
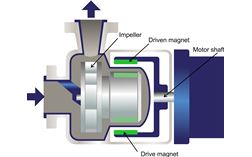
What Are Magnetic Drive Pumps and How Do They Work?
Magnetic drive pumps, or mag-drive pumps, are specialized industrial pumps that employ magnetic coupling to transmit torque from the motor to the impeller and eliminate the need for a mechanical seal. It leverages the attractive and repulsive forces of permanent magnets to create a hermetically sealed, non-contact transfer of energy between the motor and pump components.
In this article, we will delve into numerous aspects of magnetic drive pumps, including their applications, the advantages offered by their sealless construction, potential limitations and problems such as vibration issues, comparisons with canned motor pumps and traditional mechanical seal pumps, an overview of magnetic drive pump types like centrifugal and positive displacement pumps, and finally, an examination of maintenance best practices.
What Exactly Are Magnetic Drive Pumps?
Magnetic-drive (Mag-drive) pumps offer an innovative solution for chemical process pumping by eliminating the need for shaft seals. It significantly lowers the pump's initial expenses and ongoing operational costs because there is no need for mechanical seals, seal-fluid pots, or cooling lines.
The motor and pump drives are connected through a magnetic link that operates via an isolation shroud. Essentially, the incurred design ensures no direct or indirect pathways for fluids or gases to leak, which minimizes risks to operators and the surrounding environment.
Constructed from various materials, such as cast iron, ductile iron, 316 stainless steel, and Hastelloy, magnetic drive pumps provide versatility and contribute to technical standardization in process engineering through their universal applications. Moreover, these mag-drive pumps can be found in two variations: rotating shaft and stationary shaft.
How Do Magnetic Drive Pumps Work?
A magnetic drive pump operates by utilizing a balanced magnetic field to generate the rotation of the liquid impeller. It differs from a conventional centrifugal pump, which employs a direct drive connection between the impeller and motor, and incorporates a magnetic field.
An external magnetic bell housing is positioned at the end of the pump shaft; the bell is situated on the exterior of the rear casing. The pump impeller is linked to a smaller magnet assembly supported by an internal shaft and bushing assembly. Notably, there is no need for a mechanical seal since all liquid-end components are contained within the fluid head of the pump.
The smaller magnet assembly is placed at the center of the magnetic field generated by the external bell housing. Even though a fluid barrier separates the two magnet assemblies, their magnetic fields remain aligned. When the pump motor starts, the external bell housing starts to rotate, causing the rotation of the magnetic field to impact the inner impeller magnet. As both magnets rotate in unison, the impeller spins and moves fluid throughout the system.
Applications of Magnetic Drive Pumps
Chemical Processing: Magnetic drive pumps are employed in chemical processing plants to safely transfer corrosive, toxic, and even high-temperature chemicals, thanks to their leak-proof design and ability to resist chemical corrosion.
Some Chemicals which are often pumped with such designs include MDI (methylenediphenyl diisocyanate) and TDI (Toluene Diisocyanate) used in the production of Polyurethane.
Pharmaceutical Manufacturing: In the pharmaceutical industry, magnetic drive pumps ensure precise and contamination-free transfer of fluids, which is crucial for maintaining product purity and adhering to stringent regulatory standards.
Water Treatment: Magnetic drive pumps are utilized in water treatment facilities for pumping various chemicals, including acids, caustics, and disinfectants, due to their reliable, non-leaking design and chemical compatibility.
Semiconductor Fabrication: In semiconductor manufacturing, magnetic drive pumps are applied for efficient and safe handling of aggressive and high-purity chemicals, such as etchants and solvents, guaranteeing a clean, contaminatin-free environment.
Food and Beverage Processing: Magnetic drive pumps are beneficial for food and beverage processing to transfer sanitary, viscous, or shear-sensitive fluids while maintaining hygienic conditions and the integrity of the product.
