
High Pressure Potassium Hydroxide and Electrolyte Transfer and Recirculation Pumps Case Study
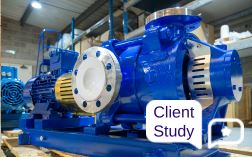
Our latest case study focuses on a project involving boosting high pressure potassium hydroxide and electrolyte transfer used in hydrogen production, where our multistage pumps were installed to increase system pressure which was deemed too low in the existing system.
What is potassium hydroxide?
Potassium hydroxide (KOH) is an electrolyte solution commonly called caustic potash. It’s an odourless, white or slightly yellow, flaky or lumpy solid which is often in a water solution. It has many industrial applications, most of which utilise its caustic nature and strong reactivity to acids.
It’s used for making soap, as an electrolyte in alkaline batteries and in electroplating, lithography, and paint and varnish removers. It’s dangerously corrosive, indeed, liquid drain cleaners are made up of 25% to 36% potassium hydroxide!
What is an electrolyte solution?
This is a solution that conducts electricity and usually contains ions, atoms or molecules that have lost or gained electrons. There are three types of electrolyte solutions: strong acids, strong bases and salts. Salts are sometimes also called ionic compounds, but strong bases are ionic compounds as well. The weak electrolytes include weak acids and weak bases.
What’s the role of the electrolyte solution in hydrogen production?
In the hydrogen production process, water is split into hydrogen and oxygen using an electrolyte solution, in this case, potassium hydroxide. It conducts electricity between two electrodes in a cell – an anode and a cathode - enabling the reaction that generates hydrogen gas. The cells are usually assembled in series to produce more hydrogen and oxygen at the same time.
The potassium hydroxide and electrolyte transfer and recirculation pumps used by our client in this production process need, most importantly, to supply the high pressures required. In addition, the system needs reliable and corrosion-resistant pumps to circulate the electrolyte and ensure a smooth and consistent exchange of ions. This is why we specified high pressure booster pumps.
What caused the low pressure in this system?
This could have been due to a variety of factors:
-
Part of the process reduced the system pressure too little for the next stage to work as intended
-
An addition to the system meant that equipment wouldn’t operate as designed without higher inlet pressure
-
Higher friction levels than forecast at design stage meant that system modifications were urgently required
How do high pressure booster pumps help?
Booster pumps are basically multi-stage centrifugal pumps which are installed within the pipeline and designed to accept the high pressures within the existing system, and add to these by generating higher pressures increasing flow and pressure within the closed loop system.
Multiple impellers generate higher pressures than can be delivered with the use of a single impeller at maximum diameter. This is because impeller side friction increases with size once it reaches a particular diameter. This in turn decreases pump efficiency. Therefore, to achieve higher pressures, it’s necessary to add several impellers along the same shaft in stages called ring sections. Each stage consists of an impeller and a diffuser.
When these extra impeller stages are added the flow rate is not changed, but the total head and shaft power increases proportionally to the number of stages. In short, multi-stage pumps are highly efficient, and what’s more, multiple duty points can be achieved by using variable speed drives and multiple outlets on the same pump.
What was our solution?
Here at North Ridge Pumps, we’re not tied to a single pump technology, so we can specify the best pump for a particular application – at the lowest lifetime cost. Indeed, we use our expertise to offer a bespoke solution, not something off the shelf.
For this particular project, we manufactured three multi-stage KOH booster pumps in AISI 316 stainless steel.
AISI 316 and AISI 316L are stainless, austenitic chromium-nickel-molybdenum steels which have good resistance to non-oxidising acids and chlorine-containing media. Due to the chemical composition, both 316 and 316L are inherently resistant to corrosion as this brief from our client required.
What’s more, the potassium hydroxide pumps were specifically designed to handle KOH in a plant where the system pressure needed was in excess of 40 bar, with our pumps handling an inlet pressure of up to 37 bar. Due to the high inlet pressures our pumps were built in a design variant containing a thrust bearing which is an additional highly performing bearing housing at the opposite end to the motor designed to balance the high radial loads and pressures within the pumps at intense duties.
Certified for use in explosive environments
The three KOH pumps were assembled with ATEX IP66 motors and non-sparking brass coupling guards.
ATEX is an abbreviation for the ATEX Directive and is short for Atmospheres Explosibles. It’s a set of EU regulations that are designed to ensure the safety of products, and identify the level of protection provided by equipment used in potentially explosive environments.
If a product or piece of equipment has official ATEX certification, it has been fully tested and approved to be safe to use in hazardous and explosive environments.
For example, ATEX-certified motors are explosion-protected electric motors which are used in industrial plants with a potentially explosive atmosphere containing flammable fumes. They meet strict safety specifications and ensure the operation can continue to run efficiently without the risk of explosion or failure.
In addition, two of the pumps required a motor with a slightly different standard hence the difference in colour.
They were also manufactured with a variety of different flange standards. This meant that they could connect seamlessly with process pipework of different specifications used in different regions or countries.
For more information on High Pressure Potassium Hydroxide and Electrolyte Transfer and Recirculation Pumps Case Study talk to North Ridge Pumps Ltd