
Two Vertical Long-Coupled Inline Pumps to replace 50 year-old pumps at a quarry Case Study
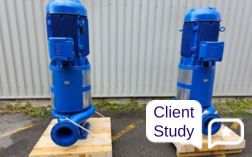
Two Vertical Long-Coupled Inline Pumps to replace 50 year-old pumps at a quarry – Case Study
Our latest case study focuses on a commission we received to replace two ageing pumps that had first been installed at a quarry around 1970.
In Europe, there are around 26,000 aggregates sites, nearly 60% of which carry out the washing of materials as part of the production process. For several years, the industry has taken action to encourage aggregate producers to continuously improve training, control of water consumption and their knowledge of water streams.
Environmental impact
In fact, water protection is a major challenge for aggregate operators who must be aware of their business’s impact on hydrology and hydrogeology, aquatic ecosystems, water resources, and the requirement to provide space to allow for the mobility of watercourses.
But they must balance this with the need to wash aggregates which is an essential part of the industrial process. It removes the fine particles naturally contained in the deposits and allows the product to obtain sufficient adhesion with binders like cement, lime, bitumen and so on. Therefore, a constant supply of water is crucial for production, and so are reliable, heavy duty pumps to pump the water.
Transferring water from the quarry ponds
Our client was looking to continue transferring water from ponds located on the site where it was then used for a range of processes within the quarry. This included the cooling of mechanical equipment such as saws, generators and plant equipment, as well as for the washing of sand and aggregate products like gravel and stones used in construction and landscaping.
The ponds are used because they recycle water, minimising the impact the quarry has on local water courses, and enabling the most cost-efficient operation of the plant. The pond water is treated and reused within the plant by the use of screens, and flocculation to remove contaminants.
What is flocculation?
This is the process by which a chemical coagulant added to water helps facilitate bonding between particles. This clumping effect creates larger aggregates which are easier to separate. Flocculation is widely used in quarries and water treatment plants, and can also be applied to sample processing for monitoring applications.
The client’s existing pumps were being used to draw water from the ponds located 4.5m below the pump suction. The client wanted to use their existing pipework which was DN150 outlet and DN200 inlet. In addition, they had also had problems with non-return valves on the inlet pipework, and wanted to see if these could be removed as they had failed in the past.
Vertical inline pumps can be made self-priming through the addition of air ejectors or a separate priming pump installed on the pump head. This evacuates the air enabling the pump to perform suction lifts at up to 6m.
The client looked at both of these options. However, because of the risk of solids being caught up in the water, we could not recommend an electric priming pump, and the client was not keen on using an air-driven ejector.
At North Ridge Pumps, we’re not tied to a single pump technology, but provide the best pump for a particular application and designed for the lowest lifetime cost. In fact, we can use our expertise to offer a bespoke solution, not something straight off the shelf.
The vertical inline centrifugal pump design has many benefits
We recommended vertical long-coupled inline pumps as they are a great space-saving pump with a reduced footprint size. They are easy to maintain through the addition of a spacer coupling bracket, which makes it possible to access the pump head without removing the motor.
This pump design is also more robust and designed for continuous use, thanks to the extra bearing bracket installed between the pump and motor. This takes a great amount of strain away from the motor during operation.
The vertical compact design means that the long-coupled pump can be installed where there is limited space. In addition, the back pull-out design allows the motor to be removed while the pump is still connected to the pipework. This in turn means that time can be saved while the pump is serviced and maintained.
Independent shafts
On this design, the centrifugal pump and motor have independent shafts. This means that only the pump shaft will need to be replaced if it breaks. Other less robust vertical centrifugal pumps on the market only use the motor shaft. So if the shaft breaks, the entire motor needs to be replaced.
A large spacer coupling is installed between the vertical inline pump and motor. This extra space protects the motor from fluid getting in if the seal fails. In addition, wear rings can be installed in the pump head. These are sacrificial parts that wear first, protecting the impeller and casing from wear, and prolonging the life of these parts and therefore the pump.
Variable Frequency Drive
The pumps operate via a Variable Frequency Drive (VFD) which enables them to work at various duty points.
What are the duty points for a pump?
The duty point of a pump includes the capacity, i.e. the flow rate, and the pressure also known as the total head of the system. Some commonly used units of measurement for pressure include psi, kg/m2, bar and so on. The head is expressed as a length measured in metres or feet.
The pumps were transferring pond water at rate of 319m³h, 52m head at a speed of only 1400rpm making the pumps ideal for operation for longer periods.
The motor needed to meet exacting specifications as it had to be suitable for operation via VFD, with two wired thermistors and insulated bearings. Due to the motors being 75KW and working in conjunction with a VFD, the insulated bearings prevent the circulation of current through them which can damage them and contribute to their failure.
To make maintenance and servicing easier, access to the inner parts like the mechanical seal and impeller is done by simply removing the outer cover screen on the spacer coupling bracket. Then the pump and motor shafts can be separated without taking the motor out.
For more information on Two Vertical Long-Coupled Inline Pumps to replace 50 year-old pumps at a quarry Case Study talk to North Ridge Pumps Ltd