Advantages of Magnetic Drive Pumps
The following are the five main advantages offered by Mag-drive pumps:
Productivity Enhancement
Mechanical seal replacement in pumps can impact operations through costs, labor, and downtime, potentially causing production delays and affecting the bottom line. Emergency maintenance can exacerbate disruptions and costs, including customer dissatisfaction and safety hazards. With their innovative design, however, magnetic drive pumps eliminate the need for mechanical seals and provide a hermetic seal by removing the direct connection between the motor shaft and the impeller assembly. It excludes potential leak points and eradicates the need for seal replacements, which reduces costs and labor over the pump's lifespan and ultimately benefits the bottom line.
Safety Improvement
Magnetic drive pumps frequently facilitate the transfer of hazardous chemicals in various fluid-handling applications. Leaks in other conventional pumps can pose a significant threat to workers by exposing them to these dangerous substances. Such exposure can occur abruptly due to a substantial leak or gradually by releasing liquid or vapors from a compromised seal.
Fugitive Emission Prevention / Volatile Organic Compounds
The presence of unstable organic compounds (UOCs & VOC’s)) and unstable hazardous air pollutants (UHAPs) is a significant concern for any establishment that employs chemical transfer pumps. Ineffective leak prevention in pumps can lead to the release of these harmful emissions and disrupt operations. Such emissions pose a threat to employees and the general public and expose pump owners to the risk of non-compliance with regulations. On the other hand, magnetic drive pumps help to mitigate these emissions while enabling businesses to adhere to local, state, and federal health and safety standards. Consequently, overall facility safety is enhanced, and the probability of facing penalties or closure due to non-compliance diminishes.
Dry Run Protection
A principal reason for pump malfunction is operating without fluid, often resulting from human errors or system disturbances. In such situations, pumps may continue to function with no fluid, which leads to rapid deterioration or destruction of the pump in many instances. Nevertheless, specific mag-drive pump configurations can withstand dry operation. In industrial settings where pumps do not receive continuous monitoring, this capability to function without fluid can expressively reduce the likelihood of pump breakdowns and related expenses.
Corrosion Resistance
Magnetic drive pump technology demonstrates an exceptional ability to endure highly corrosive and dangerous liquids. These pumps' robustness makes them appropriate for handling highly corrosive scenarios where other pump designs may falter. Due to their impressive durability, mag-drive pumps can manage fluids that overwhelm alternative pumping systems. As a result, these pumps provide a flexible solution for demanding tasks needing resilient responses.
Selection Simplification
Selecting the appropriate pump can be a complicated task. Numerous elements must be considered to determine the right pump for the intended use, and incorporating various seal alternatives (such as seal design, elastomer choices, and seal components) further complicates the decision-making process. However, magnetic drive pumps streamline the pump selection procedure.
Limitations/Problems with Magnetic Drive Pumps
Vibration: Magnetic drive pumps can experience excessive vibration due to imbalanced magnetic forces or misalignment of internal components, leading to premature wear.
Bearing Wear: In mag-drive pumps, the bearings operate close to the magnets, which can cause increased friction and wear and result in increased maintenance requirements.
Magnetic Eddy Current Losses: Magnetic drive pumps can generate eddy currents in the surrounding conductive materials. It causes energy losses and a reduction in efficiency, which is particularly noticeable in pumps that operate at high speeds.
Demagnetization Risk: Sudden temperature changes or exposure to external magnetic fields can cause demagnetization of the magnets in the pump, which leads to a decrease in torque transmission and reduced pump performance.
Limited Solids Handling: Magnetic drive pumps are generally unsuitable for handling fluids with high solid content or abrasives. The reason is that these solutions can cause excessive wear and damage to the pump's internal components.
Investment: Whilst such designs offer the lowest lifetime cost in applications when maintenance and spare part usage is taken into consideration, their initial purchase price is a higher investment to that of traditional designs of pump
Magnetic Drive vs. Canned Motor
The two primary types of sealless pumps, canned motor as well as magnetic drive pumps, differ in how the impeller rotates. Magnetic drive pumps use permanent magnets to create attractive, repulsive forces that spin the impeller. At the same time, canned motors employ a standard rotor and stator arrangement with an alternating current to generate a magnetic field that turns the rotor.
