): Also called acrylic or plexiglass, PMMA offers good transparency and weather resistance, but its impact resistance is relatively poor, making it less apposite for applications requiring high durability.
Materials with Contamination Resistance
-
Polyvinylidene Fluoride (PVDF): It has excellent contamination resistance due to its high chemical stability and low reactivity, which allows it to resist corrosion and degradation even when exposed to harsh chemicals and environments.
-
Duplex Stainless Steel: Composed of approximately equal parts of ferrite and austenite, it has superior resistance to contamination. Its high chromium and molybdenum content gives it remarkable resistance to pitting, crevice corrosion, and chloride-stress corrosion cracking.
-
Norprene A60F Hosing: It is a thermoplastic, food-grade tube notable for its broad chemical compatibility. It is a suitable choice for environments where diverse chemical exposures from mixtures or CIP are expected. Its material composition ensures that it does not interact adversely with various substances it comes in contact with, minimizing the potential for cross-contamination, a critical factor in food processing, pharmaceutical, and biotech industries.
Materials for Aquaculture
-
Polypropylene (PP): Polypropylene is highly favoured in aquaculture due to its lightness, resistance to corrosion and chemicals, low impact on marine life and flexibility, all of which facilitate easy installation and durability in aquatic environments.
-
Stainless Steel 316L: This material is good for aquaculture due to its resistance to corrosion and biofouling. It provides enduring structures in freshwater and marine environments.
-
Norprene A60F and NBR-A: These materials are also good for aquaculture because they are both food-grade materials produced per FDA specifications. They also have low-pressure ratings and resist oily, fatty, and cleaning products.
For more information on Guide to Material Codes Their Equivalents and Optimal Applications talk to North Ridge Pumps Ltd