
New Abrasion-Resistant Pump Enables Low Maintenance Resin Transfer for Formula 1 Team Case Study
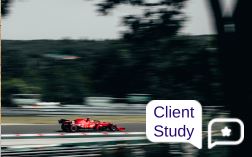
In this case study, we’re taking you into the fast-paced world of Formula 1, where reliable high performance is paramount and success is measured in hundredths of a second.
We were contacted recently by a leading Formula 1 team who were looking for a highly specialised resin transfer pump. This was going to be used to transfer a very abrasive ceramic-based high performance composite resin from a container to a machine which manufactured parts for the team’s Formula 1 car.
The liquid known as a high speed, high rigidity engineered nanocomposite was a key part of the production process, and had a low to medium viscosity of 700 to 1000cPs, but was highly abrasive and quick setting. What’s more, it was essential that the right pump was specified to prevent premature pump failure.
What is resin?
Resin is a highly versatile product with a wide range of uses. It can be used as an epoxy, which is the family of basic components or cured end products of epoxy resins. Also known as polyepoxides, epoxy resins are a class of reactive prepolymers and polymers which contain epoxide groups.
And what is epoxy resin?
This is a highly versatile, very durable and long-lasting form of resin which can be used for a large number of applications.
Most importantly, once it’s cured, epoxy resin is waterproof and this is one of the many reasons why it’s such an incredible sealant. Once it has finished bonding and curing, epoxy will prevent permeation by nearly any liquid or solid material, including water and humid air.
There are two main types of epoxy resin – single and two-part. Traditional one-part epoxies are rigid adhesives, often requiring a high-temperature thermal cure which produces outstanding strength at higher temperatures. They are the most environmentally durable adhesives, withstanding extremes of heat, cold, humidity, many solvents and other conditions.
Compared to single epoxy products, two-part epoxies need two elements to bond: resin and hardener. The hardener triggers polymerisation, which is the chemical reaction that bonds monomer molecules together to form polymer chains, which leads to curing. Two-part versions are stronger than one-part epoxies because of this strong bonding reaction.
How is resin used?
In Formula 1, resin is used in resin transfer moulding, a method for making components from fibre plastic composites. In this process, a reaction resin is poured onto the dry, semi-finished fibre parts and these parts are consequently immersed by applying pressure within a closed vessel.
Resin transfer moulding and infusion
Resin transfer moulding helps create components in a highly specialised range of industries from hi-tech aerospace components to boat building, and in this instance, for manufacturing high-performance composite components in small quantities for a Formula 1 car.
Another widely-used process is resin infusion for composites. In this method of production, resin is drawn into a dry laminate while it’s held under vacuum against a rigid mould by a sealed flexible membrane. The most commonly-used membrane is a disposable film or vacuum bag, and this film is sealed against the mould edges using a sealant tape.
Resin metering
For both these processes, precise metering and dispensing of the resin are essential. Measuring epoxy by weight is the most accurate way because you know the exact weight of each component. You'll need a scale sensitive enough to accurately measure the amount of resin and hardener you're mixing.
Recent developments in technology mean that more advanced pumps are now being used to dispense special resins.
However, there are several challenges that composite manufacturers face when it comes to pumping and metering resins.
One problem is that the thick and sticky consistency of the resin means it loses pressure when it’s pumped through a pipe. A single bend in the pipe will take away even more pressure. Therefore, it’s crucial that the resin dispensing pump can generate enough force to allow the viscous resin to flow freely at the desired rate.
Handling different viscosities
The viscosity of resins and their component parts can range from one to one million centipoise – the measure of viscosity usually abbreviated to cPs. Where water measures 1 cPs, thicker liquids like oil vary from 10 to 2,000 cPs depending on temperature, and an exceptionally thick and sticky substance like silicon can measure in the 100,000s cPs.
But whatever the viscosity, when pumping and metering resin it’s vital the materials that make up the resin are mixed to the correct ratio, and their combined flow rate must be totally accurate.
Resin dispensing
Once the resin has been metered, it then has to be dispensed. A resin dispensing pump system casts resin for the purpose of filling, sealing, covering or soaking technical parts.
To get the very best quality, the resin dispensing system has to be developed and optimised correctly, and work precisely to achieve accurate dispensing.
What’s more, because of constantly increasing cost pressures, casting devices must be capable of exceptional quality, while also being faster and more reliable. This is certainly true in Formula 1, where parts need to be manufactured quickly and to the most exacting tolerances.
So what was the project brief?
The resin transfer pump commissioned by the Formula 1 team was required to empty and refill vats of ceramic-filled resin, and had to achieve a reliable flow rate of around 800L/hour at 4 bar pressure.
However, there were a number of challenges to overcome. This particular liquid was a ceramic-based high performance composite resin which was extremely viscous and abrasive to traditional pump designs.
In addition, the resin would set prematurely if air leaked in, which can easily happen with pump designs which contain a seal. If resin sets in a pump it needs to be manually cleaned either by hand, or by being immersed in a solvent such as acetone.
Here at North Ridge Pumps, we use our expertise to offer a tailored solution, not something straight off the shelf. We’re not restricted to a single pump technology, so we can specify the best pump for a particular application and designed for the lowest lifetime cost.
After weighing up all of the options, we decided that a peristaltic pump would be the most suitable solution for a variety of reasons.
The benefits of peristaltic pumps
Peristaltic pumps are a simple design consisting of a single piece of hose connecting the inlet to the outlet. Rollers or shoes rotate slowly within the pump head compressing the hose against the casing creating a vacuum. This gently conveys fluid from the inlet towards the outlet.
The rotary motion of a peristaltic pump is very slow, which is why a gearbox is used to step down the motor speed to as little as 1rpm within the pump head.
For this project, the benefits of a peristaltic pump to our client were:
-
The resin dispensing pump could cope with the fluid’s high density, and be relatively unaffected by changes in the fluid’s viscosity
-
The pump is reversible meaning it could also be used for the emptying of tanks as well as resin transfer
-
Due to the predictable nature of the pump’s operation the client’s team could accurately measure flow rates, and ensure that the tanks were filled at a predictable speed without the use of flow meters which could also clog
-
We supplied the units with a motor-mounted inverter enabling the client to control transfer rates at the touch of a button
-
As the hose is the only part that wears out, peristaltic pumps are recognised as being very low maintenance.
For more information on New Abrasion-Resistant Pump Enables Low Maintenance Resin Transfer for Formula 1 Team Case Study talk to North Ridge Pumps Ltd