They also differ in size, operating points, and fluid containment. Canned motor pumps are more compact due to their integrated rotor winding and impeller design. Magnetic drive pumps can have their operating points modified by adjusting motor specifications, but canned motor pumps require a new pump for any alterations. While magnetic drive motors feature a single containment zone, canned motor pumps offer double containment with a sealed can (stator liner) encased within a pressure-proof motor casing, which ensures fluid containment even if the stator liner ruptures.
Magnetic Drive vs. Mechanical Seal
Magnetic drive pumps are increasingly preferred over double mechanical seal centrifugal pumps due to their cost-effective performance in hard-to-seal applications and handling hazardous, volatile, and aggressive chemicals. Compared to mechanical seal pumps, sealless magnetic drive pumps provide zero leakage, minimal installation and maintenance requirements, reduced monitoring needs, and maximized efficiency with substantial cost savings.
In addition, they also exhibit less mechanical loading on shafts and bearings, higher natural frequency due to their short design length, and improved safety by eliminating dynamic seals. Conversely, mechanical seal pumps require constant monitoring of barrier fluid levels and pressure, entail costly maintenance programs, and can experience increased bearing loads and dangerous vibrations during start-up and shut-down. Hence, magnetic drive pumps emerge as the safer and more robust option for chemical transfer by forgoing dynamic seals.
Types of Magnetic Drive Pumps
The following are the two major types of mag-drive pumps:
Centrifugal
These mag-drive pumps transfer fluids using centrifugal force and magnetic coupling principles. The impeller, attached to the rotating magnetic assembly, is driven by an external motor. As the motor rotates the impeller, kinetic energy is imparted to the fluid, creating a pressure differential and moving the fluid from the low-pressure suction side to the high-pressure discharge side.
The magnetic coupling, which is composed of an outer drive magnet and an inner driven magnet, allows for torque transfer from the motor to the impeller without needing a mechanical seal. Therefore, there is no possibility of fluid leaking out of the system.
Positive Displacement
Positive displacement magnetic drive pumps utilize the concept of volumetric displacement to move fluids at a constant rate, irrespective of the system pressure. They comprise a pair of meshing gears or lobes, a magnetic coupling, and a containment shell. In a typical configuration, one of the gears or lobes is directly connected to the rotating magnetic assembly driven by an external motor.
As the gears or lobes rotate, they expand and contract cavities and hence entrap a fixed volume of fluid while transporting it from the suction to the discharge side. The magnetic coupling, similar to that in a centrifugal magnetic drive pump, consists of an outer drive magnet and an inner driven magnet, which enables torque transmission without the need for a mechanical seal.
Mag-Drive Pump Maintenance Best Practices -23061911113404280.png)
Mag-drive pump operation best practices vary based on each model's specifications. For a non-self-priming magnetic drive pump, follow seven fundamental procedures:
-
Check Motor Fan Freely Rotates
-
Prime Pump
-
Open Suction Valve
-
Prepare Discharge Valve
-
Start the pump.
-
Check Rotation
-
Monitor power absorbed & Usage
So, following the above steps ensures proper flow and pressure and reduces the likelihood of operational problems. If any issues arise, troubleshoot using the tips provided below:
Troubleshooting a mag-drive pump involves addressing issues such as insufficient pressure, discharge, loss of prime, excessive power consumption, and excessive vibration or noise. You should also inspect various factors, like air leaks, priming, system head, motor speed, and rotation. Furthermore, regular maintenance is vital for optimal operation, with initial maintenance after six months or 2,000 hours of operation and ongoing annual examinations. Remember that maintenance schedules may vary depending on the pumped fluid and the specific application.
Conclusion
Advancements in pump technology have led to the development of smaller, more powerful, and more efficient magnetic drive pumps. They use rare earth alloy magnets and improved bearing designs for longer lifespans, reduced power losses, and decreased maintenance downtime. Various designs are also available for different applications, including handling solids, self-priming, and pumping many challenging liquids. Mag-drive pumps cater to a broad spectrum of viscosities, temperatures, capacities, and pressures while ensuring zero leakage of the pumped medium.
If you have any questions about Magnetic Drive Pumps, speak to us to see how we can help.
For more information on What Are Magnetic Drive Pumps and How Do They Work? talk to North Ridge Pumps Ltd